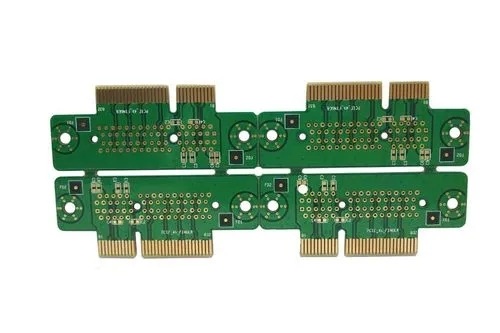
PCB Design Factory: What does rugged electronic design include?
Try searching for "rugged electronic products" on the Internet, and you may find many videos showing people stepping on smart phones. Robust electronic equipment needs to withstand the impact mechanically, but a robust system has more than just withstanding the fall on the sidewalk. This is not only about housing design, but also about component selection and manufacturing selection.
Military aviation designers often use the term "harsh environment" to describe many scenarios where the reliability and life of electronic equipment will be tested. If you want your next product to be truly rugged, it helps to adopt some of their strategies in your PCB layout. In this paper, we will study some design strategies used in military aviation design, as well as those used in industrial design.
What is the harsh environment in rugged electronics?
The term "environment" as defined in some industry standards can refer to anything from actual environmental conditions (temperature, humidity, etc.) to mechanical environments (e.g. vibration) or electrical environments (noise, ESD potential). Rugged electronic equipment is usually designed to withstand one or more of the conditions common in harsh environments:
Temperature too high or too low
Extreme and frequent temperature cycles
Moisture and high/low pressure
Mechanical vibration or shock
High voltage/current discharge
Particulate matter, such as dust
Oxidizing or explosive gas
This is a very extensive and incredible list. Typically, you cannot design a single device to withstand all of the factors in the above list. The harsh environment is difficult to deal with, because there are so many factors that can damage electronic equipment. These problems may affect the circuit board, components, the entire PCBA, or all of the above.
Some reinforcement strategies
The following table summarizes some of the solutions you can implement in your design to make it more robust and better able to withstand the above list of environmental factors.
environmental factor
design strategy
high temperature
Conductive cooling combination (chassis/radiator), using thermal interface materials and fans, diffusing heat components, using ceramic or metal core PCB boards, liquid cooling
low temperature
Use inlet protection to prevent condensation, and use direct current heating to keep the components within the normal operating temperature range
Extreme thermal cycle
Use high Tg laminate, do not use stacked vias.
High pressure environment
It is also planned to design for extreme temperatures, select appropriate components that will not implode, apply conformal coatings and fill the enclosure with inert gas or insulating liquid
Mechanical vibration or shock
Select through hole components as far as possible, design circuit boards, make the lowest resonant frequency at least three times of the expected impact frequency, and weld large ICs directly to circuit boards instead of using sockets or grid arrays
discharge
Keep the grounding close to the chassis and TVS grounding, and use ESD to protect the circuit
particulate matter
Use three proof paint to prevent ESD, and use high-pressure sealing shell to prevent particles from entering
Corrosion by moisture or oxidizing gas
Use conformal paint with appropriate chemical composition to design a sealed enclosure with high pressure rating
Explosive gas
Eliminate any components that may produce expected sparks during operation (such as relays), and apply ESD protection measures
It can be clearly seen from the above table that the reinforcement spans the slab level. Some solutions can only be implemented at the board level, while others need to consider all aspects from boards to components and shells. Some industry standards governing these solutions include:
Intrusion Protection (IP) standard to limit moisture intrusion in rugged electronic equipment
MIL-S-901D, which specifies the requirements for high impact mechanical impact of shipboard equipment
MIL-STD-810G, which specifies the test requirements for commercial military equipment
National Electrical Manufacturers Association (NEMA), specifying enclosures, cabinets, and enclosures
National Fire Protection Association (NFPA), which specifies a series of requirements for electronic equipment in certain environments to ensure fire suppression or containment
Potentially Explosive Atmospheres (ATEX), NFPA 497, and HazLoc specify design requirements to prevent explosion when deploying equipment in environments containing explosive gases
Your housing and installation method are important
So far, we have only discussed electrical design, physical layout and PCBA. Obviously, designing solid electronic products requires more than placing a thicker plastic shell around the PCB board and finishing the work. Enclosures, circuit board mounting methods, and fixtures will play an important role in determining reliability and countering some of the environmental factors listed above.
A simple way to address mechanical shock and vibration and potential electrical/thermal factors is to use shock absorbers.
Other aspects of enclosure design and installation will need to consider the specific environmental factors you need to address. Adapting to environments with high pressure gas will not use the same strategy as for high-pressure liquid environments, even though both are shell level solutions that rely on pressure equalization. Strong electronic design is a good example. The electrical design team needs to communicate closely with the mechanical team to ensure that the reinforcement strategy does not interfere with electrical requirements.
Final ideas on rugged electronics
The last piece of advice I can give about rugged electronic devices is that you will not always deploy devices in scenarios that contain an entire list of harsh environments. Therefore, the first step in designing a rugged electronic product is to consider the specific environmental factors that may damage the product and pay attention to these factors in the design. For example, if you are primarily concerned about temperature cycling, do not worry about designing protection for oxidizing gases (although you may get this protection as a side benefit). By focusing on what is important to your design, you can still produce a compact and cost-effective product. What steps does the circuit board assembly and circuit board processing manufacturer introduce to the robust electronic design?