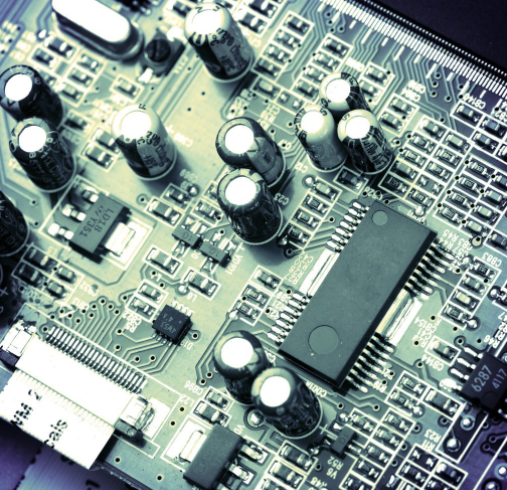
PCB conformal coating and selective wave soldering machine
Importance of PCB conformal coating thickness
PCB conformal coating thickness is one of the most important characteristics to ensure the long-term reliability of electronic equipment. The minimum coating thickness is critical to providing the required function of conformal coating, but if the conformal coating is too thick, it may actually have a negative impact on your protection level.
Which conformal coating thickness should be used for optimum protection?
If we open the technical data sheet of any conformal coating, we will find the recommended coating thickness. It is usually specified as a thickness range, not an absolute value. In order to understand why conformal coating manufacturers recommend specific ranges, we need to know some coating qualification criteria
These standards cover various test methods for measuring the effectiveness of conformal coatings, such as moisture and insulation resistance, dielectric withstand voltage, flammability (e.g., according to UL94), etc. All electrical, chemical and physical properties listed in the S&T Data Sheet are measured and evaluated using these methods. Standardized methods. Measure with different samples coated with the thickness specified in the standard.
Circuit board
All PCB coating materials shall be tested within these thickness ranges. In retrospect, for conformal coating manufacturers, this is the best reference to provide thickness ranges to ensure the given electrical and physical characteristics Indeed, the thickness values given in the technical data sheet are only recommended, not required In conformal coating applications, these recommendations may deviate, but it is important to understand the potential consequences:
Low coating thicknesses (e.g. less than 25 mm (1 mil)) may present a risk because dielectric strength and other physical properties are not tested according to standardized test methods. This does not mean that conformal coatings cannot provide the required protection for electronic equipment, but standardized test methods will not be extended to lower thicknesses.
High coating thicknesses above the upper limit rarely provide additional protection for PCBs. When the coating thickness exceeds these upper limits, it will often lead to coating defects, such as cracks, mismatch of thermal expansion coefficient and wrinkles, and increase the possibility of bubbles in the dry conformal coating film.
In short, the appropriate conformal coating thickness is the most important variable in the conformal coating process. Since PCB manufacturers carry out all standardized tests within these ranges, it is very important to keep the conformal coating thickness within the range specified in the technical data sheet. In addition, on the contrary, the possibility of coating defects mentioned earlier has increased.
Selective wave soldering machine
Selective wave soldering is a special form of wave soldering invented to meet the requirements of modern welding technology. It also has three main components: flux unit, preheating unit and welding unit. Through the pre programmed program, the machine can spray and weld the solder joints that need to be sprayed with flux. The welding efficiency and reliability are higher than manual welding, and the welding cost is lower than wave soldering.
Selective soldering technology is applicable to high-end electronic manufacturing fields, such as communications, automotive, industrial and military electronics.
Scientific and technological advantages of selective welding
The welding parameters of each welding spot can be "customized". The flux spraying amount, welding time and wave height of each welding spot can be adjusted to the best, which can reduce the defect rate, and even realize zero defect welding of hole components.
|Selective welding is only to selectively spray flux on the points to be welded. The cleanliness of this circuit board is greatly improved, and the amount of ion pollution is greatly reduced. If the sodium ion and chloride ion in the flux remain on the circuit board, the welded circuit board needs to be cleaned with air for a long time. Selective welding will fundamentally solve this problem.
The water molecules in the gas combine to form salt, corrode the circuit board and solder joint, and finally cause the solder joint to open Therefore, the traditional production method of welding is only applicable to welding at specific points No matter it is spot welding or resistance welding, it will not cause thermal shock to the whole circuit board. In summary, it will not form on surface mount devices (such as BGA) The obvious shear stress will not lead to solder joint cracking due to the overall deformation of the welded joint, thus avoiding various defects caused by thermal shock
The above is the explanation given by the editor of pcb circuit board company.
If you want to know more about PCBA, you can go to our company's home page to learn about it.
In addition, our company also sells various circuit boards,
High frequency circuit board and SMT chip are waiting for your presence again.