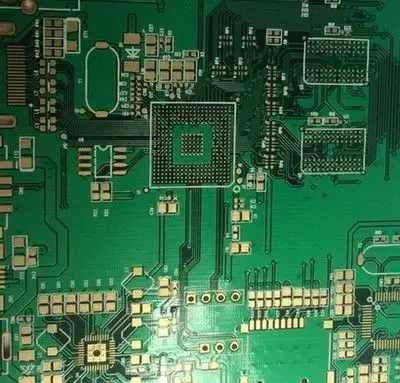
PCB layout guide sharing of switching power supply and voltage regulator
Power supplies and regulators can come in a variety of shapes and sizes. Although they are usually discussed as different products, they are electrically equivalent, especially switching regulators. From the perspective of advanced systems, the switch regulator part of the power supply and the actual regulator circuit perform the same functions in the same box diagram.
For the power supply, it is only a matter of scale and how the regulator integrates with other power conversion modules in the system. The switching regulator section in the power supply and the switching regulator circuit on the PCB shall be arranged according to the same general guidelines to ensure low noise operation.
In the next section, I want to briefly focus on the differences between the power supply and the voltage regulator, although most designers already know that. The power supply will (or should) include a power regulator, but the regulator can be an independent circuit, not a so-called power supply. For power supply and PCB with on-board voltage regulator, the layout of switching voltage regulator will be the main factor determining the overall system performance. Therefore, we will mainly focus on some switching power supply layout criteria in terms of regulator layout.
System Layout Criteria for Switching Power Supplies
Before looking at the regulator part of the switching power supply, we should first look at the high-level block diagram of the entire system. If you are designing a power supply, the entire device will have the topology shown below. This is particularly important for AC power from wall outlets.
High level block diagram of switching power supply.
The above block diagram can be implemented on multiple boards, although usually everything is placed on one board to leave room for large transformers, radiators, fans and mechanical mounting brackets, especially for high voltage/current power supplies. If you are designing a small voltage regulator for the circuit board to be inserted into the power supply unit, you will work in the above topology anyway, and you will have only one ground wire between the output voltage regulator and the new voltage regulator. Again, this is common for high current power supplies.
We have three separate grounding areas, which are tied together with the cap. Do not blindly follow the guidelines for using caps: there is no PCB grounding technology that can solve every noise source, so you should be very careful when using the caps. As shown in the figure, this is a method to ensure that all grounding areas have a constant grounding potential. This is a recommended method for grounding industrial Ethernet systems. The idea here is to prevent any DC potential that may be generated between two grounded parts
The danger here is that ground loops and common mode noise will be generated, which must then be filtered. In this way, binding the grounding wires together is basically the work done with a metal case, while the plastic shell will keep the grounding wires isolated. This becomes tricky and requires careful circuit design and PCB layout to pass all EMC tests.
Output stage
Current isolation on the output stage is not required; It depends on the topology of the DC regulator (see Flyback Converter for an example). Generally, a conducted EMI filter circuit or common mode choke is placed at the output to suppress the common mode current reaching the load circuit. In addition to these points, the output regulator stages will be arranged using best practices specific to the regulator topology. I will introduce these broader ideas about the layout of regulators below.
The output stage of the power supply may not be the final regulator in the system. Instead, another regulator or a series of regulators can be powered, and each regulator will provide a set voltage for a group of components at a certain maximum current. Again, this can be done on a single board or on multiple boards (one for the power supply and one for the regulator stage):
Layout each circuit block
Now, we can see the architecture of the whole system, and we can roughly understand how to lay out the switching power supply and each circuit module in the whole system to ensure low EMI and safety.
Sectional layout: Like other circuit boards with multiple function blocks, try sectionalized layout of power boards. This can be done linearly from input to output in the block diagram.
Plan a layout with feedback: sometimes, for example, in a precision large current regulator, there will be some feedback between parts. Use optical couplers to bridge the ground gap between each section.
