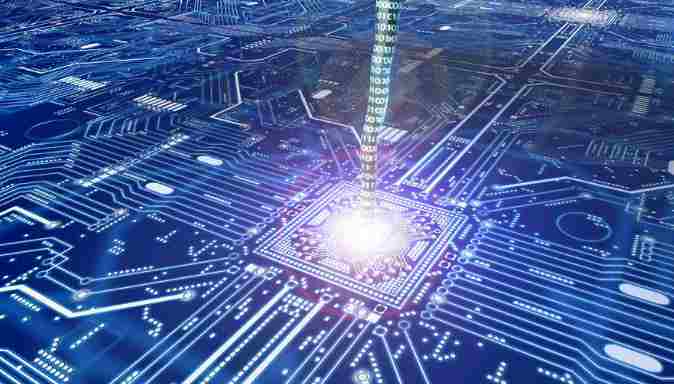
1. Coating site and defects
a) The PCB surface except welding pad, MARK point and test point shall be coated with solder resistance layer.
b) If the customer uses FILL or TRACK to indicate the disk, he/she must draw a Solder mask of the corresponding size to indicate the solder on it. (We strongly recommend that the non-pad form is not used to represent the disk before design)
c) If you need to dissipate heat on the large copper skin or spray tin on the line, you must use Solder mask to draw a figure of the corresponding size to indicate the tin on the copper skin.
2. Adhesion
The adhesion of the solder resistance layer is in accordance with Class 2 requirements of IPC-A-600F.
Character and etch marks
1. Basic requirements
a) PCB characters should generally be designed with a character height of 30mil, a character width of 5mil and a character spacing of 4mil, so as not to affect the discriminability of the text.
b) Etched (metal) characters should not be bridged with wires and adequate electrical clearance should be ensured. General design according to the word height 30mil, word width 7mil above the design.
c) If the customer does not have clear requirements for characters, our company will generally adjust the collocation ratio of characters according to our technological requirements.
d) If there is no clear stipulation by the customer, our company will print our trademark, material number and cycle at the appropriate position of the screen printing layer in the board according to our technological requirements.
2. PAD processing on text
Disk (PAD) can not have screen printing layer identification, to avoid virtual welding. When customers have designed PADSMT, our company will be appropriate to move processing, the principle is not to affect the identification and device compatibility.
The concept of layer and the design of the processing layer of MARK point
1. Our company takes the Top layer (i.e. Top layer) as the front face by default, and the characters of topoverlay silkscreen layer are positive.
2. If the Signal layer is drawn on the Top layer in a single panel, it means that the line on the top layer is the front surface.
3. If the Signal layer is drawn on the Top layer of a single panel, it indicates that the line on the top layer is the perspective surface.
MARK point design
4, when the customer has the surface patch (SMT) for the board file to use the Mark point positioning, must put MARK, the circular diameter of 1.0mm.
5. If the customer has no special requirement, our company will Solder 1.5mm arc to indicate the free flux to enhance its identification. The FMask layer places one
6. When the customer has a surface patch and a process edge but does not put MARK on the board file, our company generally adds a MARK point in the diagonal center of the process edge; When the customer has surface patch without process edge for the board file, it is generally necessary to communicate with the customer whether to add MARK.
About V-CUT
1. No gap is left between the splicing plate and the connecting plate of the V cut. But notice how far the conductor is from the center line of the V cut. In general, the distance between the conductors on both sides of the V-CUT wire should be more than 0.5mm, that is, the distance between the conductors and the edge of the plate in a single plate should be more than 0.25mm.
2. The expression method of V-cut line is as follows: the general shape is expressed by the keep out layer(Mech 1) layer, then the place in the board to be V CUT only needs to be drawn by the keep out layer(Mech 1) layer and it is best to mark the words V-cut at the joint of the board.
3. As shown in the figure below, the depth of residual V after cutting is generally 1/3 plate thickness, which can be adjusted appropriately according to the requirements of residual thickness of customers.
4, V cut products break apart due to the phenomenon of glass fiber is pulled loose, the size will be slightly out of tolerance, individual products will be larger than 0.5mm.
5, V-CUT knife can only go straight line, not curve and broken line; And can pull the wire plate thickness is generally above 0.8mm.
Surface treatment technology
When the customer does not have special requirements, our default surface treatment adopts HAL. (i.e. spray tin: 63 tin /37 lead)
The above DFM general technical requirements (single and double panel part) are the reference for our customers when designing PCB files, and we hope to reach some agreement on the above aspects, so as to better realize the communication between CAD and CAM, better realize the common goal of design for manufacturability (DFM), better shorten the product manufacturing cycle and reduce the production cost.
Concluding remarks
The above DFM general technical requirements (single and double panel part) are only for the reference of Shenzhen Honglijer for customers in the design of PCB files, and hope to negotiate and reconcile with each other on the above aspects, in order to better realize the communication between CAD and CAM, better achieve the common goal of design for manufacturability (DFM), shorten the product manufacturing cycle, reduce the production cost.