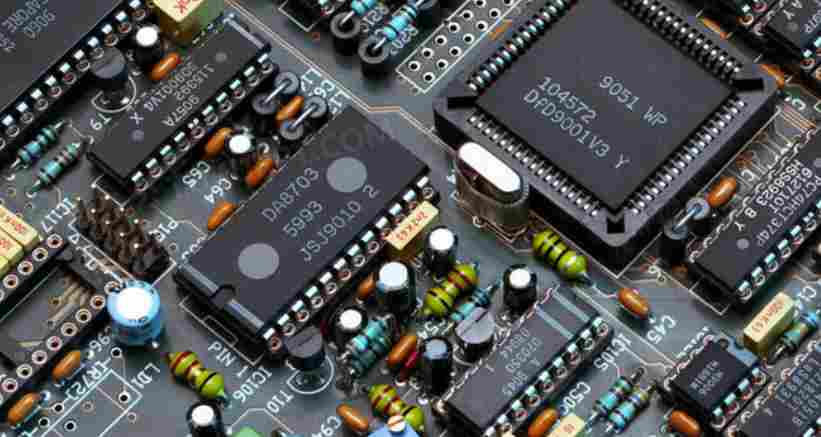
Electrical testing is a very important link in the PCB board manufacturing process, the purpose is to check whether the PCB board is open and short circuit problem, to ensure that the finished products in line with the customer's electrical performance requirements. Circuit board manufacturers have a variety of electrical testing methods, deep link circuit is usually used by flying needle test, test rack test. Let's take a quick look at the two test methods.
Flying needle test is one of the methods to check the electrical function of PCB (on/off test). Flying needle tests use four to eight independently controlled probes that move into the element under test. The unit under test (UUT, unit under test) is transferred to the test machine by belt or other UUT conveyer system. Then fixed, the probe of the tester contacts the test pad (test pad) and the access hole (via) to test the individual components in the test unit (UUT). The test probe tests the components in multiplexing over the UUT by connecting the multiplexing system to drivers (signal generators, power supplies, etc.) and sensors (digital multimeters, frequency counters, etc.). While one component is being tested, the other components on the UUT are electrically shielded by probes to prevent interference with readings. Flying needle testing of general samples and small batch PCB boards can reduce the cost of making test racks, thus reducing the time of making test racks and shortening the delivery cycle.
Traditional online testing is another batch PCB board testing method. Test data need to be prepared in advance and sent to test rack suppliers to make test racks. Each product model has corresponding test racks, and then the test racks are fixed on the test machine to start on-off testing. This test method is fast and generally used for batch PCB board test.
How to save cost and maintain quality of the circuit board
In recent years, with the increase of labor cost and raw material price again and again, many customers began to require product price reduction to save costs. Circuit board manufacturers just located in the middle of the whole food chain, we do circuit board, the next to face plate suppliers and other auxiliary material suppliers of the price, to face the customer requirements of the price reduction, but also in the face of the growth of labor costs, we all racking their brains to think of how to save costs and to ensure quality. Keyou Circuit is specialized in the production of high-precision multi-layer PCB circuit boards (single panel, double panel, multi-layer board),LED aluminum substrate, copper substrate,3K full/half carbon fiber board, etc. It is a high-tech enterprise with quality assurance, timely delivery and sales as one. It is a manufacturer worthy of reliance.
Batch delivery of the circuit board is based on the basis of proofing, only after the sample qualified, the product can be mass-produced. If the size of the product is large, the one-time production can be satisfied. However, if the size of the product is small, the one-time material will produce inventory after delivery. If the customer samples are directly mass produced through OK, less material can be added during mass production. Can empty the inventory, but if the customer sample test is unqualified, need to revise, then the inventory can only be scrapped.
In order to solve this problem, we can choose the same material, the same plate thickness and the same process of the product, and make it together, which has achieved the effect of reducing inventory and saving cost.
When the appearance of customers' products is irregular, we can not according to the ordinary style of the plate, according to its different shapes, design inverted, concentric circles or two large boards with small boards in the middle of the way to improve the utilization rate of the board, save costs.
Common problems and improvement methods for PCB manufacturing?
Preface: What is PCB,PCB is the English abbreviation of circuit board, what is PCB is the English abbreviation of rigid circuit board, the following is the circuit board at present Keyou circuit board manufacturers produced by the common bad problems, problem cause analysis and solution. Here to share with everyone, in this hope to help you, can let your skills get improved! 1. Problem: Copper foil edge warps in PCB Reasons:
(1) improper feed rate;
(2) The milling cutter is not sharp enough.
Solution:
(1) Grinding or replacement of milling cutter;
(2) Optimize the relationship between feed rate and speed.
2. Problem: The feed pressure required in PCB is too large
Reasons:
(1) Bearing damage;
(2) The pressure value of the lower pressure wheel is set too high.
Solution:
(1) Replace the bearing;
(2) Adjust to the specified pressure according to the technological requirements.
3. Problem: The hypotenuse in PCB is rough, sometimes forming bell cut
Reasons:
(1) the cutting knife is not sharp enough;
(2) The cutter is loose or the cutter holder is not clamped.
Solution:
(1) Replace the sharp cutting knife;
(2) Re-clamp and fix after inspection.
4. Problem: PCB hypotenuse surface undulates
Reasons:
(1) The cutter seat is loose
(2) uneven plate thickness
(3) Belt wear or damage
(4) The guide rails deviate from the set value
(5) Guide wheel or bearing wear
(6) lower pressure wheel wear or deviation from the set value
Solution:
(1) Replace the new belt;
(2) Replace pulley or bearing;
(3) readjust the guide rail according to the technological requirements;
(4) Re-implement fixed measures after inspection;
(5) Adjust the tension, replace the flywheel or replace the bearing;
(6) Check the specifications of the plate and choose the machine type that can match the product.