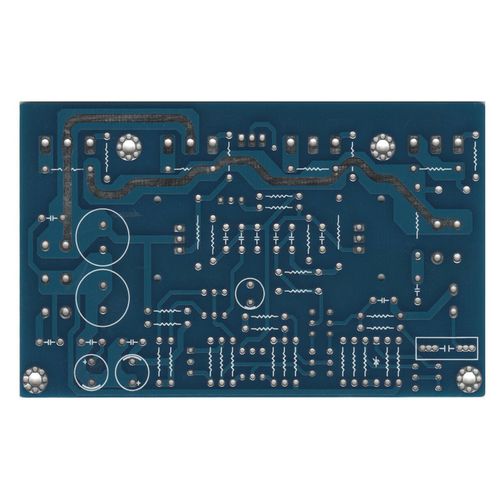
Circuit board manufacturer: the importance of impedance to PCB
What is the significance of impedance to PCB and why PCB should be impedance. Impedance actually refers to the parameters of resistance and reactance. Because the PCB circuit (bottom of the board) should consider the connection and installation of electronic components, and the conductivity and signal transmission performance should be considered after the connection, so the lower the impedance, the better, and the resistivity should be less than 1 per square centimeter × 10 to the minus sixth power.
On the other hand, during the production process of the circuit board, it must go through the steps of copper deposition, electrotinning (or chemical plating, or thermal spraying), connector soldering, and the materials used in this step must ensure the low resistivity, so as to ensure that the overall impedance of the circuit board is low enough to meet the product quality requirements, otherwise the circuit board will not operate normally.
In addition, in the electronic industry as a whole, PCB manufacturers are the most likely to have problems in the tin plating process, which is the key link to affect impedance. Because the tin plating process of PCB is now popular to use chemical tin plating technology to achieve the purpose of tin plating, but we, as the recipients of the electronic industry, have been exposed and observed in the electronic or circuit board manufacturing and processing industry for more than 10 years, There are not many domestic enterprises that can do well in electroless tin plating (used in the field of circuit board or electronic tin plating), because the electroless tin plating process is a rising star in China, and the technical level of many enterprises is uneven
For the electronic industry, according to the industry survey, the most fatal weakness of the electroless tin coating is that it is easy to change color (i.e. easy to oxidize or deliquescence), poor solderability leads to difficult welding, high impedance leads to poor conductivity or unstable performance of the whole board, and easy to grow tin must lead to short circuit of PCB circuit, even burning or fire events
It is reported that Kunming University of Science and Technology was the first to study electroless tin plating in China in the early 1990s, followed by Guangzhou enterprises in the late 1990s. Up to now, the industry has recognized that these two institutions are the best. Among them, according to our contact screening survey, experimental observation and long-term endurance test of many enterprises, it is confirmed that the chemical tin coating is a pure tin coating with low resistivity, and the quality of conductivity and brazing can be guaranteed to a higher level. No wonder they dare to ensure that their coating can keep color free, bubble free, peeling free, and permanent tin whisker free without any sealing and anti discoloration agent protection.
Later, when the whole social production industry developed to a certain extent, many of the later participants often copied from each other. In fact, a considerable number of enterprises themselves did not have the ability to research and develop or initiate. As a result, many products and their users' electronic products (PCB bottom or overall electronic products) had poor performance, and the main reason for the poor performance was the impedance problem, Because when unqualified chemical tin plating technology is used, the tin plated on PCB is not really pure tin (or pure metal simple substance), but a tin compound (that is, it is not a metal simple substance at all, but a metal compound, oxide or halide, more directly a non-metallic substance) or a mixture of tin compound and tin metal simple substance, but it is difficult to find with the naked eye alone
Because the main circuit of PCB is copper foil, and the solder joint on the copper foil is a tin coating, and the electronic components are welded on the tin coating through solder paste (or solder wire). In fact, the solder paste is welded between the electronic components and the tin coating in the melting state, which is gold tin (that is, a good conductive metal substance), so it can be simply pointed out that the electronic components are connected to the copper foil at the bottom of PCB through the tin coating, So the purity and impedance of tin coating are the key; In addition, before the electronic components are plugged in, when we directly use the instrument to detect the impedance, in fact, the two ends of the instrument probe (or called the probe) also connect the current by contacting the tin coating on the copper foil surface at the bottom of the circuit board first, and then with the copper foil at the bottom of the PCB. So tin coating is the key, the key to affect the impedance and the performance of the whole circuit board, and also the key to be easily ignored.
It is well known that, except for the metal simple substance, its compounds are all electrical poor conductors or even non-conductive (which is also the key to the existence of distribution capacity or transmission capacity in the circuit). Therefore, when such conductive but non-conductive tin compounds or mixtures exist in the tin coating, their existing resistivity or future oxidation The resistivity and its corresponding impedance after electrolytic reaction due to moisture are quite high (enough to affect the level or signal transmission in the digital circuit), and their characteristic impedance is inconsistent. Therefore, it will affect the performance of the circuit board and the whole machine.
Therefore, as far as the current social production phenomenon is concerned, the coating material and performance on the bottom of the PCB are the most important and direct reasons that affect the characteristic impedance of the whole PCB. However, because of its variability with the aging and electrolysis of the coating, the worrying impact of its impedance becomes more recessive and variable. The main reasons for its concealment are: first, it cannot be seen by the naked eye (including its changes), and second, it cannot be measured constantly, Because of its variability with the change of time and environmental humidity, it is always easy to be ignored. PCB manufacturers, PCB designers and PCBA manufacturers explain the importance of impedance to PCB in detail.