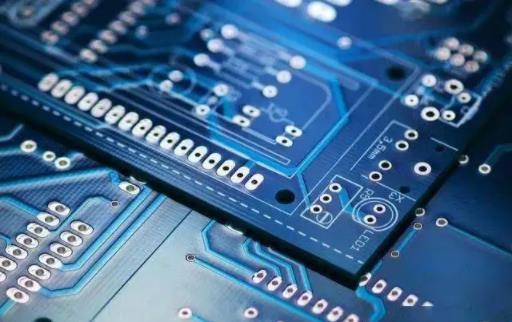
Analysis of 10 Possible Reasons for PCB Design and Assembly Failure
Understanding why PCB design assemblies fail and how to correct them is a key part of PCB design. PCB design requires time, energy and knowledge. However, if your PCB fails, all this hard work is futile. Therefore, let's take a look at the main reasons for the failure of PCB design and assembly.
10 Possible Reasons for PCB Design and Assembly Failure
1. Component design failure
Incorrect placement of parts, power failure and overheating caused by insufficient space on the PCB are just some examples of possible errors in the design and manufacturing stages. Related issues:
Welding problems
Chemical (liquid) leakage
Broken component barrier
Placement of defective components
Burned parts
2. Poor quality components
Tight placement of printed lines and paths, poor cold solder joints, poor connectivity between circuit boards, insufficient thickness of circuit boards, and the use of counterfeit components are common examples of poor PCB quality. Related issues:
Major defects
Bending and fracture
3. Environmental factors
Exposure to high temperature, dust and moisture, accidental impact (drop) and power overload/surge may be the cause of circuit board failure. However, the most destructive reason for premature failure of the circuit board is electrostatic discharge (ESD) during the assembly phase. Related issues:
4. Aging
Failure caused by aging cannot be avoided, but the cost of replacing parts can be controlled by replacing old parts with new ones. This is more cost-effective than new PCB assembly.
Thermal stress
5. Chemical leakage
The presence of any chemical fluid leaking from the assembly can severely damage the PCB and cause failure. Most chemicals are removed during manufacturing, but trace elements are usually left behind. In the packaging of components, leakage may occur, leading to rapid aging of semiconductors or packaging. Such chemical leakage may eventually lead to short circuit or corrosion.
6. Problems during welding
Solder is a component that provides the necessary contact mode between components and circuits. Without it, PCB will not work. There are some solder problems that may cause failures, but the most common are flux contamination and poor processing conditions. Some flux residues will absorb moisture, which may conduct electricity, causing a short circuit. If the welding process is not set up and controlled correctly, it may lead to joint cracking and solder contamination
7. Component barrier is damaged
The barrier of the component can protect the component from the external environment and provide a way for the component to connect the circuit. If this barrier is broken, the component will be exposed to environmental factors such as oxygen and moisture, which may lead to component aging and then failure.
8. Physical problems of materials
The materials used in PCB usually encounter problems that will lead to the failure of PCB. In the manufacturing phase, if one layer of PCB is misaligned, it will lead to short circuit, open circuit and signal line crossing. If the material has psychological defects, such as fracture, cavity and delamination, the performance of PCB will be seriously affected. Failure may also occur if the material used is impure.
9. Thermal stress
Stress from heat or moisture is one of the biggest causes of PCB failure, especially when multiple materials are used. Different materials have different expansion rates, so when a constant thermal stress is applied, it may damage the solder joints and components. If the wrong copper weight is used, or there is a coating problem, this will increase the stress from the thermal factor. Even in the manufacturing process, the temperature of the room where PCB is assembled will affect its performance.
10. Fabrication and Cleaning
Most fault problems occur after PCB manufacturing, but they may also occur during this period. The environment of the room in which the assembly takes place will affect the PCB. For example, humidity can affect how components and solders behave during assembly, so environmental conditions need to be controlled. Another common failure is the inability to keep PCB clean during and after manufacturing. Dust, hair, and even insects may enter the PCB. Therefore, preventive measures need to be taken.
Solve PCB design and assembly failure
After thorough inspection and analysis, most fault problems can be solved through rework. However, the best way to reduce PCB failure risk is to cooperate with an experienced PCB assembly company. Our team is very happy to provide you with product answers and solutions.
By understanding the common faults in PCBs, you can be sure that you have avoided these problems and taken the correct precautions to prevent them from happening. Keep in mind that you should always check for traces of leaked chemicals; Clean PCB after welding; Do not let the component barrier break; Use pure materials without defects; Avoid subjecting PCB to excessive thermal stress, and keep PCB room and hands clean. The PCB processing factory explained the analysis of 10 possible reasons for failure of PCB design and assembly, as well as the reasons for failure of components and welding.