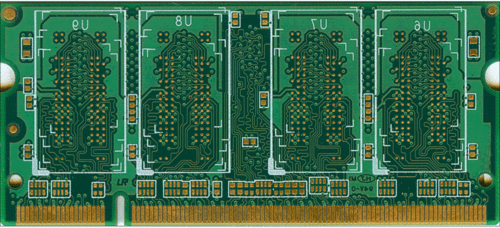
Processing details of high-precision multilayer boards, producing high-quality PCB
The core of high-precision multilayer circuit board is the pressing process between multilayer boards. Because customers have not been engaged in PCB production, they usually lack understanding of the pressing process and are not very familiar with the production process and production standards of various manufacturers. This has led to quality control problems such as obvious layering, warping, and even open inner layers after obtaining the multilayer board. I will reveal a secret to you today. The main reason for this quality control problem is that the production line of the factory is not complete enough, and the pressing process can only be outsourced to amateur pressing plants. Many of them have many defects in process, equipment and talents, which leads to unreliable pressing quality. Common problems include:
● The substitute factory is not equipped with a hot-melt machine and an X-RAY drilling target machine, but only uses the riveting process to press. The tolerance of rivet holes will affect the alignment accuracy between multi-layer plates. The impact of the press during pressing will lead to rivet deformation, resulting in interlayer offset
(The solution is to increase the spacing between holes and lines to reduce the scrap rate of high-precision boards, but this also limits the customer's PCB design)
● The crimping machine equipment in the substitute factory is old, with high failure rate. Frequent shutdown events result in low production efficiency, unable to deliver on time, and affecting the delivery date
● Avoid process defects such as warping and layering caused by excessive glue flow and uneven glue content between inner layers, and fully ensure the high yield of laminated boards!
● Extremely low failure rate and precise automatic control can reduce production risk, maintain efficient and stable production, and save customers time!
Finally, the requirements and standards of high reliability and stability are realized.
MVLP vacuum and pressurization process: The vacuum chamber is composed of upper and lower hot plates, with heaters built in respectively. When the product is installed in the hot plate, the hot plate will be closed (forming a chamber), and the interior will be in a vacuum state. After the set time, the air cushion expands with the supply of compressed air to press the product on the hot plate. The pressing force and heat are used for pressing.
In addition, what other factors will affect the compression yield?
(1) Quality of laminated steel plate:
The steel plate is one of the core accessories for pressing. The poor hardness and flatness of the laminated steel plate will have a huge impact on the process. If the quality is not up to standard, it will cause serious consequences for PCB production (such as low precision of the pressing thickness tolerance, indentation on the board surface, etc.)
(2) High precision X-RAY target drilling machine and hot-melt machine:
The X-ray target drilling machine is used for the interlayer alignment after pressing. The principle is to project the bonding pad through X-ray fluoroscopy after pressing the multilayer board, judge the fit between the inner layers and drill holes at the location (drilling target); The hot-melt machine is used to bond and fix the PP plate and core plate through high temperature and pressure (commonly known as "fusion"), while the ordinary riveting process is used to press. The alignment accuracy between layers is affected by the rivet hole tolerance, and the impact during pressing will lead to rivet deformation, resulting in inter layer offset.
(3) PP adhesive sheet:
PP sheet is a kind of sheet material, in which the resin is in the B-stage. Under the action of temperature and pressure, it has fluidity, can quickly cure and complete the bonding process, and forms an insulating layer with the carrier. The quality of PP sheet also affects the reliability and stability of the multilayer board.
PCB manufacturers, PCB designers and PCBA processors explain the processing details of high-precision multilayer boards and produce high-quality PCBs.