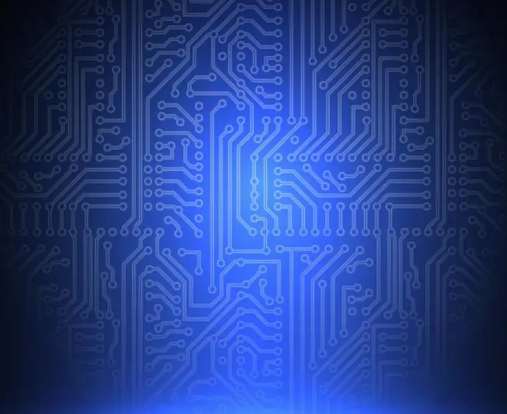
First, The Processing Level Is Not Clearly Defined
The single panel design is on the TOP layer, if it is not specified, it may be made out of the board to install the device and not good welding.
Second,Large Area Copper Foil Is Too Close To The Outer Frame
The spacing between large area copper foil and outer frame should be at least 0.2mm, because it is easy to cause the copper foil to warping and the solder resistance to fall off when milling the shape.
Third, Use The Filler Block To Draw The Pad
Drawing PCB pad with filler blocks can pass DRC inspection when designing the circuit, but it is not good for machining, so the pad cannot directly generate solder resistance data. When applying solder resistance, the filler block area will be covered by solder resistance, resulting in difficulty in welding the device.
Fourth, The Electric Formation Is The Welding Pad And The Connection
Because the design is a flower welding pad power supply, the formation is the opposite of the actual printed board image, all lines are isolation lines, drawing several groups of power supplies or several types of ground isolation lines should be careful, can not leave a gap, so that the two groups of power short circuit, can not cause the connection area blocked.
Fifth, The Character Is Misplaced
Character cover pad SMD weld, which brings inconvenience to PCB on-off test and component welding. The character design is too small, resulting in screen printing difficulties, too large so that the characters overlap each other, difficult to distinguish.
Sixth, The Surface Mount Device Pad Is Too Short
This is for the on-off test, for the too dense surface mount device, the distance between the two feet is quite small, the pad is also quite thin, the installation of the test needle must be staggered up and down, such as the pad design is too short, although it does not affect the installation of the device, but will make the test needle wrong.
Seventh, Single-Side Pad Aperture Setting
Single side pad is generally not drilled, if the drilling needs to be marked, its aperture should be designed to be zero. If you design the values so that when the drilling data is generated, the hole coordinates appear at this location, and there is a problem. Single side pad should be specially marked if drilled.
Eighth, Pad Overlap
During the drilling process, the drill bit will be broken due to multiple holes in the same place, resulting in hole damage. The two holes in the multilayer plate overlap, and the film is drawn as an isolation plate, resulting in scrap.
Ninth, There Are Too Many Filling Blocks In The Design Or The Filling Blocks Are Filled With Very Thin Lines
The light drawing data is lost, and the light drawing data is incomplete. Because the filling block is drawn line by line when the light drawing data is processed, the amount of light drawing data is quite large, which increases the difficulty of data processing.
Tenth, Graphics Layer Abuse
Some useless connections were made on some graphic layers, and more than five layers of lines were designed on the original four-layer board, causing misunderstanding.
Against conventional design. The graphic layer should be kept complete and clear during design.
Eleventh, Hot Melt Plastic Film Plate Making Method:
This method is collected from online articles, the feasibility has not been verified, for reference.
① On the printer, the circuit board diagram is printed on 80 grams of copy paper at a ratio of 1:1. Hand painting is also acceptable, but the backing paper should be flat.
② Find a fax machine, take out the fax paper in the machine, and replace it with hot melt plastic film. Put the circuit diagram into the fax machine entrance, and use the copy key of the fax machine to copy the circuit diagram on the hot melt plastic film. At this time, the "printed manuscript" of the printed circuit board is done.
③ Paste the plastic film of the finished drawing on the copper plate with double-sided tape paper. Note that it should be smooth and not wrinkled, and the tape paper should not cover the melted part, otherwise it will affect the production effect of the circuit board.
④ Brush the paint evenly on the plastic film, note: can not reciprocate the brush, can only brush in one direction, otherwise the plastic film wrinkles together, the lines on the copper plate will overlap. After the circuit diagram has been brushed all over, carefully remove the plastic film. At this time a printed circuit board is printed. Let dry, it will corrode.
If you want to print more pieces, you can make a wooden frame larger than the circuit board, the screen is flat on the wooden frame, fixed. Then use double-sided tape paper to fix the plastic film under the screen. Put the copper coated plate on the table, close the screen frame (the printing picture and the copper coated plate should be aligned left and right), brush the paint in one direction, and remove the net frame. The printed circuit board is printed. If there is any defect, it can be modified with paint and bamboo.
The above process should be noted that when painting, the hand force should be appropriate, too heavy paint film is too thick, the line will run lace, too light line will break the line. The plastic film must face up.