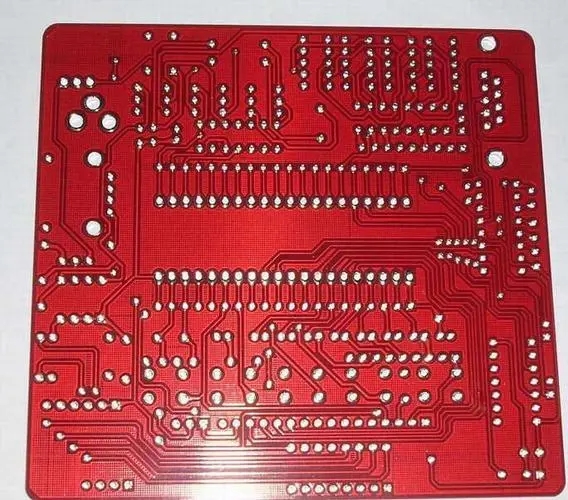
Importance of High Frequency Circuit Board and Resistance Welding Green Oil Plug Hole
PCB manufacturers, PCB designers and PCBA processors explain the importance of high-frequency PCB in electronic parts and the advantages of solder resistant green oil plug holes
High frequency circuit board is a special circuit board with high electromagnetic frequency. Generally speaking, high frequency can be defined as the frequency above 1GHz. Its physical performance, accuracy and technical parameters are very high, and are commonly used in automotive anti-collision systems, satellite systems, radio systems and other fields.
The high-frequency circuit board provided by the utility model is provided with a stop edge that can block the glue flow at the upper opening and the lower opening edge of the hollow slot of the core board, so that the glue flow will not enter the hollow slot when the core board is bonded with the copper clad plate placed on its upper and lower surfaces, that is, the bonding operation can be completed by pressing once. Compared with the high-frequency circuit board that needs to be pressed twice in the prior art, the high-frequency circuit board in the utility model has a simple structure, Low cost, easy to manufacture.
High frequency circuit board is the key interconnect of electronic products, which is also an excellent product for modernization. High frequency circuit boards also have the saying of "the mother of electronic products", because the most special part of electronic products is our high-frequency circuit boards. Without high-frequency circuit boards, the assembly of electronic components cannot be connected and assembled normally.
As the substrate loaded with sub parts and the interconnection substrate of key electronic components, high-frequency circuit boards need to be equipped with the electronic equipment and industrial products seen on the market. The industrial chain and business coverage derived from high-frequency circuit boards are quite extensive. It touches the fields of general consumer electronic products, medical skills, aerospace science and technology products. With the development of science and technology skills and the era of industrialization, the demand for electronic information processing based on high-frequency circuit boards is constantly increasing, which also promotes the benign improvement of high-frequency circuit boards in the process of development. On the basis of continuous optimization, emerging electronics continue to emerge and develop, making the market for high-frequency circuit board products continue to expand, such as our 5G era. Therefore, the market share of high-frequency circuit boards will be larger.
High frequency circuit board is the most basic component of the information industry. It belongs to the electronic assembly industry in the electronic component occupation and is the foundation of all electronic occupations. The assemblers of high-frequency circuit boards also have high requirements. In China, the assembly profession for high-frequency circuit boards is now quite mature, which is the benchmark of our modern industrialization.
Seven Advantages of Resistance Welding Green Oil Plug Hole for PCB High Frequency Circuit Board
At present, except for part pin holes, mechanical holes, heat dissipation holes and test holes, all other through holes (such as ViaHole) of the PCB high-frequency circuit board require the use of solder proof ink plug holes without being exposed. In particular, HDI high-density connection technology is becoming more and more intensive. There are more and more VIP holes and VBP holes of the PCB high-frequency circuit board used for packaging, and most of them require via plug oil. What are the advantages of using solder proof plug holes, Next, let's introduce the seven advantages of solder resistant green oil plug hole of PCB high-frequency circuit board
The green oil plug hole is used to plug green oil into the vias. Generally, two thirds of the vias are filled with green oil, which is light tight. Generally, if the via is large, the size of the ink plug hole is different according to the manufacturing capacity of the PCB high-frequency circuit board factory. Generally, the hole below 16mil can be plugged, and whether the PCB high-frequency circuit board factory can plug the larger hole should be considered.
PCB high-frequency circuit board plug hole can prevent possible short circuit caused by closely spaced devices (such as BGA). This is why vias under BGA need to be plugged in the design process. Because there is no plug hole, there has been a case of short circuit.
2. Avoid flux residues in the through hole.
3. The plug hole will be helpful to the SMT process.
4. Prevent solder beads from popping up during wave soldering, causing short circuit.
5. Prevent the solder paste on the surface from flowing into the hole, causing false soldering and affecting the mounting; This is most obvious in the heat dissipation pad plus via.
6. After the surface mounting and component assembly of the electronics factory are completed, the PCB high-frequency circuit board must be vacuumed to form a negative pressure on the testing machine.
7. The plug hole can prevent short circuit caused by tin penetrating through the component surface from the through hole when PCB high-frequency circuit board passes wave soldering; This means that there is no through hole or plug hole treatment for through hole within the range of wave soldering design area (generally the welding surface is 5mm or above). PCB manufacturers, PCB designers and PCBA processors will explain the importance of high-frequency PCB in electronic parts and the advantages of solder resistant green oil plug holes.