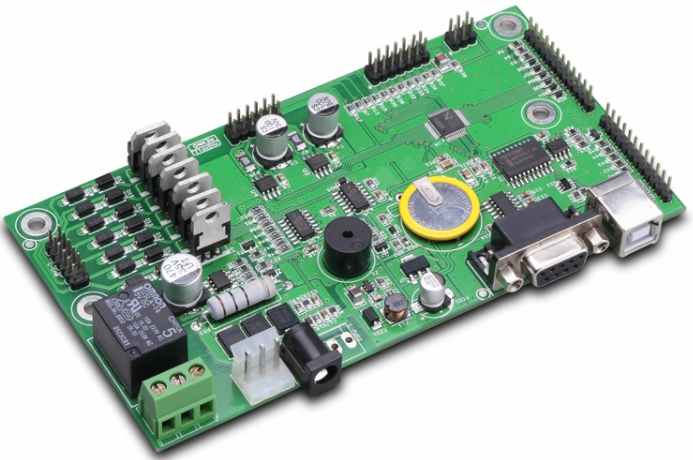
Connected board usually combines more than two pieces of the same circuit board into a large circuit board, such as 2 in 1 (2-in-1), 3 in 1 (3-in-1), 4 in 1 (4-in-1), etc. There was also a case where boards of different shapes were made into a large board, but this was rare because it was difficult for the Planner to arrange production with just the right number of different boards. The following patch processing manufacturer Xiaobian to explain how to decide the number of PCB board and circuit board design how to enhance ESD function of the relevant knowledge.
1. How to enhance ESD function in circuit board design
In the design of PCB board, PCB anti-ESD design can be realized by layering, proper layout and wiring and installation. In the process of circuit board design, most design modifications can be limited to adding or subtracting components through prediction. The PCB layout and wiring can be adjusted to prevent ESD.
Static electricity from the human body, the environment and even inside electronic equipment can cause various damage to the precision semiconductor chip, such as penetrating the thin insulation layer inside the component; Destroy the grids of MOSFET and CMOS components; Trigger locking in CMOS devices; PN junction with short circuit reverse bias; PN junction with short circuit forward bias; Melt the welded wire or aluminum wire inside the active device. In order to eliminate electrostatic discharge (ESD) interference and damage to electronic equipment, it is necessary to take a variety of technical measures to prevent.
In the design of PCB board, PCB anti-ESD design can be realized by layering, proper layout and wiring and installation. In the process of circuit board design, most design modifications can be limited to adding or subtracting components through prediction. The PCB layout and wiring can be adjusted to prevent ESD.
2. How to determine the number of PCB connecting boards
Generally speaking, after the design engineer has determined the Printed Circuit Board's appearance, the panelization of the circuit board should proceed immediately. The purpose of connecting plates is nothing more than the following: 1. Increase the output of the production line. 2, reduce the loss of plate. The most common connected board usually combines more than two pieces of the same circuit board into a large circuit board, such as 2 in 1 (two-in-one), 3 in 1 (three-in-one), 4 in 1 (four-in-one), etc. There was also a case where boards of different shapes were made into a large board, but this was rare because it was difficult for the Planner to arrange production with just the right number of different boards.
More related reading: The advantages of PCB "Yin-yang board" are also examples of making the same board into "Yin-yang board". "Yin-yang board" mostly means top and bottom surface configuration, which is usually used on circuit boards with fewer parts, such as mobile phone board, because it can make full use of SMT's long line hitting function to increase efficiency. But the disadvantage is that the use of some restrictions, and may cause parts uneven heat phenomenon, such as some circuit boards will put the heavy parts concentrated design of a side, and then this side will be as a second hit to avoid heavy parts repeated reflow fall, of course, this board is more difficult to use the design of the Yin and Yang board. Some boards may have more heat-absorbing parts (such as a large area of ATM card slot), and are not suitable for the design of [Yin and Yang board]. Of course, there are also flexible [Yin and Yang plate] typing method can overcome this problem, but not to discuss. Basically, in the design of how much even board, should consider the following factors, in fact, no matter how to produce or design, ultimately can not be separated from the consideration of money, so should all the factors into the amount to make the final measurement standard to choose a suitable plate method. Consider the best utilization rate of circuit board general circuit board manufacturers in order to rapid mass production and low cost, will have its basic standard plate size, such as 16.16"x16.16", 18.32"x18.32", 20.32"x20.32",... Etc., what we have to do is to try to use up all these plates, that is to say, to choose a suitable size of the standard plate to put our board into, to achieve the highest utilization rate of the plate. Because the price of the circuit board will be with the size of the board to price money, the same board can be stuffed more circuit board, the cheaper the price of the circuit board. Of course, the price of the circuit board also has to consider several layers of board, drill several holes, there is no HDI... Etc.
Considering SMT printing/pasting efficiency SMT line usually has the so-called long line and short line, short line is the line is shorter, mostly only a fast machine and a slow machine, at most is to add a fast machine; Long line is a long line, fast and slow machine more than a few pendulum. Generally speaking, it takes about 35 ~ 40 seconds to print a solder paste for a 150mm composite plate. If only a 2 in 1 composite plate is used for SMT short lines, the time allocated to each machine may be about 10 ~ 26 seconds. Obviously, all the time is lower than the solder paste printing time, that is to say, the SMT machine behind is waiting for the solder paste printing machine, which leads to the idle SMT machine and reduces the production capacity.
If you change the 2 in 1 connecting plate to 4 in 1, Then the efficiency is immediately improved (output per hour)2 in 1 board solder paste printing (seconds) Fast machine one (seconds) fast machine two (seconds) slow machine (seconds) Bottleneck time (seconds) hourly output Top3826261038188 Bottom4034352440180 pieces 4 in 1 board solder paste printing (s) Fast machine one (s) Fast machine two (s) Slow machine (s) Bottleneck time (s) per hour output Top3852522052276 Bottom4068704870204 pieces 1. Output per hour: {[60(seconds/min) x 60(minutes/hour)] / Bottleneck time (seconds)} x number of shutters. In addition, circuit board manufacturers would prefer the number of connected boards to be as small as possible to avoid so-called cross board (X-board) losses. The so-called cross board means that there is more than one defective board in the composite board. General SMT printing factories do not want to accept this kind of board, because it will cause loss of efficiency. However, this kind of circuit board cannot be absolutely avoided in the manufacturing process, so the more the number of consecutive boards, the more the number of discarded circuit board factory, and the relative cost will increase. As stated at the beginning, the final result is still to be converted into money to calculate the optimal number of boards using and connecting plates. Moreover, the results of different plate factories and SMT factories may be different.