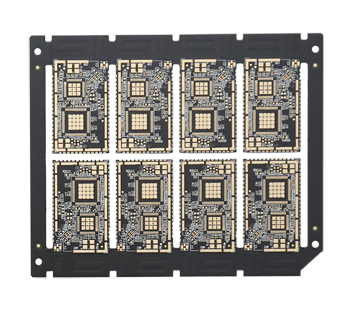
Reliability analysis of HDI lead-free digital products in long-term use
PCB manufacturers, PCB designers and PCBA manufacturers explain the reliability analysis of HDI lead-free digital products in long-term use
The reliability of lead-free HDI process digital products in long-term use needs to be noted in many aspects, and we will discuss several important issues below:
A senior reliability expert of General Motors recently said, "Do you know the problem caused by lead-free? No one can answer such a simple question: If the quality of lead-free products I make is the same as that of products using tin lead, can they work for the same length of time?"
The question is simple, and the answer is not complicated. After years of research and test, researchers have summarized the factors that affect the long-term reliability of lead-free products into the following five aspects.
Tin whisker
Kirkendall Cavity
Mechanical vibration of lead-free solder
Thermal cycling of lead-free solders
Conductive anode wire (CAF)
Let's talk about these five aspects:
Tin whisker
Tin whiskers are grown from the tin coating of components and connectors. If these conductive tin whiskers grow too long, they may be connected to other lines and cause electrical short circuit. By using 90Sn10Pb coating on device pins, the tin whisker problem has been effectively eliminated, but now this problem has arisen again.
Some HDI factory used pure tin plated devices to produce a large number of lead-free products. Tin whiskers have been found in the use process, and failures will occur in less than 2 years. Although the actual failure rate is not clear, the evidence shows that tin whisker failure does not increase the overall product repair rate. Since tin plating on thin pin devices has only occurred in the last three or four years, the impact of tin whiskers on long-term reliability remains to be observed.
If you are not designing products that may cause personal injury, you should first consider whether components and connectors have the following characteristics.
Pin spacing is less than 1mm (some companies adopt spacing less than 0.3mm)
Metal housing can be used (such as through hole crystal oscillator or oscillator)
Backlogged connection points (e.g. circuits with bent connectors)
Welds (such as electrolytic capacitors)
Once the key components have been identified, you should ask the component manufacturer to provide certification tests based on iNEMI recommendations or JEDEC standard JESD22A121. The definition of fault in the industry is almost blank, so you may need to propose your own standards. The standard can be either an absolute value, for example, the maximum whisker length cannot exceed 25, 50 or 75 μ m. It can also be a relative value (such as 1/3 or 1/2 of the minimum spacing).
Kirkendall Cavity
Between two dissimilar materials, the voids generated due to different diffusion rates are called Kirkendall voids, and this void generation mechanism exists in both SnPb and lead-free solders. In recent experiments, very serious voids were found in SnPb solder. However, during the use of surface mount technology in the past 30 years, there has been no report of product failures caused by Kirkendall cavities.
Mechanical vibration
Even if you have not encountered the Kirkendall cavity, you should be prepared for the product performance degradation caused by mechanical vibration or drop. Studies have shown that the failure load of SAC (SnAgCu) solder alloy is less than half of that of SnPb alloy when it is subjected to vibration, dropping or bending of the circuit board. This performance loss seems to be a combination of several factors, including fragile intermetallic bonding, circuit board degradation due to higher reflow soldering temperature, and greater stress transmission due to SAC being harder than SnPb.
Is this a long-term reliability problem or a quality problem from the beginning? The lead-free technology of portable electronic product manufacturers has been implemented for several years, and there is no report on the increase of repair rate due to the drop. Some companies focus on how to better control the manufacturing environment, especially reducing the maximum allowable tension from 1000 micro rib to 750 or 500 micro rib.
thermal cycle
In some specific cases, the thermal performance of SnPb materials is better than that of lead-free materials. The following situations should be considered.
Components highly sensitive to solder joint fatigue (such as large on-chip resistance, BGA of ceramic package, leadless ceramic substrate, unfilled chip level package).
The maximum node temperature exceeds 80 ℃ and the dwell time exceeds 4 hours (the dwell time decreases with the temperature rising).
The thermal cycle shall be conducted at least once a day, and the expected service life shall be at least 10 years (the service life decreases with the increase of cycle frequency).
If you are in these situations mentioned above, you need to conduct accelerated life tests based on the existing lead-free solder joint reliability model to determine the risk.
Formation of CAF
Conductive anode wire (CAF) is formed by the migration of copper wire along the glass fiber or resin interface, which will generate internal electrical short circuit between adjacent conductors, which is a serious problem for the design of high-density circuit boards. Higher reflow temperature will cause this problem to occur more easily. Some large HDI board manufacturers cannot meet the CAF requirements of users when using lead-free reflow soldering.
Some materials and processing processes can avoid CAF problems even after multiple reflow soldering. In any case, all these methods will increase the cost, because patented or private technologies will be used. In this way, unless specifically required by customers, many HDI board manufacturers will not use materials that can prevent CAF.
Interface Science (Goleta, CA) has developed a promising mitigation technology by introducing silane, which can maximize the consistency of density and silane shell of glass fiber. If the consistency is good, the glass fiber and resin can be combined more closely, which can reduce the probability of CAF. PCB manufacturers, PCB designers and PCBA manufacturers will explain the reliability analysis of HDI lead-free digital products in long-term use.