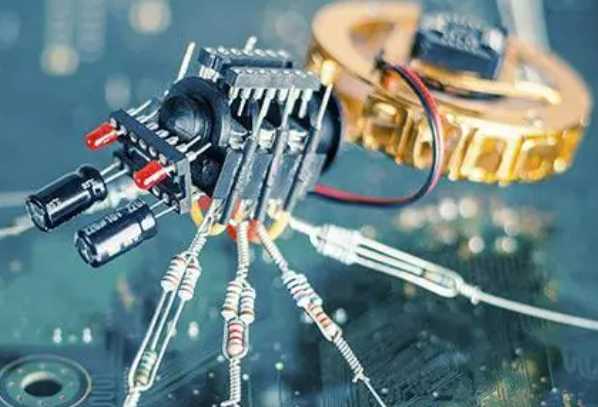
In AD6.3 and later, you can create grooved and non-circular pads and add grooves and square pad holes.
The detailed drill type can be seen from the production manufacturing step, place special string symbols on your PCB board, and add output instructions on top, place legend string symbols in the DrillDrawing layer.
Note: If the latest software version supports output machining file detection, it is a good idea to check your PCB machining file to see if grooves already exist on your board. In addition, the earliest versions often used methods including describing grooves in mechanical or solder resistance layers, using text descriptions. Some designers place pads or through-holes that overlap the through-holes to define the area of drill output, but this can cause the bit to be damaged.
When the irregular hole fabrication method is different from the next plate structure, you will find that your plate structure is more suitable to be handled. So there are three ways to define a trench
Add detailed machining information to the mechanical layer
Add multiple overlapping pads or through holes
Apply the CAMtasticNCDrill feature
For examples of this design, the mechanical layer is often used to describe the groove information
Details can be found in the mechanical layer PlatedRouteDetails, where you can see the connection between the wires and the grooves in J1, J6, and J2S. To switch to single layer mode, you can see the initial Settings for each layer (shortcut to switch to single layer mode: shift,s).
The wiring details are contained in the component so that the component is moved when switching.
Before using this route, check with the PCB processor to see if it is acceptable to set up the dog method.
For this step, the pad and groove area must have been established with sufficient support information to the processor as follows:
Multilayer pads with holes are set to 0 units, which is the default setting for the pad area
The starting and ending pad positions are at the end of the groove positions and the aperture sizes for these pads are to be set to the same size as the groove.
Line is placed on the mechanical layer of the coating channel details from the starting center point to the end of the pad, with the width of the line referring to the width of the groove cutting scissors.
You also need to think hard about the inner plane connections for the grooved pads, leaving enough space for solid connections on the inner plane, whereas hot pads and empty pads need to be set up manually. In this PCB example, a hot pad has been used -- manually creating arcs and lines, see Pad 1 of J6 for details.
The connection rules for the power plane connection set for the pad can be connected directly. For design rules, look at the power plane connection type setting rules to set connections directly to these grooves, (Rule: PlaneConnect_Obround_Pads, add an already-set class to the pads in the design; Classes can be easier to set in rules.) When fitting to the plate, if you cannot easily attach to the hot pad you can choose the simple option to attach directly to these grooved pads.
Finally, the grooved pad cannot be connected to the plane. For example, pad 2 and pad 3 on J6 need to apply copper to the clipped empty area, so add a line or other object to connect the inner electric layer as the flying line of the shear area. Because the plane is negative output.
When you export your Gerber file or ODB++ file, carefully check the internal layer connections, remember to include the Platedroutingdetails of the mechanical layer, and remind your board manufacturer to look out for the grooved pad on the PCB board.
How to set wire width reasonably in PCB design
The width of printed wire in PCB design should follow the following rules:
1, wire width should be able to meet the requirements of electrical performance and convenient production is appropriate, its minimum value to withstand the size of the current, but the minimum should not be less than 0.2mm, in high density, high precision printed lines, wire width and spacing generally desirable 0.3mm.
2, wire width in the case of large current should also consider its temperature rise, single panel experiment shows that when copper foil thickness is 50μm, wire width 1-1.5mm, through the current 2A, temperature rise is very small, therefore, generally choose 1-1.5mm width wire may meet the PCB design requirements without causing temperature rise.
3, printed wire public ground wire should be as thick as possible, if possible, the use of lines greater than 2-3mm, this is particularly important in the circuit with a microprocessor, because when the line is too thin, due to the change of the current through the ground potential changes, the level of the microprocessor timing signal is unstable, will make the noise tolerance deterioration.
4. The principles of 10-10 and 12-12 can be applied in wiring between DIP-packaged IC feet, that is, when two wires pass between two feet, the diameter of the pad can be set as 50mil, and the line width and line distance are both 10mil; when only one wire passes between two feet, the diameter of the pad can be set as 64mil, and the line width and line distance are both 12mil.