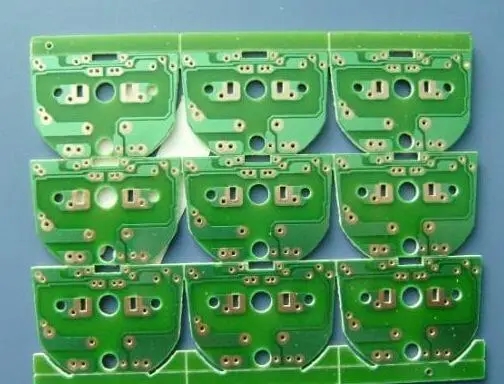
Limitation on SMT's adoption of "Yin Yang Board" or "Mandarin Duck Board"
Although it can increase the efficiency of SMT production line and save material costs by converting PCB panels into [Yin Yang boards or Mirror boards], these two [Yin Yang boards] have their own shortcomings and limitations. This paper will discuss and seek solutions.
As for the "negative and positive plates with reversed front and back sides", the limitation is that it is not recommended to use them on plates with heavy parts, because heavy parts are usually placed on the second side before they are punched, which can avoid the risk of solder paste falling off when heavy parts pass through the second reflow oven.
Method 1: Dispense glue under heavy parts. The early SMT line, red glue dispensing process and dispensing machine are necessary equipment, because the glued parts can be taken to wave soldering, and the current SMT line does not necessarily have this equipment. If not, you can also consider dispensing by hand, but I don't recommend it, because the quality of manual operation is difficult to control.
Method 2: Use carrier. The carrier of the over reflow furnace can be designed to just support the heavy parts, so that the heavy parts will not be easy to fall down when reflow welding for the second time. However, the cost of a vehicle is not cheap, and the total number of vehicles arranged should be greater than the length of the reflow oven, that is, to calculate how many plates are in the reflow oven at the same time during the travel period, plus the spare parts (buffer), it will cost nothing to add up to more than 20 if there are no more than 30. In addition, because the vehicle needs to withstand the high temperature of repeated reflow soldering, it is generally made of metal or special high temperature resistant plastic. There is also a special reminder that the use of Carrier will require an additional labor cost. It also requires labor to put boards on Carrier.
Method 3: Hand weld heavy parts. I do not recommend this method because it is difficult to control the quality manually and some parts are not easy to be welded by hand.
In addition, there is another problem with the "negative and positive boards with reversed sides". Some boards may use heat absorbing parts on one side (such as large ATM card reading slots). These parts need a long heating time to reach the melting temperature of solder paste, but they cannot burn other vulnerable parts. This kind of board needs to pay special attention to the adjustment of reflow profile.
As for the "upside down yin and yang boards on the same side", it is basically not helpful for the efficiency of SMT lines, but it can achieve the purpose of saving boards. How to cut board edges is only a problem that needs to be considered for this kind of panel. Normally, V-Cut can be used to cut the edges of boards in a normal way, which is less costly. However, it is limited to assembling yin and yang boards, because V-Cut can only be used for straight line cutting, and the curved edges depend on the Router. For details, refer to the article "Removing the edges of boards from circuit boards - V-Cut board splitter".
Cross boards are easy to be created after panel assembly, and the more panels are assembled, the more opportunities there are for X-boards. X-board is an inevitable product in the manufacturing process of the board factory. The so-called X-board is that there is more than one defective board in the panel. Generally, the board factory will mark an X on the defective board with a signature pen, so it is called X-board. Most SMT printing factories do not want to accept this kind of board, because it will cause efficiency loss, but this kind of circuit board cannot be absolutely avoided in the process of manufacturing. Therefore, the more boards connected, the more the number of discarded boards will be, and the relative cost will be increased. Therefore, circuit board manufacturers will hope that the number of connected boards is as small as possible, because this can avoid the loss of X-board. Of course, the wool still comes from sheep. If the board factory has been unable to overcome the loss of X-board, the final price will be reflected to the customer.
In fact, some professional OEM factories will make the panel manually, but they need to use some skills and have to admire their ideas.