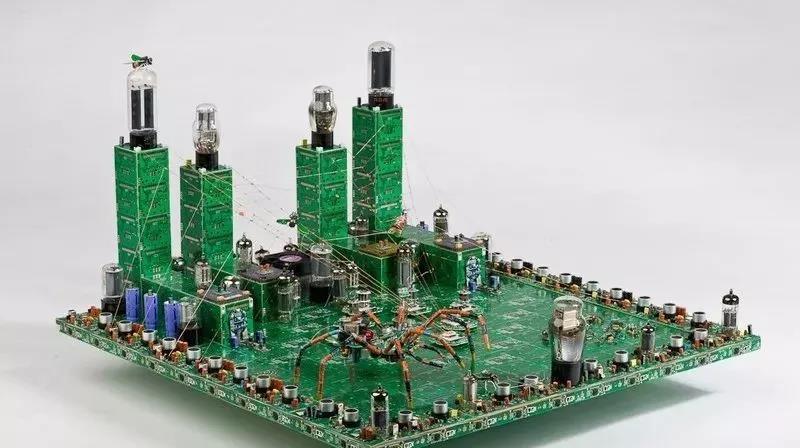
Influence of Printing Equipment and Printing Process Parameters on Solder Paste in SMT Process
Printing machine is the equipment that prints solder paste onto PCB board, which has the greatest impact on process and quality. At present, printing presses are mainly divided into manual printing presses, semi-automatic printing presses and full-automatic printing presses.
Semi automatic printing machine: simple operation, fast printing speed and simple structure. Its disadvantages are: less controllable points of printing process parameters, low printing centering accuracy and poor solder paste demoulding. It is generally applicable to PCB printing process with components above 0603 and pin spacing greater than 1.27mm.
Full automatic printing machine: high printing centering accuracy, good solder paste demoulding effect, stable printing process, suitable for the printing of narrow spacing components of dense devices; Disadvantages are: high maintenance costs and high requirements for knowledge level of operators.
4、 SMT printing process parameters
1. Pattern alignment
The base plate on the workbench is aligned with the steel mesh, so that the pattern of the base plate pad is completely coincident with the pattern of the steel mesh opening.
2. Angle between scraper and steel mesh
The smaller the angle between the scraper and the steel mesh, the greater the downward pressure. It is easy to inject solder paste into the mesh, but it is also easy to squeeze solder paste to the bottom of the steel mesh, causing solder paste adhesion. Generally, the included angle between scraper and steel mesh is 45-60 degrees. At present, automatic and semi-automatic printing presses mostly use 60 degrees.
3. Solder paste input
Too little solder paste is put in, which is easy to cause poor filling, missing printing and less printing; Too much solder paste is put in, which is easy to cause the solder paste can not form rolling movement, and the solder paste can not be scraped clean, resulting in poor printing demoulding; In addition, too much solder paste exposed to air for a long time is not suitable for the quality of solder paste, and the input amount of solder paste is more appropriate to the amount of | h=13-23 mm.
During production, the operator checks the height of the solder paste strip on the steel mesh every half an hour, and moves the solder paste on the screen beyond the length of the scraper to the front of the screen with a bakelite scraper every half an hour and distributes the solder paste evenly.
4. Scraper pressure
Scraper pressure is also an important factor affecting printing quality. The scraper pressure actually refers to the drop depth of the scraper. If the pressure is too small, the scraper does not stick closely to the surface of the steel mesh. In addition, if the pressure is too small, a layer of solder paste will remain on the surface of the steel mesh, which is easy to cause printing defects such as printing, forming and bonding.
5. Printing speed
Because the speed of the scraper is inversely proportional to the viscosity of the solder paste, the PCB has narrow spacing, and the speed is slower for high-density graphics. If the speed is too fast, the time for the scraper to pass through the steel mesh opening is relatively short, and the solder paste cannot fully penetrate into the opening, which may cause printing defects such as insufficient solder paste molding or missing printing.
There is a certain relationship between printing speed and scraper pressure. The ideal scraper speed and pressure should just scrape the solder paste from the steel mesh surface.
6. Printing clearance
The printing gap is the distance between the steel mesh and PCB, which is related to the amount of solder paste retained on PCB after printing.
7. Separation speed of steel mesh and PCB
After solder paste printing, the instant speed of steel mesh leaving PCB is the separation speed, which is related to the printing quality parameters. In narrow spacing, high-density printing is the most important. With advanced printing equipment, when the steel mesh leaves the solder paste pattern, there will be one or more small stay processes, namely multi-stage demoulding, which can ensure the best printing and molding.
8. Cleaning mode and cleaning frequency
The stencil pollution is mainly caused by solder paste spilling from the edge of the opening. If it is not cleaned in time, it will pollute the PCB surface, the residual solder paste around the opening of the stencil will become hard, and even block the opening of the stencil in serious cases.
Cleaning the bottom of the stencil is also a factor to ensure the printing quality. The cleaning mode and frequency should be determined according to the solder paste, stencil material, thickness and opening size.
5、 Main Factors Affecting Solder Paste Printing Quality
1. First is stencil quality: stencil thickness and opening size determine the printing quality of solder paste. Too much solder paste will cause bridging, and too little solder paste will cause insufficient solder paste or faulty soldering. The shape of the steel mesh opening and whether the opening wall is smooth also affect the demoulding quality.
2. The second is solder paste quality: the viscosity of solder paste, the rolling property of printing, and the service life at room temperature will affect the printing quality.
3. Printing process parameters: scraper speed, pressure, the angle between scraper and screen, and the viscosity of solder paste. Therefore, only by correctly controlling these parameters can the printing quality of solder paste be guaranteed.
4. Equipment precision: when printing high-density narrow spacing products, the printing precision and repeated printing precision of the printing machine will also have a certain impact.
5. Ambient temperature, humidity and environmental sanitation: too high ambient temperature will reduce the viscosity of solder paste. When the humidity is too high, the solder paste will absorb moisture in the air. When the humidity is too low, the volatilization of solvent in the solder paste will be accelerated. When the dust in the environment mixes with the solder paste, pinholes and other defects will occur in the solder joints.
From the above introduction, we can see that there are many factors that affect the printing quality, and printing solder paste is a dynamic process. Therefore, it is very necessary to establish a complete set of printing process control documents. Selecting the correct solder paste and stencil, combined with the most appropriate printer parameter settings, can make the entire printing process more stable, controllable and standardized.
PCB manufacturers, PCB designers and PCBA processors will explain the influence of printing equipment and printing process parameters on solder paste in SMT process.