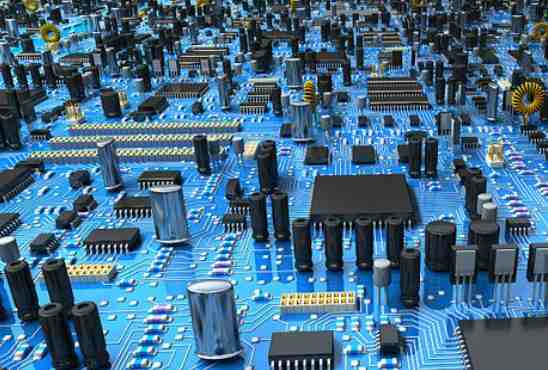
There are many variables that can cause a printed circuit board to fail after the coating process is complete. In general, these failures may be due to the choice of coating material, coating method is not appropriate, or due to the surface treatment work is not done adequately, or there will be some chemical action under the coating completely unrelated to the coating material. A poorly performing coating may lose its insulating properties on the PCB surface when condensation and ionic impurities combine to form a conductive channel between the PCB lines. There is no doubt that condensation will severely test the insulation resistance of the coating. There are many coating products that can withstand this kind of test, so you can avoid these problems by choosing the right materials at the beginning of the design.
If the coating is not fully cured, its protective effect will not be fully realized. When this happens, the coating process is to blame. Correct coating process is a prerequisite for successful coating, as long as the coating process is correct, a series of coating problems can be solved at once. For example, poor coverage, insufficient thickness and sharp edge coverage, many coating materials are difficult to solve these problems, in the prone to these problems in the area of coating is difficult to reach enough thickness, it is difficult to ensure the protective effect of the coating. These problems will be solved by combining material selection with coating technology and process. The IPC specification allows dry film thicknesses between 30 and 130 microns, with thicker coatings achieved by applying multiple times. For example, trying to get a dry film thickness of 130 microns, using solvent-based acrylic materials to achieve a dry film thickness of 130 microns in one go through a selective coating process is a recipe for disaster, with excessive bubbles forming in the coating, film shrinkage, coating delamination, and additional stress on the component. The result of this coating is that the protection of the coating is relatively poor and does not improve the protection of the circuit at an overall level. The coating process should aim at a uniform thickness of 30-50 microns, and focus on achieving perfect coverage for each coating, which is a better way to improve the protection of three anti-paint on electronic circuits.
It is important to get the correct coating thickness when applying three anti - paint; Keep in mind that if the coating is too thick, it may cause solvents to linger in areas where the coating is not fully cured. Similarly, too thick a coating can cause the coating to crack while curing, or even to crack the coating of the coated component itself, either due to temperature changes or mechanical shocks and vibrations. The primary factor that determines the reliability of the coating is the coating process. Often, a material with poor properties is well coated, while another material with good properties is poorly coated, and the results of the two cases may be comparable, or sometimes even better than the former. When applying, try to get enough coverage on sharp edges, not over thick material on all metal surfaces. Of course, some materials are "easier to coat" than others, and keep the coating process as simple as possible; But ultimately the performance of coatings for liquid applications will always depend on how well they are applied.
Large arrays of discrete components also face a huge coating challenge because of the high capillary force involved in coating, with often disastrous results. Because there are areas of the board that do not need to be coated and areas that do need to be coated, at the junction of these two areas, Where the coating is too thick, the coating is prone to stress cracking, film separation and other coating defects. This can eventually lead to premature component failure and should be avoided!
Another cause of coating defects can be unexpected interactions between other process materials used to prepare and manufacture PCBS. Flux residues are a typical example of this type of problem. For example, in a "no-wash" process, some of the materials used in the no-wash process can inhibit the curing of certain types of coatings or cause the insulation of the system to decline, which is more of a problem than any one material alone. The only way to avoid this is to meticulously prepare the PCB before coating or to implement a pre-cleaning system before coating. Otherwise, corrosive residues can cause the PCB's conductive wiring to bridge, which can lead to failure over time. While the coating may delay the failure of the board for many years, it is inevitable that the board will fail at some point.