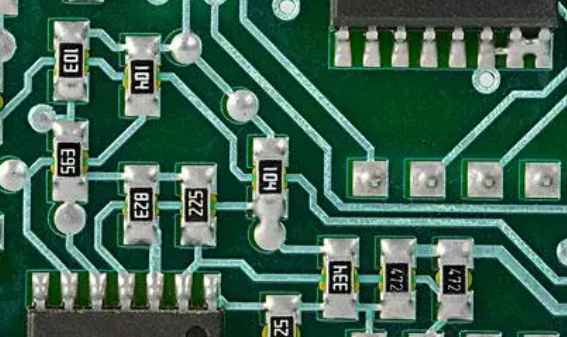
It can be seen from the above simulation results that the waveforms of scheme 1 and scheme 2 almost coincide, that is to say, the influence caused by the unequal spacing is very small, while the influence of line length mismatch on the timing is much greater (scheme 3). From the perspective of theoretical analysis, although the distance is inconsistent, the difference impedance will change, but because the coupling between the difference pairs itself is not significant, so the range of impedance change is also very small, usually within 10%, only equivalent to the reflection caused by a hole, which will not cause significant impact on signal transmission. Once the line length is not matched, in addition to the time sequence deviation, it also introduces common mode components into the differential signal, reducing the quality of the signal and increasing EMI.
It can be said that the most important rule in PCB differential routing design is to match the length of the line, and other rules can be flexibly processed according to the design requirements and practical applications.
Mistake three: Think the difference line must be very close. Keeping the differential lines close together is nothing more than to enhance their coupling, not only to improve the immunity to noise, but also to make full use of the opposite polarity of the magnetic field to counteract the electromagnetic interference to the outside world. Although this approach is very favorable in most cases, but not absolute, if we can ensure that they are fully shielded from external interference, then we do not need to achieve the purpose of anti-interference and EMI suppression through strong coupling with each other. How to ensure that differential routing has good isolation and shielding? It is one of the most basic ways to increase the distance between the lines and other signals. The energy of electromagnetic field decreases with the square relationship between the distance. Generally, when the distance between the lines is more than 4 times the width of the lines, the interference between them will be extremely weak and basically can be ignored. In addition, the isolation of ground plane can also play a good shielding role. This structure, known as CPW structure, is often used in the design of high frequency (above 10G) IC packaging PCB, which can ensure strict differential impedance control (2Z0), as shown in FIG. 1-8-19.
Differential routing can also be done in different signal layers, but this is generally not recommended because the differences in impedance and through-hole generated by different layers can destroy the effect of differential mode transmission and introduce common-mode noise. In addition, if the two adjacent layers are not coupled tightly enough, the ability of differential wiring to resist noise will be reduced, but crosstalk is not a problem if proper spacing is maintained between the adjacent lines. At the general frequency (below GHz), EMI is not a serious problem. Experiments show that the radiation energy attenuation of differential wiring with a distance of 500Mils has reached 60dB at 3 meters away, which is enough to meet the electromagnetic radiation standard of FCC. Therefore, designers need not worry too much about electromagnetic incompatibility caused by insufficient coupling of difference lines.
3. Serpentine line
Serpentine line is a kind of Layout which is often used in layout. Its main purpose is to adjust the delay and meet the requirements of system timing design. The first thing designers need to realize is that snake-like wires can destroy signal quality and change transmission delay, and should be avoided when wiring. However, in actual design, in order to ensure sufficient holding time of signals, or to reduce the time offset between the same group of signals, it is often necessary to deliberately wind.
So, what does the serpentine do to signal transmission? What should we pay attention to when we walk? The two most critical parameters are parallel coupling length (Lp) and coupling distance (S), as shown in FIG. 1-8-21. Obviously, when signals are transmitted in the serpentine line, coupling will occur between parallel line segments in the form of differential mode. The smaller S is and the larger Lp is, the greater the degree of coupling will be. It may lead to reduced transmission delay and greatly reduced signal quality due to crosstalk. The mechanism can be referred to the analysis of common mode and differential mode crosstalk in Chapter 3.
Here are some suggestions for Layout engineers to handle snake lines:
1. Try to increase the distance (S) of parallel lines to at least 3H, H refers to the distance between the signal line and the reference plane. Generally speaking, it is to go around the big bend, and as long as S is large enough, the mutual coupling effect can be almost completely avoided.
2. When the coupling length Lp is reduced, the crosstalk generated will reach saturation when the double Lp delay approaches or exceeds the signal rise time.
3. The signal transmission delay caused by Strip-Line or Embedded Micro-strip snake wire is less than that caused by Micro-strip. Theoretically, the strip does not affect the transmission rate due to differential mode crosstalk.
4. For high-speed signal lines and those with strict timing requirements, try not to use snaking lines, especially not meandering in a small area.
5. The snake-like routing at any Angle can be often adopted, and the C structure in FIG. 1-8-20 can effectively reduce the mutual coupling.
6. In high-speed PCB design, the serpentine line has no so-called filtering or anti-interference ability, which can only reduce the signal quality, so it is only used for timing matching and has no other purpose.
7. Sometimes the spiral route can be considered for winding, and the simulation shows that the effect is better than the normal snake route.