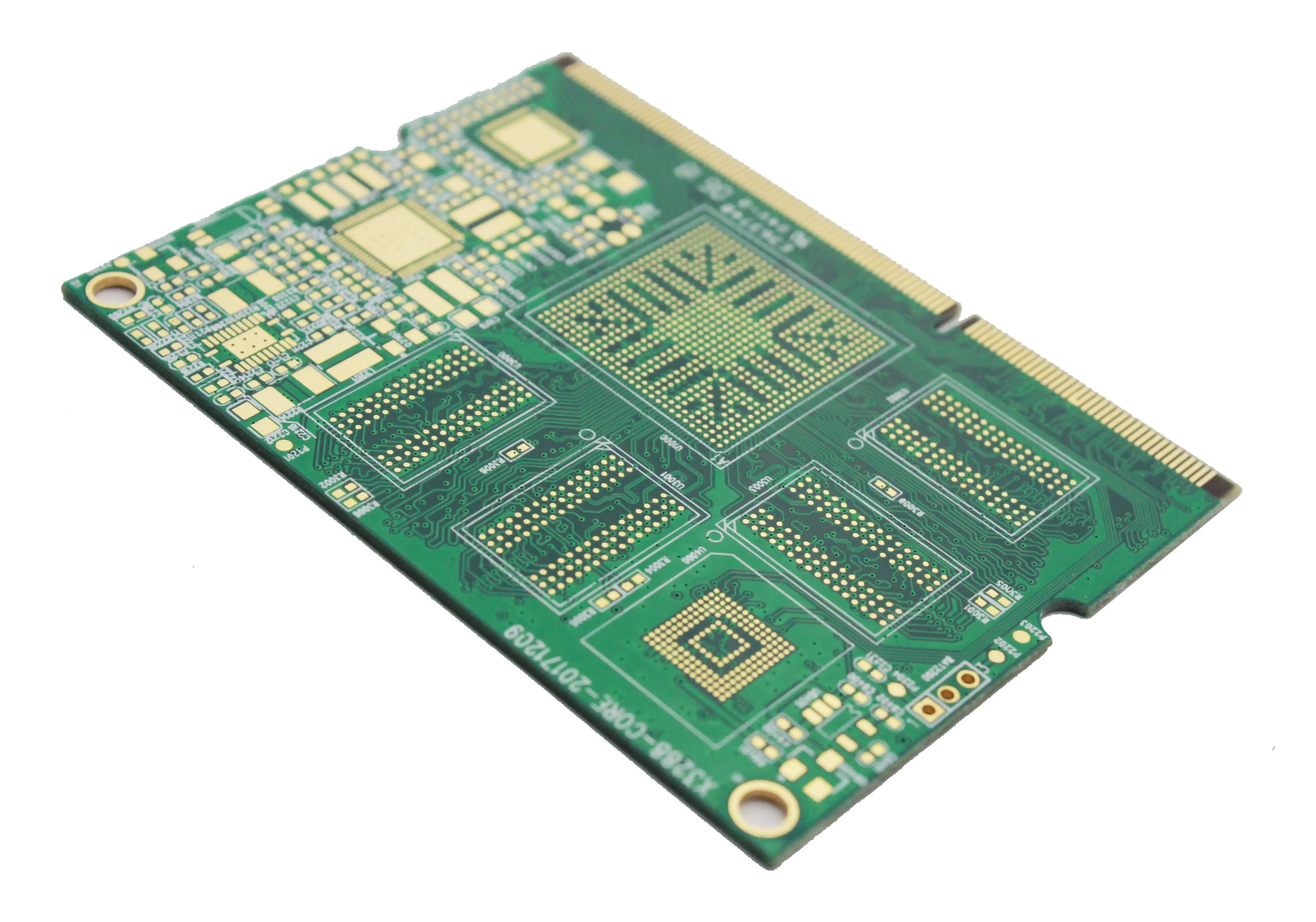
Detailed explanation of inspection methods and processes that PCB has to know
PCB manufacturers, PCB designers and PCBA manufacturers will explain the basic inspection methods and processes of PCB
Since the first batch of computers were produced, the progress of electronic technology has been very magnificent. However, the credit of all this is the integration of circuit systems. Whether it is a semiconductor chip or a circuit board, in essence, it is to save space and integrate complex cables into a small space. But this also brings a problem, that is, after manufacturing, the integration is very high, and later maintenance is basically impossible, so we can only do a good job of testing and prevention when leaving the factory. At present, the lightweight of all kinds of equipment puts forward higher requirements for PCB quality inspection, and the traditional inspection can no longer meet the requirements of PCB production industry for quality control. As the most important component and connection unit of modern electronic equipment, PCB has a large installation density and a small volume of SMD components, so it is required to continuously improve the integration of PCB. The quality of the motherboard directly affects the quality of the entire electronic product, so PCB detection equipment is very important. The last step of PCB production is to carry out quality inspection. Various tests in the factory are an inspection method to find problems in time and provide reliable products, as well as a necessary means to prevent losses caused by product quality.
Key points of PCB inspection:
1. Test the insulation performance of the electric soldering iron when PCB board is to be welded;
2. Test whether the pins of the circuit board are short circuited;
3. Check that the PCB board test instrument meets the standard, and the built-in resistance should be sufficient;
4. Pay attention to the power when testing the circuit board and monitor the heat dissipation of the integrated circuit to avoid danger;
5. Detect PCB board leads reasonably and reliably;
6. Detect the welding quality of PCB under welding;
7. Do not arbitrarily judge whether the integrated circuit is damaged when detecting the PCB board
8. Master the working principles of integrated circuits and related circuits before testing PCB boards
What should be done before PCB testing? First of all, the environment and requirements of the equipment during operation shall be clarified. The primary factor is the possible influence of external electrical parameters on the equipment. Then, observe the phenomenon of PCB failure and analyze the cause of failure. Then carefully check the SMD components on the circuit board to find out the important components in the circuit board and their impact on the function of the circuit board. Finally, anti static, anti electromagnetic and other anti-interference measures should be taken.
PCB detection methods include the following: the first method is manual visual inspection, but the cost of this method is relatively high, and human eye fatigue may cause certain errors due to long-time visual inspection of PCB. In addition, with the continuous improvement of modern PCB integration, the wire spacing and the volume of patch components are shrinking, which also increases the requirements for visual inspection. With the specialization of PCB production, there is also the factor of output, and the manual visual inspection method is more and more backward; The other is the function test of the circuit board. The function system test refers to the comprehensive test of the functional modules of the circuit board using special test equipment in the middle process stage of the production line and the early shipment stage to confirm whether the circuit board has failed. It requires special equipment and specially designed test flow, and it is tedious to write functional test program, so it is not suitable for most circuit board production lines. But nowadays, there is a single dimension detection which is relatively more applied. It uses a plane image system measuring instrument to measure the position, length and width, hole position and other shape data. PCB is a precision machined and fragile product. Contact measurement is easy to cause PCB deformation and inaccurate measurement. Planar image measuring instrument has become the best choice for high-precision dimension measuring instruments. After programming, the plane image measuring instrument can realize full automatic measurement. At the same time, it has the triple effect of high measurement accuracy, greatly shortening the measurement time and improving the measurement efficiency.
The above is a step that has the greatest impact on the quality of PCB production, so as to ensure the ex factory quality of products.