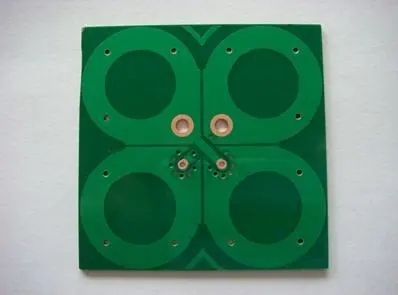
How to ground in the isolated power PCB board layout? What to do?
Most designers who use desktop power supplies may use isolated voltage stabilizing (switching) PSUs plugged into the wall. Everything needed to provide a stable power supply at a specific DC or AC level is built into the unit, and the noise is relatively low. As a designer, you don't need to do anything except connect some leads to the circuit board. Unfortunately, a real system with an integrated power part, or even just a power regulator module that you want to integrate into a larger system, is not that simple, and requires some custom design to ensure that they work correctly.
An important aspect of integrating the power supply into the system is to properly set up and connect the grounding, even for isolated power supplies. If you integrate the isolated power supply with the rest of the main circuit to the circuit board, you still need to ground in the system. These rules even apply to PCB boards of isolated DC chargers or DC power adapters, because the design may need to be connected back to earth, depending on the application and safety issues. Because poor grounding connection will cause noise problems, even security risks, let's look at the best practices of creating grounding connection in the power regulation section when converting AC power to DC power on the circuit board.
Grounding structure in isolated power supply
Suppose you are designing a system that needs to perform power conversion (AC to DC), regulation, and transmission to the circuit in the design. If you consider the actual structure of the system, there are three different options that may be used on the ground:
Grounding: This is a real grounding electrical connection, which exists as a safety wire (PE) on a 3-wire AC line.
Chassis grounding: This applies to enclosures with metal components, where the metal in the enclosure is used to create a grounding connection.
Signally: This is sometimes incorrectly described as analog and digital (don't separate your land like this). Signal ground usually refers to anything except ground or chassis.
Power supplies built with transformer coupling, such as AC-DC converters, DC-DC switching converters, or a combination of these two systems, will be built with transformers to compensate for these gaps in the PCB layout. The reason is simple: unless you only operate under low voltage and low current, you usually want to isolate in the design to protect users from safety hazards.
For various reasons, these grounding systems are not always located on a single ground plane. This applies to switching power supplies, especially more complex power supplies, such as LLC resonant converters. The reason why grounding is so important is that it defines the voltage that is measured when the component is operating in the system. When I write "voltage measured by one component", it means that the 5 V signal defined on a certain grounding area in the system may not be measured under 5 V when measured on a certain other grounding area in the system.
This problem in isolated switching power supply is called "ground offset", which will cause noise problems. This is important because the ground offset in the system may only be a small fraction of the voltage that you want to reliably supply in the transformer coupled power supply.
DC isolation can be maintained by capacitor grounding
Fortunately, there is a simple solution: connect the planes together with capacitors. Class Y capacitors are a good choice for higher voltage/current designs. You can easily do this in the schematic diagram: just find the components required by your capacitor, and then connect the bridge grounding network directly. A typical location for performing this operation in a PCB layout is close to the transformer.
Although it is still effective in AC-DC conversion, a more complex method is to use capacitors between the power rail and the AC side of the system. The ground offset between each side is eliminated by extracting and releasing some displacement currents. The circuit board assembly, circuit board design, and circuit board processing manufacturers explain how to ground the isolated power PCB circuit board layout? Do you know what to do?
Note that this applies only to the two grounded areas on the board. We have not considered the chassis or the earth. However, you can take some basic steps to ensure that the housing, circuit board, and ground are properly connected together. Unfortunately, this is not so simple. It is necessary to consider how noise and current play a role in the system, and whether they cause safety hazards. The following are some resources for further reading to help you determine the best way to connect to ground while maintaining isolation.
About grounding in electronic design and PCB layout
Isolated and non isolated power supply: correct selection
Define power grounding: system, chassis and grounding in PCB
How to Route Through Ground Plane Gaps
If you want to implement control algorithms for your power system, you will need to allow feedback from the output back to the input so that output power can be sensed. This means that you need to physically run a line from the output side of the regulator to the input side containing the switching elements. The question is: If your output is DC, but you want to keep isolation, what is the best method?
The answer is to use optical couplers. It is not appropriate to place wiring on the gap, because wiring will receive external noise, while switching power supply will produce a lot of noise. Transformer coupling is also not available because you are adjusting the DC. In the following diagram, the optical coupler spans the isolation between the ground planes, so we maintain the required isolation in this power supply.
Optocouplers allow you to send signals across ground plane gaps without wiring.
After placing the optocoupler, you can route the output to the power controller. Microcontrollers with PWM outputs are a good choice for custom power controllers, although some companies produce MOSFET gate driver controllers with feedback inputs and some external resistors. If you are designing very precise power regulation or you are experimenting with control algorithms, this is a simple solution to achieve output detection. You can then use standard control algorithms to adjust the frequency of the PWM controller to ensure maximum efficiency or specifically track the desired power output. The circuit board assembly and circuit board processing manufacturers explain how to ground the isolated power PCB circuit board layout? Do you know what to do?