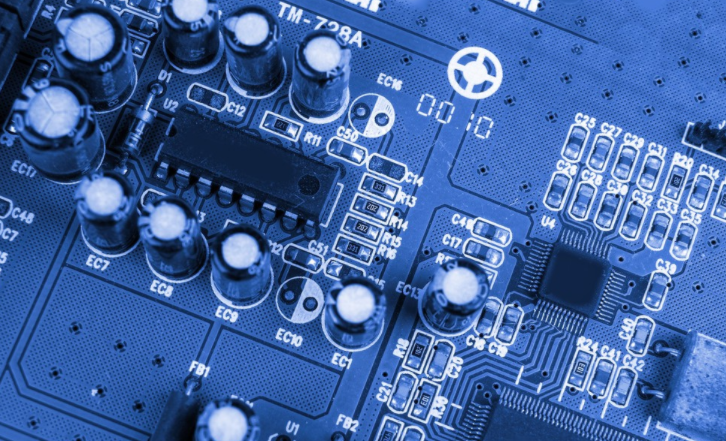
How SMT Technology Produces Mobile Phones
Mobile phones, computers, tablets and other electronic devices are an indispensable part of people's life today Do you have any problems during the use? Is this the electronic equipment in our hands? From?
Next, we will introduce a surface mount technology (SMT) for the production of all electronic devices.
In simple terms, surface mounting is to print solder paste on a fixed point on the PCB, and then install resistors, capacitors and other components on the surface of the PCB through mechanical equipment, and then bake the circuit board at high temperature to solidify the solder paste, so that the components are firmly welded to the circuit board to form a complete circuit board component.
The SMT production line is mainly composed of the following equipment: solder paste printer, solder paste inspection equipment (SPI, Solder Paste Inspection), placement machine, AOI (Automated Optical Inspection), reflow soldering furnace, loading and unloading machine, barge equipment, return station and other equipment
Circuit board
Among them, solder paste printer, mounter and reflow furnace belong to processing equipment, SPI and AOI belong to inspection equipment, as well as upper and lower plate machines, connecting equipment, rework station and other auxiliary equipment.
SMT production line is usually built in the order of loading machine solder paste printer solder paste detection equipment (SPI) - unloading machine at AOI rework station after AOI reflow in front of the mounter, interspersed with monorail or dual rail transmission and connection equipment.
Solder paste printer: place the solder paste on the designed mold, and use the mechanical arm to control the scraper to scrape the solder paste from one end of the mold to the other end. The solder paste will leak out of the template hole on the template. Place the PCB at the corresponding position under the mold.
Solder Paste Inspection Equipment (SPI): Detects the quality of solder paste after printing through optical principle to prevent problems such as missing printing, less tin, more tin, continuous tin, dislocation, poor shape and circuit board surface pollution.
Chip mounter: pick up components and materials through the suction nozzle, and paste the materials on the correct position of the PCB surface through the control arm.
AOI: Check whether there is displacement, leakage, polarity, skew, wrong parts, etc. through optical inspection of element placement. After reflow soldering, check whether there is less tin, more tin, displacement, poor shape, etc.
Reflux furnace: It is divided into different temperature zones, heated by hot air or infrared radiation, so that the temperature of different temperature zones in the furnace is gradient. When PCB board passes through the furnace, the solder paste will be solidified due to the temperature rise.
Circuit board loader and connector: equipment used to transfer PCB boards.
Rework station: it has the basic function of heating and is used to manually check the reworked and welded PCB boards.
The application of surface mount technology is too extensive. For example, the smart phones held by everyone now are circuit boards produced through this process, and then use circuit boards, monitors and thermal conductive adhesives through the entire machine assembly process. Assemble the glue, screen and other materials into a mobile phone. Companies including Foxconn, Huawei, OPPO, Vivo, Xiaomi and BYD have their own SMT production lines, and these large electronic manufacturers also have many foundries. Foxconn, for example, is Apple's most famous foundry.
Although the current surface mount technology is very mature, it also faces the following problems:
1. If the equipment accuracy is less than 100%, errors will still occur, resulting in scrapping of the solder PCB wall;
2. Equipment requiring manual intervention, verification and maintenance;
3. There is a risk of aging and damage to complex precision parts, leading to the risk of production line shutdown;
4. Data platforms of equipment from different manufacturers are incompatible.
Therefore, the development trend of SMT production line is very clear:
1. The device can perform closed-loop detection, which means that the device will conduct in-depth learning and self evolution through error processing to ensure that the correct processing will be performed under the same conditions next time;
2. All are interconnected, all equipment platforms are compatible, and will be connected to the enterprise MES system, so that one server can control multiple production lines at the same time, and can adjust the capacity distribution and material transportation in real time according to data;
3. The core components of the monitoring equipment, such as the new monitoring system on the hot air motor of the reflux furnace, can monitor the operation of the motor in real time, and timely conduct manual intervention in case of abnormalities;
4. The equipment has the functions of early warning and foolproof. The electronic equipment cannot guarantee that the equipment will not suffer from aging, short circuit and other phenomena. Once this phenomenon occurs, there is no early warning or foolproof function, which is for production fire safety and personnel life safety. The hidden danger is great. In this case, all smart devices will be equipped with simple functions, such as immediate alarm in case of failure, and immediate power off in case of short circuit;
5. Fully realize unmanned management. Human beings can be replaced by industrial robots and intelligent robots. All similar maintenance, inspection and other processes are completed by robots rather than humans Finally, only a few people can take care of the whole SMT factory