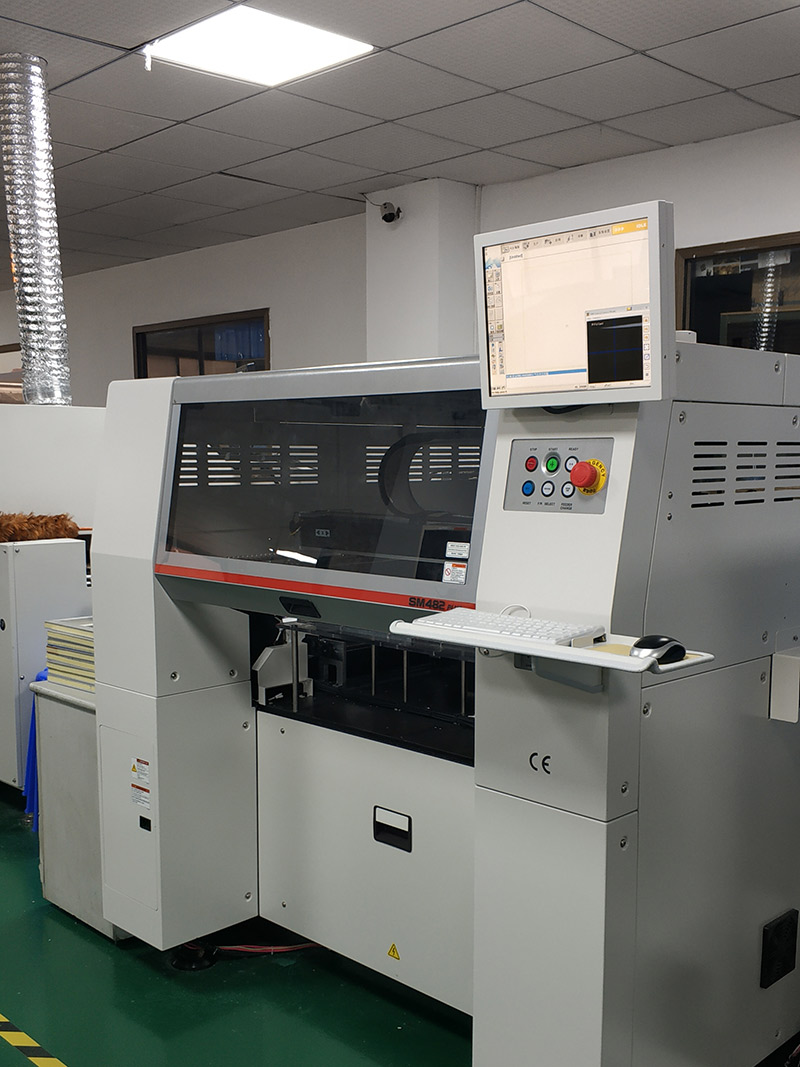
Brief introduction to the main points of SMT assembly process of BGA components
FPC factory When SMT (Surface Mount Technology)/SMD (Surface Mount Device) practitioners find that QFP (Quad Flat Package) with a pitch of 0.3mm cannot be realized, the emergence of BGA (Ball Grid Array) will definitely reduce assembly defects to ensure SMT quality achievement. From the perspective of system theory, although BGA component detection is not easy to achieve, the problem can be solved as soon as possible due to the reduction of the difficulty level of process technology, making product quality easier to control and compatible with the concept of modern manufacturing. This article will discuss and analyze the SMT assembly process of BGA components in various directions based on actual mass production.
Key points of SMT assembly process for BGA components
• Preprocessing
While some components in BGA packages are not sensitive to humidity, it is recommended that all components be baked at 125°C as no negative effects were seen in low temperature bakes. This also applies to bare PCBs (printed circuit boards) that are ready to be assembled via SMT. After all, moisture can be eliminated in the first place with fewer solder ball defects and improved solderability.
• Solder paste printing
In my assembly experience, solder paste printing is usually easy to achieve on BGA components with a pitch greater than 0.8mm and QFP components with a pitch of 0.5mm. However, sometimes there is a problem that the tin needs to be compensated by manual operation, because some solder balls do not get enough solder paste printing, causing the soldering to be displaced or short circuited.
Still, I don't think solder paste will print any easier on a 0.8mm pitch BGA component than a 0.5mm pitch QFP component. I believe many engineers have realized the difference between horizontal printing and vertical printing on QFP with a pitch of 0.5mm, which can be explained from a mechanical point of view. Therefore, some printers are capable of 45° printing. Based on the viewpoint that printing plays an important role in SMT assembly, it is recommended to give enough attention.
• Placement and installation
Based on actual assembly experience, due to the high manufacturability of BGA components due to physical characteristics, they are easier to install than QFP components with a pitch of 0.5mm. However, the main problem we have to face during SMT assembly is that vibrations usually occur on the components when they are placed on boards with a size greater than 30mm using large nozzles with rubber rings. According to the analysis, it can be considered that the pressure in the nozzle is too high due to the excessive installation strength, and it can be eliminated after appropriate modification.
