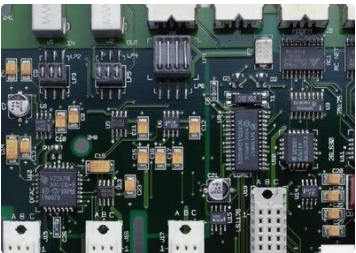
In PCB production, there are two laser technologies that can be used for laser drilling. The CO2 laser wavelength is in the far infrared wave band, and the ultraviolet laser wavelength is in the ultraviolet wave band. CO2 laser is widely used in the fabrication of industrial micro vias for printed circuit boards. The diameter of the micro vias is required to be greater than 100 μ m (Raman , 2001) . For the fabrication of these large aperture holes, CO2 laser has high productivity, because the punching time required for CO2 laser to fabricate large aperture holes is very short. Ultraviolet laser technology is widely used in diameter less than 100 μ With the use of miniature circuit diagram, the pore diameter can even be less than 50 μ m 。 Ultraviolet laser technology is used to make the diameter less than 80 μ The yield of m hole is very high. Therefore, in order to meet the increasing demand for microporous productivity, many PCB manufacturers have begun to introduce dual head laser drilling systems- The following are the three main types of PCB hybrid laser drilling systems used in the PCB market today:
1) Double head ultraviolet drilling system;
2) Double head CO2 laser drilling system;
3) Stick laser drilling system (CO2 and UV).
All these types of drilling systems have their own advantages and disadvantages. The laser drilling system can be simply divided into two types: dual bit single wavelength system and dual bit dual wavelength system. Regardless of the type, there are two main parts that affect the ability of drilling:
1) Laser energy/pulse energy;
2) Beam positioning system.
The energy of the laser pulse and the transmission efficiency of the beam determine the drilling time. The drilling time refers to the time when the laser drill drills a micro through hole. The beam positioning system determines the speed of moving between the two holes. These factors together determine the speed of laser drilling machine to make micro through-hole with given requirements. The dual head UV laser system is most suitable for use in integrated circuits smaller than 90 μ M, and its aspect ratio is also very high.
The dual head CO2 laser system uses a Q switched RF excited CO2 laser. The main advantages of this system are high repeatability (up to 100kHz), short drilling time, wide operation area, and only a few shots are needed to drill a blind hole, but the drilling quality is relatively low.
The most common dual head laser drilling system is the hybrid laser drilling system, which consists of an ultraviolet laser head and a CO2 laser head. This comprehensive hybrid laser drilling method can facilitate the simultaneous drilling of copper and dielectric. That is, use ultraviolet ray to drill copper to generate the size and shape of the required hole, and then use CO 2 laser to drill uncovered dielectric. The drilling process is completed by drilling 2in X 2in blocks, which are called domains.
CO2 laser effectively removes dielectrics, even inhomogeneous glass reinforced dielectrics. However, a single CO2 laser cannot make small holes (less than 75 μ m) And removing copper, there are a few exceptions, that is, it can remove the 5 μ Thin copper foil below m (lustino, 2002). Ultraviolet laser can make very small holes, and can remove all ordinary copper streets (3 - 36 μ m. 1oz, even plated copper foil). Ultraviolet laser can also remove dielectric materials independently, but at a slower speed. Moreover, for non-uniform materials, such as reinforced glass FR - 4, the effect is usually poor. This is because the glass can only be removed when the energy density is increased to a certain extent, which will also damage the bonding pad of the inner layer. As the stick laser system includes ultraviolet laser and CO 2 laser, it can achieve the best in both fields. With ultraviolet laser, all copper foils and small holes can be completed, and with CO 2 laser, dielectric can be drilled quickly. Figure 10-14 shows the structure of the dual head laser drilling system with programmable drill distance. The spacing between two drill bits can be adjusted according to the layout of components, which ensures the maximum laser drilling capacity.
Now, in most double head laser drilling systems, the distance between two drill bits is fixed, and the step repeat beam positioning technology is also available. The advantage of the step and repeat laser remote regulator itself is that the range of adjustment is large (up to (50 X 50) μ m) 。 The disadvantage is that the laser remote regulator must move step by step in a fixed area, and the distance between two drill bits is fixed. Typical double head laser remote adjuster The distance between two drill bits is fixed (about 150 μ m) 。 For different panel sizes, fixed distance drills cannot be operated in the same optimal configuration as programmable spacing drills.
Nowadays, the double head laser drilling system has various performances of different specifications, which can be applied to small PCB manufacturers as well as mass production PCB manufacturers.
Because ceramic alumina has a high dielectric constant, it is used to manufacture printed circuit boards. However, because it is fragile, the drilling process required for wiring and assembly is difficult to complete with standard tools, because the mechanical pressure must be reduced to the minimum, which is a good thing for laser drilling. Rangel et al. The use of a short pulse, low energy, high peak power laser helps to avoid the damage of mechanical pressure to the sample, and can produce an aperture less than 100 μ M high quality through hole. This PCB fabrication technology has been successfully applied to low noise microwave amplifiers in the frequency range of 8 - 18GHz.