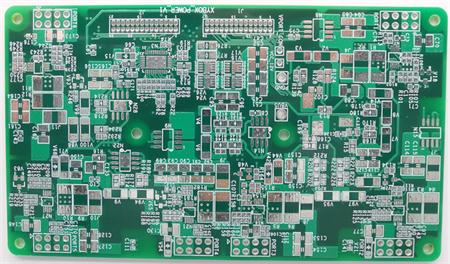
The development of science and technology has made the industry more and more subdivided. The electronic industry is the most thoroughly globalized and market-oriented field at present, and the pursuit of high and new technology and low cost is the inevitable trend of the development of the electronic industry. Only with high product quality and low cost advantages, the quality of the circuit board factory is the quality level of the product, and is the collection of quality, reputation, responsibility and culture. The requirements of the PCB factory generally include the following aspects:
Circuit board factory
(1) Appearance requirements
PCB processing plants usually have stricter requirements on the appearance, which requires that the surface should be free of pollution, inclusions, fingerprints and oxidation, so as to prevent affecting solderability and insulation. The color of solder mask pattern shall be consistent, without peeling, missing printing, deviation or oil leakage, so as to prevent affecting welding. The plate edge shall be smooth and clean without concave convex or burr, so as not to affect the assembly size and insulation. The conductor shall be uniform without corrosion, notch and residual copper, so as to avoid affecting the electrical performance. The marking symbols shall be clear and shall not be pasted and readable to prevent affecting assembly and maintenance. There is no scratch on the surface to avoid affecting the welding assembly and electrical performance. There shall be no blistering or delamination between conductors or insulation layers, especially multilayer plates, to avoid affecting mechanical and electrical properties.
(2) Electrical performance requirements
It is very important to set a proper electrical gap between the conductors of the multilayer circuit board. Proper line spacing can prevent flash soldering and breakdown between the relevant conductors in PCB processing, and can successfully pass the review of relevant product safety standards. In the industrial standards and safety standards of PCB products, different working voltages, different applications and other factors have different regulations on the electrical clearance and creepage distance between conductors.
(3) Mechanical performance requirements
Before the circuit board is opened, the copper clad laminate must be dried to ensure that the water vapor volatile resin in the board is completely cured; The material opening shall be carried out in strict accordance with the longitude and latitude directions in the material opening instructions; When laminating and typesetting, it shall be opened according to the longitude and latitude directions of PCB processing plates. During typesetting, the longitude and latitude directions shall be distinguished first, and then typesetting shall be conducted according to the distinguished longitude and latitude directions to ensure that the longitude and latitude directions are consistent. It is not allowed to adjust the cold pressing time without permission, and records shall be made to ensure that the stress in the board is completely released and the resin is completely cured; When baking the characters of circuit boards at high temperature, the shelf shall be adjusted according to the size of the board. The board shall not be bent or twisted when inserting the shelf. The boards with different sizes shall be inserted separately for baking.
(4) Environmental resistance and other performance requirements
The multilayer circuit board has the properties of environmental resistance, mold resistance, moisture resistance, cooking resistance, temperature impact resistance, etc. The formation of PCB fastboard product quality runs through the whole process of product formation, and the quality of PCB products is related to the whole manufacturing process. Every PCB factory should pay special attention to quality. Quality is produced, not inspected. Think of yourself as the consumer of the previous process and the customer of the next process. Behind each circuit board, there are a group of quality assurance personnel silently conducting quality inspection. A perfect quality control system is required by every PCB factory.