Follow the grounding circuit: If there are general guidelines in PCB design, it may be "Follow the grounding circuit". For power supplies, this is essential to determine where common mode current can be generated and to ensure a low loop inductance in each power section.
Pay attention to high current and high voltage rails: High voltage and high current designs can sometimes be mixed together. The maximum potential difference between two conductors will determine their minimum spacing, and the current carried by the conductor will determine its required width to ensure low temperature
Optocouplers are small ICs that can be used to bridge data or sense signals across two electrically isolated grounded areas. The optocoupler (U4) is used in the LLC resonant converter as part of the feedback loop with the current detection amplifier to precisely adjust the switching frequency of the converter.
In the PDN design part, you should also consider how to ground each part and how to tie the grounding together to provide a consistent reference potential. As I mentioned earlier, this is very important to prevent EMI. This should be done before starting to process PCB layouts.
Layout Skills of Power Switch Regulators
After selecting components for the voltage regulator, creating the schematic diagram and designing the grounding/distribution strategy, you can start to consider the PCB layout. The PCB layout of the switching power supply regulator needs to be balanced: you need to balance the conductor size and electrical clearance requirements, but you need to make the structure compact.
Always implement minimum clearance and routing width rules for your system.
Shorten the voltage/current detection feedback line for the most direct route as much as possible.
You may have to gather some control and detection components around the drives and controller ICs, so make sure to establish a short connection between them. These components can be clustered in a narrow area (see below).
If large current is to be designed, consider using thicker copper or even metal core PCB.
Do not be afraid to use polygons as mounting pads for components or connectors. Be careful when strapping directly back to the aircraft, as you may need to dissipate heat.
Even though regulators can be very efficient, they can still get hot. Make sure to leave space in the layout to accommodate any radiators (if any) on the IC. Another option is to use thermal interface materials.
Some parts of the switching power supply layout may be very tight and may have wider rails/polygons. Don't be afraid to use these elements to ensure that you operate at safe temperatures and create a low inductance layout.
Specific layout guidelines for switching regulators will depend on topology, number of components, presence of feedback, and grounding strategy. I hope you have considered grounding to prevent EMI and provide the required isolation before starting PCB layout. To view some more specific guidelines for your specific regulator, please see the following additional resources:
How to Design a Booster Regulator
Isolated and non isolated power supply: correct selection without fault
LLC resonant converter design and PCB layout
Low noise, low EMI regulator
What are we not covering?
Obviously, there are many factors to consider in the above layout guidelines for switching power supply and regulator circuits. What is lacking? In the above discussion, some key aspects of power regulation and transmission did not appear:
PDN impedance: If you do not design high-speed/high-frequency components, you may not need to worry about PDN impedance. Just make sure to use a fertile power rail and a large amount of ground. If you are designed for high speed/high frequency, low PDN impedance is very important for suppressing ripple, which usually requires a large number of decoupling capacitors and high inter plane capacitance.
Power EMI: I mentioned this above. Whenever you create a PCB layout, you should consider ensuring low EMI. However, there are still many things to do besides suppressing EMI and routing EMC tests through the low loop inductance.
Analog power supply: Here, we are studying the switching converter usually discussed in digital ICs. What about analog components? Their electricity needs may vary considerably. Digital ICs that send analog/RF signals usually do this internally. However, there are special LDOs (such as NCP161BMX280TBG) or switching regulators (such as LTC3388IMSE-1).
There is also the problem of component selection, such as selecting inductors to ensure low EMI and common mode noise coupling, and ensuring low ripple current. Because the layout style of pure analog circuit is different from the power regulator or embedded power supply of digital system. Once you operate at very high frequencies, RF power problems are more difficult to solve due to parasitic capacitance (similar to what you see in unstable amplifier circuits). PCB assembly, PCB manufacturer's explanation of switching power supply and voltage regulator PCB layout guide sharing.