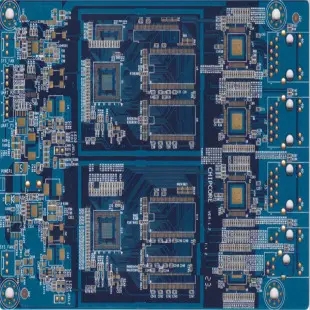
Function and Operation Procedure of Bottom Filler in PCB Production
Function and Operation Procedure of Bottom Filler in PCB Production
Underfill was originally designed for Flip Chip to enhance its reliability.
Because the coefficient of thermal expansion of silicon clad chips is much lower than that of general PCB materials, there is often a relative displacement in thermal cycles testing, which leads to mechanical fatigue and leads to the problem of solder joint falling off or fracture. Later, this technology was applied under some BGA chips to improve the reliability of falling/falling when they were welded to the circuit board.
The bottom filler is usually made of epoxy resin, which uses the principle of capillarity to coat epoxy on the edge of the chip so that it can penetrate into the bottom of the coated chip or BGA, and then is heated to cure. Because it can effectively improve the mechanical strength of solder joints, thus improving the service life of the chip, it is currently mostly used in the design of some handheld devices, such as mobile phone circuit boards. Because handheld devices must pass the rigorous drop test and tumble test of bare metal, many BGA solder joints can hardly withstand such rigorous test conditions, especially some boards with ENIG surface treatment.
The steps of adding the bottom filler are usually arranged after the circuit board is assembled, that is, SMT, Wave Solder and hand welding parts are completed, and all functions of the board are confirmed to be OK after the electrical test is completed. Because it is difficult to repair or rework the core after underfill.
After the bottom filler is added, it needs to be baked at high temperature to speed up the curing time of the epoxy resin. In addition, it can also ensure that the filler under the chip is really cured. Generally, the epoxy resin can be cured slowly when placed at room temperature, but it takes at least 24 hours, depending on the length of contact with the air, Some epoxy resin components will also be added with some metal element additives. When selecting, you must pay attention to the surface impedance of its liquid and solid state, otherwise there will be a chance of current leakage.
When adding the bottom filler, generally, epoxy resin will only be added in the L-shaped path on the adjacent two sides of the chip.
Here are some steps for operating underfill with Loctite 3536 for reference only:
1. Loctite 3536 must be stored at a low temperature of 5 ℃ (Loctite requires a temperature between 2 ℃ and 8 ℃). It must be returned to the room temperature for at least 1 hour before being used.
2. The circuit board to be underfil shall be preheated to 70 ℃ during glue filling.
3. Start dispensing the BGA chip with the L-shaped path for the first time. As shown in the figure below, place Loctite 3536 on the edge of the BGA chip.
4. Wait about 30~60 seconds for Loctite 3536 to penetrate into the bottom of BGA.
5. For the second L-shaped path dispensing of BGA chip, the amount of glue should be a little less than that of the first. Wait about 60 seconds to observe whether the black glue has spread around the BGA and formed a slope coating chip. (This purpose is to ensure that the underfill under the chip has the least bubbles or cavities.)
6. After confirming that the glue filling is correct, put the circuit board filled with glue into the oven and bake it to 130 ℃+20 minutes. (Loctite does not recommend baking at a temperature above 140 ℃)
7. After baking, check whether the appearance of the sealant is black and bright, and touch it gently with your nails to see whether it is smooth and hard.