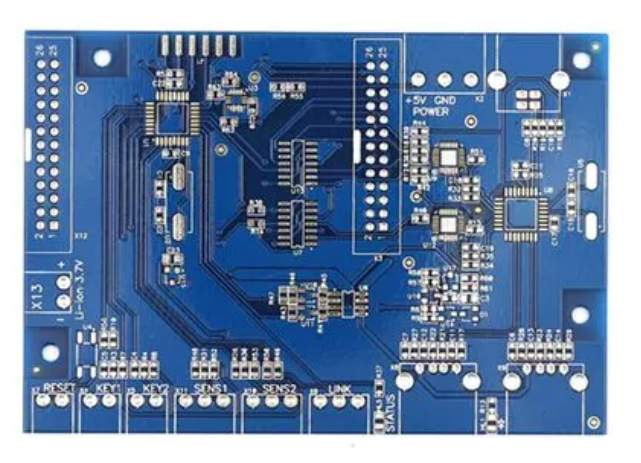
Rigid and flexible board design in the traditional sense of PCB design is much more complex, and need to pay attention to the place is particularly many. In particular, the rigid torsion transition area, as well as the related design aspects such as wiring and hole, need to follow the requirements of the corresponding design rules.
1. Through the hole position
In the case of dynamic use, especially when the soft plate is often bent, the holes on the soft plate should be avoided as far as possible. These holes are easy to be damaged and broken. However, the strengthening area on the soft plate can still punch holes, but also to avoid the strengthening area near the edge. Therefore, in the combination of soft and hard plate design when punching to avoid a certain distance in the combined area. For the distance between the hole and the soft and hard binding zone, the design rules should be followed as follows:
The storage distance should be at least 50mil and at least 70mil in high reliability applications.
Most manufacturers will not accept less than 30mil.
Follow the same rules for holes on soft plates.
This is one of the most important design rules of the soft and hard combined board must be followed.
2. Design of pad and hole
Under the condition of meeting the electrical requirements, the welding pad and the hole shall gain the maximum value. The connection between the welding pad and the conductor shall adopt a smooth transition line to avoid right angles. Separate pads should be toe-toed to strengthen support.
In the design of rigid and soft board, the hole or pad is easily damaged. Rules to follow to reduce this risk:
Welding pad or through the hole of the welding layer exposed copper ring, the larger the better.
Through the hole line as far as possible to add tears, increase the mechanical support.
Add disk toe for reinforcement.
3. Cable design
If there are different layers of wiring in the Flex zone, try to avoid the same path of one wire on the top layer and another wire on the bottom layer. In this way, when the soft plate bending, the upper and lower two layers of wire copper stress is inconsistent, easy to cause mechanical damage to the line. Instead, it should be spread out and cross paths.
In the Flex zone (Flex) routing design requires the best arc line, rather than Angle line. Contrary to the recommendations of Rigid zones. This can protect the flexible plate part of the line is not easy to break when bending. Lines should also avoid sudden expansion or contraction, and use teardrop arc connections between thick and thin lines.
4. Copper design
To enhance the flexible bending of the flexible plate, copper or flat layer is best to use the mesh structure. But for impedance control or other applications, the electrical quality of the mesh structure is not satisfactory, so the designer in the specific design needs to choose its light judgment, is to use the mesh copper or solid copper. But for the waste area, or design as much solid copper as possible.
5. Distance between the drill hole and the copper peel
This distance refers to the distance between a hole and copper, we call it "hole copper distance". Soft plate material is different from hard plate material, so that too tight hole copper distance is difficult to deal with. Generally speaking, the standard hole copper spacing should be 10mil.
For the rigid and flexible binding zone, the two most important distances must not be ignored. One is the Drill to Copper, as described here, which follows a minimum standard of 10mil. The other is the distance from the Hole to the edge of the soft plate (Hole to Flex), generally recommended 50mil.
6. Design of rigid and flexible combination area
In the rigid and flexible binding area, the soft plate is best designed to connect with the hard plate in the middle of the stack. And the soft plate through the hole in the rigid and flexible joint area is considered to be buried holes. The rigid and flexible binding area needs attention as follows:
Line to smooth transition, the direction of the line should be perpendicular to the bending direction.
The wire should be evenly distributed throughout the bending area.
The width of the wire should be maximized throughout the bending zone.
PTH design should not be adopted as far as possible in rigid torsion transition zone.
7. Bending radius of bending zone of rigid and flexible binding plate
The flexible flexural zone of rigid and flexible bonded board shall be able to withstand 100,000 flexures without circuit breaks, short circuits, performance degradation or unacceptable delamination. The flexural resistance shall be determined by special equipment, or by equivalent instruments. The tested samples shall meet the requirements of relevant technical specifications. In design, the design of bending radius should be related to the thickness of the flexible bending area and the number of layers of the flexible plate. A simple reference standard is R=WxT. T is the total thickness of the soft plate. Single panel W is 6, double panel 12, multilayer 24. Therefore, the minimum bending radius of single panel is 6 times plate thickness, double panel is 12 times plate thickness, and multilayer board is 24 times plate thickness. All should not be smaller than 1.6mm.
In short, for the combination of soft and hard board design, particularly important is the flexible circuit board design. Flexible circuit board design requirements to consider the flexible circuit board of the substrate, bonding layer, copper foil, covering layer and reinforcement plate and surface treatment of different materials, thickness and different combinations, as well as its performance, such as peeling strength, anti-deflection performance, chemical properties, working temperature, etc. Special consideration should be given to the assembly and specific application of the flexible plate designed. The specific design rules in this respect can refer to IPC standards: IPc-D-249 and IPC-2233.