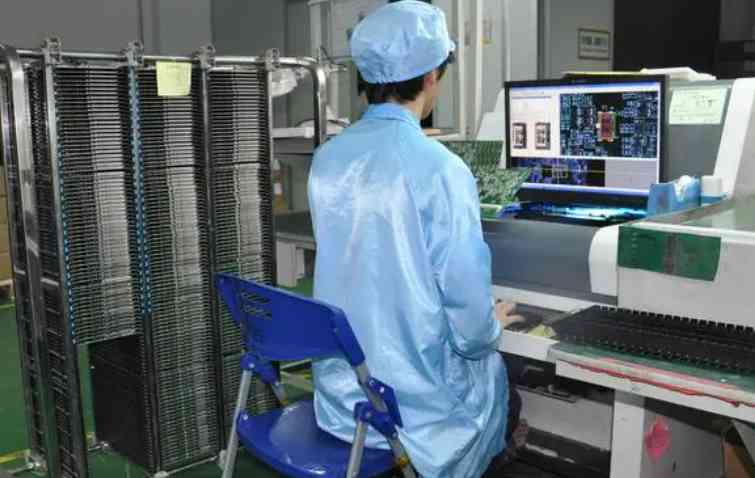
1, the board up and down uneven heat, back in first out, prone to bending plate warped defects;
2. When entering the tin furnace, the liquid tin on the solder plate will be arc shaped by the surface tension of the liquid, resulting in uneven tin thickness on the solder plate. Due to the hot air scraping force and gravity, the lower edge of the solder plate will come into solder sag, so that the welding of SMT surface mounted parts is not easy to stick steadily. It is easy to cause deviation or tomb stoning of welded parts.
3. The smaller the pad is, the more obvious the tin arc shape is on the surface of the pad, and the worse the flatness is.
Solution:
For the BGA packaging plate less than 14MIL pad or the plate with high flatness requirements, considering the hidden dangers of tin spraying, it is not recommended to make tin spraying plate, can be changed to gold, gold plating, if the customer must make tin plate, it must be clear that the customer's requirements for flatness.
What are the technical requirements of PCB production? Circuit board manufacturer
When receiving orders, processing engineering data and production process, we often find that some customers' designs do not meet the feasibility requirements of PCB production process. Of course, this is not to say that designers have limited skills, but because most design engineers have not been to PCB factories to understand how a qualified PCB board is produced, and have little knowledge of PCB production, which is the main reason that the designed board cannot be processed and produced or there are problems in the production process. Therefore, I hope the following contents can help engineers engaged in PCB design.
Details of relevant design parameters:
1. Minimum line width: 6mil (0.153mm). That is to say, if the line width is less than 6mil, it will not be able to produce, (the minimum line width of the inner layer of multilayer board is 8MIL) if the design conditions permit, the bigger the design, the better the line width, the better the factory production, the higher the yield, the general design routine is about 10mil, this point is very important, the design must be considered.
2. Minimum line distance: 6mil (0.153mm).. Minimum line distance, that is, line to line, line to pad distance is not less than 6mil from the production point of view, the bigger the better, generally in 10mil, of course, under the condition of design conditions, the bigger the better this point is very important, the design must be considered.
3. Distance between line and contour line 0.508mm(20mil)
Two, via hole (is commonly known as conductive hole)
1. Minimum aperture :0.3mm(12mil)
2. The minimum hole (VIA) aperture is not less than 0.3mm(12mil), the single side of the pad can not be less than 6mil(0.153mm), the best greater than 8mil(0.2mm) is not limited, this point is very important, the design must be considered.
3. Through hole (VIA) hole to hole spacing (hole edge to hole edge) should not be less than 6mil, preferably greater than 8mil. This is very important and must be considered in the design.
4. Spacing between pad and contour line 0.508mm(20mil)
Three, PAD pad pad (commonly known as the plug-in hole (PTH))
1. The size of the plug-in hole depends on your component, but it must be larger than your component pin. It is recommended that the pin of the component should be larger than 0.2mm at least, that is to say, 0.6.
2 plug-in hole (PTH) welding disc outer ring side can not be less than 0.2mm(8mil) of course, the bigger the better, this point is very important, the design must be considered
3. Plug-in hole (PTH) hole to hole spacing (hole edge to hole edge) can not be less than: 0.3mm of course, the bigger the better, this point is very important, the design must be considered
4. Spacing between pad and contour line 0.508mm(20mil)
Four, anti welding
Plug-in window opening, SMD window opening side shall not be less than 0.1mm(4mil)
Five, character (character design, directly affect the production, whether the character is clear to the character design is very relevant)
Character word width should not be less than 0.153mm(6mil), word height should not be less than 0.811mm(32mil), the ratio of width to height is the best 5 relationship, that is to say, word width 0.2mm word height is 1mm, so as to push the class.
Six: non-metallic slot hole hole minimum spacing is not less than 1.6mm, otherwise it will greatly increase the difficulty of milling edge
Seven: patchwork
1. Patchwork is divided into no gap patchwork and gap patchwork, gap patchwork gap should not be less than 1.6 (plate thickness 1.6) mm otherwise it will greatly increase the difficulty of milling edge patchwork plate size depending on the equipment is different, no gap patchwork gap about 0.5mm process edge is generally 5mm
2. The size in the direction of the Mosaic V-cut must be larger than 8cm, because the V-cut less than 8cm will fall into the machine, the width of the V-cut must be less than 32cm, larger than this width will not be put into the V-cut machine, this point due to production process limitations, but we cannot do.
3.V cut can only walk in a straight line, because of the appearance of the board, it can not walk in a straight line can be added spacing for stamp hole bridge connection, related matters needing attention