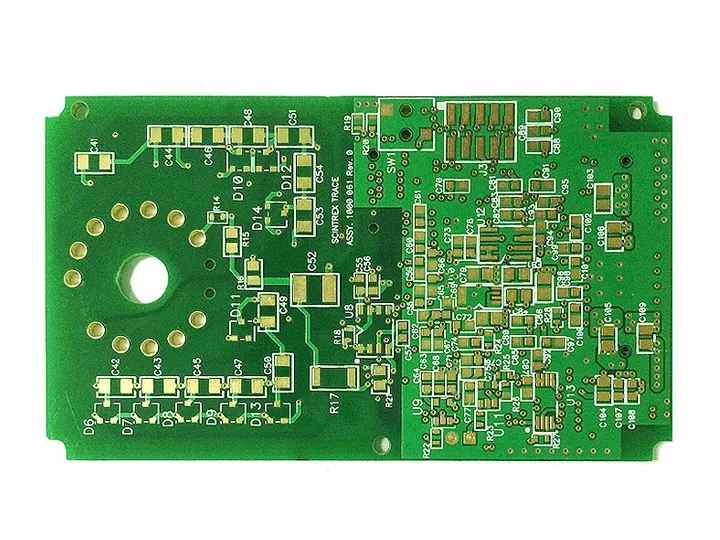
The influence of right angle wiring in PCB design of PCB manufacturers and the inspection method of PCB thermal design
Right angle routing is generally required to be avoided in PCB wiring, and it has almost become one of the standards to measure the quality of wiring. How much impact will right angle routing have on signal transmission? In principle, right angle routing will change the line width of the transmission line, resulting in impedance discontinuity. In fact, not only right angle wiring, sharp angle wiring, but also sharp angle wiring may cause impedance changes.
The influence of right angle routing on the signal is mainly reflected in three aspects: first, the corner can be equivalent to the capacitive load on the transmission line to slow down the rise time; Second, impedance discontinuity will cause signal reflection; The third is the EMI generated by the right angle tip.
The parasitic capacitance brought by the right angle of the transmission line can be calculated by the following empirical formula:
C=61W(Er)1/2/Z0
In the above formula, C refers to the equivalent capacitance of the corner (unit: pF), W refers to the width of the wiring (unit: inch), ε R is the dielectric constant of the medium, and Z0 is the characteristic impedance of the transmission line.
As the line width of right angle wiring increases, the impedance at this point will decrease, which will cause certain signal reflection. We can calculate the equivalent impedance after the line width increases according to the impedance calculation formula mentioned in the transmission line chapter, and then calculate the reflection coefficient according to the empirical formula: ρ= (Zs-Z0)/(Zs+Z0). Generally, the impedance change caused by right angle wiring is between 7% - 20%, so the maximum reflection coefficient is about 0.1.
Test Methods for PCB Thermal Design
The practical application of thermoelectricity is, of course, to measure temperature using thermocouples. The complex relationship between electron energy and scattering makes the thermoelectric potentials of different metals different from each other. Since the thermocouple is such a device, the difference of the thermoelectric potential between its two electrodes is an indication of the temperature difference between the hot end and the cold end of the thermocouple. If the thermoelectric potential of all metals and alloys is different, it is impossible to use thermocouples to measure the temperature. This potential difference is called the Scebeek effect. For a pair of conductors A and B of different materials, one contact is maintained at temperature T1, and two free ends are maintained at a lower temperature To. Both the contact and the free end are located in an area of uniform temperature, and both conductors are subject to the same temperature gradient. In order to measure the thermoelectric potential difference between free ends A and B, a pair of conductors C of the same material are respectively connected to conductors A and B at the temperature to and connected to a detector at the temperature T1. It is obvious that the Seebeck effect is by no means a phenomenon at the connection point, but a phenomenon related to the temperature gradient. In order to correctly understand the performance of thermocouples, this point cannot be overemphasized.
Thermocouple temperature measurement has a very wide range of applications, and the problems encountered are also diverse. Therefore, this chapter can only cover several important aspects of thermocouple temperature measurement. Thermocouple is still one of the main means of temperature measurement in many industries, especially in steel making and petrochemical industries. However, with the development of electronics, resistance thermometers are more and more widely used in industry. Thermocouples are no longer the only and most important industrial thermometers.
Compared with thermocouple (resistance measurement and thermal potential measurement), the advantage of resistance thermometer lies in the fundamental difference in the working principle of the two components. The resistance thermometer indicates the temperature of the area where the resistance element is located, which is independent of the temperature gradient of the lead and along the lead. However, the thermocouple measures the temperature difference between the cold end and the hot end by measuring the potential difference between the two electrodes at the cold end. For an ideal thermocouple, the potential difference is only related to the temperature difference at both ends. However, for an actual thermocouple, some non-uniformity of the thermocouple wire at the temperature gradient will also cause the change of potential difference, which is still a factor limiting the accuracy of the thermocouple. PCB assembly, PCB design, and PCB processing manufacturers explain the right angle wiring and PCB thermal design in PCB design.