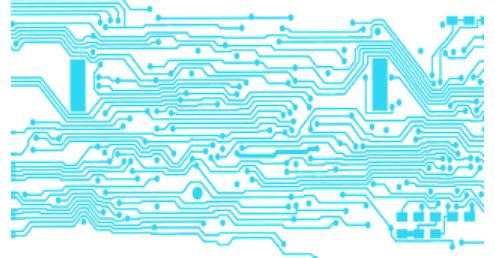
In circuit board maintenance, it is often necessary to weld and disassemble components. Instrument workers must master the welding and disassembling skills of circuit board and electronic components of instruments so as to improve the maintenance quality of instruments.
1. Skills of welding electronic components
(1) The choice of flux is very important: rosin flux can be used for instrument maintenance and welding. When welding rosin and solder should be added to the solder joint, do not use hot iron head to dip rosin; Using rosin alcohol solution is more convenient.
② Pay attention to the cleaning of the components' pins: the metal pins of electronic components are often oxide, oxide conductivity is poor, and it is difficult to tin. Before welding, the metal surface of the welding should be polished with an eraser. In order to make the pins of electronic components easy to weld, the components are manufactured with surface treatment. For heavily oxidized components, use a knife or sandpaper to remove the oxide layer from the component pins. After removing the oxide layer, tin is plated on the clean component lead so that the lead is evenly coated with a very thin tin layer. Only after careful cleaning and tinning of the electronic components of the pins, after welding will not appear "virtual welding" problem.
③ Welding operation points: low melting point of rosin solder wire should be selected for welding components. When welding, tweezers should be used to clamp the pin of the component, one is to fix the component is not moving, the other is to protect the component by heat dissipation. When welding, the temperature of the iron head should be appropriate, and the contact time of the welded element and the iron should be appropriate. Too short welding time will cause virtual welding, but too long welding time will burn the element. Generally, the welding time of components should be 2-3s. Do not shake the element or lead before the solder is solidified in the solder joint, otherwise it will cause virtual welding. Do not move the iron head in the process of welding components, otherwise it will affect the quality of the solder joint. The welding of special devices should be carried out according to the component requirements, such as CMOS devices require that the electric iron metal shell is not charged and should be connected to the ground. If possible, it is best to use anti-static welding platform. If there is no condition, the electric iron can be heated first. When welding, the electric iron can be removed from the power socket and the waste heat can be used for welding. After welding, clean the residual flux on the circuit board with anhydrous alcohol.
Electric iron welding experience: the temperature of the iron head should be appropriate, generally to rosin melting, but do not leave smoke for the degree. The amount of solder should be appropriate to just wrap and cover the foot of the intended welding element. For welding with high component density, the components that impede welding can be temporarily removed, and then restored to the original position after welding. After the completion of welding, it is necessary to eliminate solder slag and other sundries in time to avoid short circuit fault that may be caused. It is recommended to clean solder joints and their surroundings with anhydrous alcohol.
2, the skills of disassembling components on the circuit board: usually disassembling components with tweezers to clamp the pin root, when the solder joint is melted, the pin will be quickly pulled out of the solder joint, tweezers have the function of clamping and cooling, pulling out can be with the soldering iron head soldering tin and other actions. In order to disassemble easily, the solder joint can be added to promote the melting of tin. The electric iron used to remove the components can be selected to be 5-10W larger than welding, the power of the iron is large, the heat is large, the time of melting tin is short, if the power of the iron is small, the time of melting tin is long but easy to burn the components.
How to improve the craft of circuit board maintenance
Now more and more circuit boards using surface mount components, compared with traditional packaging, it can reduce the area of the circuit board, easy to mass processing, high wiring density. The lead inductance of patch resistors and capacitors is greatly reduced, which has great advantages in high frequency circuits. The disadvantage of surface mounted components is that they are not easily welded by hand.
1. Tools and materials required for circuit board maintenance
The welding tool needs a 25W small copper head soldering iron. If possible, the welding table with temperature adjustable and ESD protection can be used. Note that the tip of the soldering iron should be thin and the width of the top should not be greater than 1mm. A pair of pointed tweezers can be used to move and secure chips and to inspect circuits. Also prepare fine wire and flux, isopropyl alcohol, etc. The main purpose of using flux is to increase the fluidity of the solder, so that the solder can be drawn with the soldering iron and coated smoothly on the pins and pads by the action of surface tension. Remove the flux from the plate with alcohol after welding.
Two, circuit board maintenance and welding methods
1. Before welding, the welding pad is coated with flux and treated with a soldering iron, so as to avoid poor tinning or oxidation of the pad, resulting in poor welding, and the chip is generally not needed to be treated.
2. Carefully place the PQFP chip onto the PCB board using tweezers, taking care not to damage the pins. Align it with the pad, ensuring that the chip is placed in the correct direction. Adjust the temperature of the soldering iron to more than 300 degrees Celsius, dip the tip of the soldering iron head with a small amount of solder, press down on the aligned position of the chip with the tool, add a small amount of flux on the two diagonal position of the pins, still press down on the chip, weld the two diagonal position of the pins, so that the chip is fixed and cannot move. Recheck chip alignment after welding diagonally. If necessary, it can be adjusted or removed and re-aligned on the PCB board.
3. To begin soldering all pins, solder the tips of the iron and apply flux to all pins to keep them moist. Touch the tip of the iron to the end of each pin of the chip until you see solder flowing into the pin. During welding, the tip of the iron should be kept parallel with the pin to be welded to prevent lap bonding due to excessive soldering.
4. After soldering all pins, wet all pins with flux to clean the solder. Blot off excess solder where needed to eliminate any short circuits and lapping. Finally, check with tweezers to see if there is any solder. After the check is complete, remove the flux from the circuit board. Dip the hard bristle brush with alcohol and wipe it carefully along the direction of the pins until the flux disappears.
5. The patch resistance component is relatively easy to weld some, you can first spot on a solder spot on the tin, and then put on the end of the component, with tweezers to hold the component, welding on the end, and then see whether it is put; If it is in place, weld the other end. It takes a lot of practice to really master welding skills. Now more and more circuit boards using surface mount components, compared with traditional packaging, it can reduce the area of the circuit board, easy to mass processing, high wiring density. The lead inductance of patch resistors and capacitors is greatly reduced, which has great advantages in high frequency circuits. The disadvantage of surface mounted components is that they are not easily welded by hand. Therefore, this paper takes common PQFP encapsulated chip as an example to introduce the method of circuit board maintenance. Expert answer circuit board maintenance:
Circuit board repair basic formula
A common circuit board, circuit combination tens of millions
The appearance of components changes frequently, and character recognition is the key
Resistive capacitors are the most common, and damage is common
Resistance value is easy to change, capacitance leakage capacity leakage
Inductance transformer is coil, simple test to see through
Diode and audion, measure the PN junction positive and negative
MOS tube and thyristor, trigger test is key
These are discrete parts, integrated circuits for many years
Simulator parts have operational amplifier, virtual short virtual end to judge
Optocoupler isolation before and after the level, the damage is thousands of millions
Digital devices are often seen, 40 and 74 front
Then there's the analog-to-digital converter, which is a lot of testing
Don't forget ROM and CPLD, burn write to rely on the programmer
CPU, single chip microcomputer, timing judgment logic instrument
All kinds of sensors. Damage rate is number one