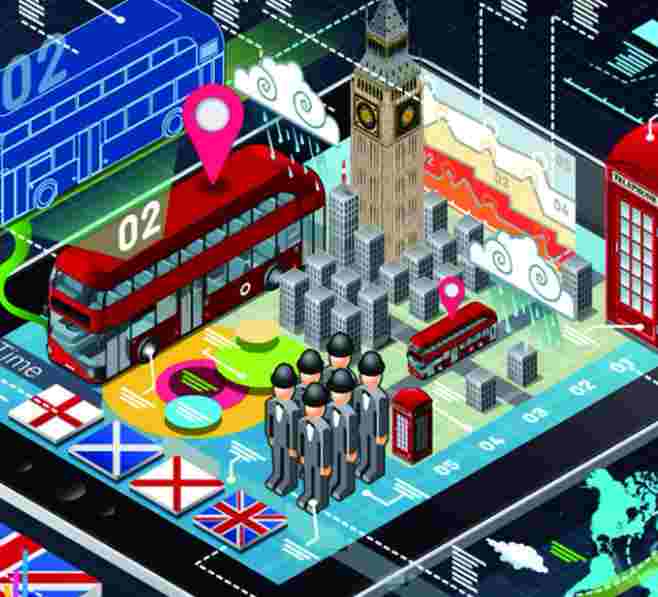
Scanning acoustic microscope Currently used for electronic packaging or assembly analysis is mainly C-mode ultrasonic scanning acoustic microscope, which uses the amplitude and phase and polarity changes generated by the reflection of high-frequency ultrasonic waves on the discontinuous interface of materials to image. The scanning mode is to scan the X-Y plane information along the Z-axis.
Therefore, the scanning acoustic microscope can be used to detect components, materials and PCB and PCBA internal defects, including cracks, delamination, inclusions and voids. If the frequency width of the scan acoustics is sufficient, the internal defects of the solder joint can also be detected directly.
A typical scanning acoustic image is a red warning color to indicate the existence of defects. As a large number of plastic packaged components are used in SMT process, in the process of converting from lead to lead-free process, a large number of moisture reflux sensitive problems will occur, that is, hygmoscopic plastic sealing devices will appear internal or substrate delamination cracking during reflux at a higher lead-free process temperature. In the high temperature of lead-free process, common PCB will often appear the phenomenon of board explosion.
At this point, scanning acoustic microscope shows its special advantage in nondestructive detection of multilayer high density PCB. And the general obvious explosion plate is only through the visual appearance can be detected.
Microscopic infrared analysis is a combination of infrared spectrum and microscope analysis method, it uses the principle of different materials (mainly organic matter) absorption of infrared spectrum, analysis of material compounds, combined with the microscope can make visible light and infrared light in the same optical path, as long as in the visible field of view, you can find to analyze trace organic pollutants.
Without the combination of a microscope, usually infrared spectroscopy can only analyze a large sample size. In many cases of electronic technology, trace pollution can lead to poor weldability of PCB pad or lead pin. It can be imagined that it is difficult to solve process problems without the infrared spectrum of the microscope. The main purpose of micro-infrared analysis is to analyze the organic pollutants on the surface of the welded surface or solder joint, and to analyze the causes of corrosion or poor weldability.
Scanning electron microscopy (SEM) is one of the most useful large-scale electron microscopy imaging systems for failure analysis. It is most commonly used for morphological observation. Currently, the function of scanning electron microscopy has been very powerful, and any fine structure or surface characteristics can be magnified to hundreds of thousands of times for observation and analysis.
In the failure analysis of PCB or solder joint, SEM is mainly used to analyze the failure mechanism. Specifically, it is used to observe the morphology and structure of the surface of the solder joint, the microstructure of the solder joint, the measurement of intermetallic compounds, the analysis of weldability coating and the measurement of tin whisk.
Different from the optical microscope, the image produced by scanning electron microscope is electronic, so only black and white, and the sample of scanning electron microscope is required to conduct electricity, for non-conductors and part of the semiconductor need to spray gold or carbon treatment, otherwise the charge gathered on the surface of the sample will affect the observation of the sample. In addition, the depth of field of SEM image is much larger than that of optical microscope, which is an important method for the analysis of metallographic structure, micro-fracture, tin whisker and other uneven samples.
Differential scanning calorimeter (DSC)
Differential Scanning Calorim-etry is a method to measure the relationship between power difference and temperature (or time) between input material and reference material under programmed temperature control. It is an analytical method to study the relationship between heat and temperature, according to which the physical, chemical and thermodynamic properties of materials can be studied and analyzed.
DSC is widely used, but in the analysis of PCB is mainly used to measure the degree of curing of various polymer materials used on PCB, glass state conversion temperature, these two parameters determine the reliability of PCB in the subsequent process.
Thermal Mechanical Analysis (TMA) is used to measure the deformation behavior of solids, liquids and gels under thermal or mechanical forces under programmed temperature. It is a method to study the relationship between thermal and mechanical properties. According to the relationship between deformation and temperature (or time), the physicochemical and thermodynamic properties of materials can be studied and analyzed.
TMA is widely used in the analysis of PCB. It is mainly used in the measurement of the two most critical parameters of PCB: linear expansion coefficient and glass transition temperature. The PCB of substrate with excessive expansion coefficient often leads to the fracture failure of metallization hole after welding and assembly.
Thermogravimetry Analysis (TGA) is a way to measure the mass of a substance as it changes with temperature (or time) under programmed temperature control. TGA uses a sophisticated electronic balance to monitor the subtle mass changes that occur during the process of programmed temperature change.
According to the change of material mass with temperature (or time), the physicochemical and thermodynamic properties of materials can be studied and analyzed. In the aspect of PCB analysis, it is mainly used to measure the thermal stability or thermal decomposition temperature of PCB materials. If the thermal decomposition temperature of the substrate is too low, PCB will explode or delamination failure phenomenon when it passes the high temperature of welding process.