•welding
In the SMT assembly process, reflow soldering with hot air is a non-intuitive process, which can also be defined as a special technique. Although BGA components have the same soldering time and temperature profile as the standard profile, it differs from most traditional SMDs in terms of reflow soldering. The solder joints of BGA components are located under the components between the component body and the PCB, which determines that BGA components are more affected on the solder joints than traditional SMD, because the latter's pins are located on the periphery of the component body. At least, they are directly exposed to hot air. Thermal resistance calculation and practice show that the solder balls in the central area of the BGA component body are affected by thermal delay, slow temperature rise and low maximum temperature.
•examine
Due to the physical structure of BGA components, visual inspection cannot meet the detection requirements of hidden solder joints of BGA components, so X-ray inspection is required to manufacture soldering defects such as voids, short circuits, missing solder balls, air holes, etc. X-ray inspection is the only The disadvantage is high cost.
• Rework
With the widespread use of BGA components, and the popularity of electronic products for personal telecommunications, BGA rework has become more and more important. However, compared with QFP components, BGA components cannot be used again once they are removed from the circuit board.
Now that BGA packaging technology has become the mainstream of SMT assembly, its level of technical difficulty can never be ignored, and the points mentioned in this article should be carefully and correctly analyzed to solve problems reasonably. When choosing an electronics contract manufacturer or assembler, you should choose a professional production line with comprehensive assembly capabilities and assembly equipment.
FPC factory When SMT (Surface Mount Technology)/SMD (Surface Mount Device) practitioners find that QFP (Quad Flat Package) with a pitch of 0.3mm cannot be realized, the emergence of BGA (Ball Grid Array) will definitely reduce assembly defects to ensure SMT quality achievement. From the perspective of system theory, although BGA component detection is not easy to achieve, the problem can be solved as soon as possible due to the reduction of the difficulty level of process technology, making product quality easier to control and compatible with the concept of modern manufacturing. This article will discuss and analyze the SMT assembly process of BGA components in various directions based on actual mass production.
Key points of SMT assembly process for BGA components
• Preprocessing
While some components in BGA packages are not sensitive to humidity, it is recommended that all components be baked at 125°C as no negative effects were seen in low temperature bakes. This also applies to bare PCBs (printed circuit boards) that are ready to be assembled via SMT. After all, moisture can be eliminated in the first place with fewer solder ball defects and improved solderability.
• Solder paste printing
In my assembly experience, solder paste printing is usually easy to achieve on BGA components with a pitch greater than 0.8mm and QFP components with a pitch of 0.5mm. However, sometimes there is a problem that the tin needs to be compensated by manual operation, because some solder balls do not get enough solder paste printing, causing the soldering to be displaced or short circuited.
Still, I don't think solder paste will print any easier on a 0.8mm pitch BGA component than a 0.5mm pitch QFP component. I believe many engineers have realized the difference between horizontal printing and vertical printing on QFP with a pitch of 0.5mm, which can be explained from a mechanical point of view. Therefore, some printers are capable of 45° printing. Based on the viewpoint that printing plays an important role in SMT assembly, it is recommended to give enough attention.
• Placement and installation
Based on actual assembly experience, due to the high manufacturability of BGA components due to physical characteristics, they are easier to install than QFP components with a pitch of 0.5mm. However, the main problem we have to face during SMT assembly is that vibrations usually occur on the components when they are placed on boards with a size greater than 30mm using large nozzles with rubber rings. According to the analysis, it can be considered that the pressure in the nozzle is too high due to the excessive installation strength, and it can be eliminated after appropriate modification.
•welding
In the SMT assembly process, reflow soldering with hot air is a non-intuitive process, which can also be defined as a special technique. Although BGA components have the same soldering time and temperature profile as the standard profile, it differs from most traditional SMDs in terms of reflow soldering. The solder joints of BGA components are located under the components between the component body and the PCB, which determines that BGA components are more affected on the solder joints than traditional SMD, because the latter's pins are located on the periphery of the component body. At least, they are directly exposed to hot air. Thermal resistance calculation and practice show that the solder balls in the central area of the BGA component body are affected by thermal delay, slow temperature rise and low maximum temperature.
•examine
Due to the physical structure of BGA components, visual inspection cannot meet the detection requirements of hidden solder joints of BGA components, so X-ray inspection is required to manufacture soldering defects such as voids, short circuits, missing solder balls, air holes, etc. X-ray inspection is the only The disadvantage is high cost.
• Rework
With the widespread use of BGA components, and the popularity of electronic products for personal telecommunications, BGA rework has become more and more important. However, compared with QFP components, BGA components cannot be used again once they are removed from the circuit board.
Now that BGA packaging technology has become the mainstream of SMT assembly, its level of technical difficulty can never be ignored, and the points mentioned in this article should be carefully and correctly analyzed to solve problems reasonably. When choosing an electronics contract manufacturer or assembler, you should choose a professional production line with comprehensive assembly capabilities and assembly equipment.