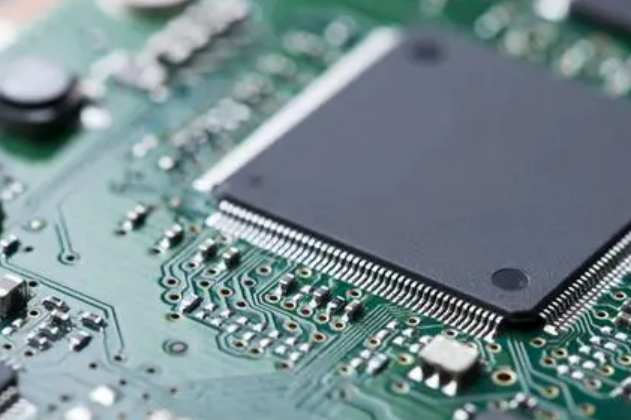
1. Heat dissipation through PCB board itself: at present, PCB board is widely used in copper/epoxy glass cloth substrate or phenolic resin glass cloth substrate, and a small amount of paper-based copper coated plate. Although these substrates have excellent electrical properties and processing properties, but poor heat dissipation, as a heat dissipation way of high heating components, almost can not be expected from the PCB resin conduction heat, but from the surface of the components to the surrounding air heat dissipation. However, as electronic products have entered the era of component miniaturization, high-density installation and high thermal assembly, it is not enough to only rely on the surface of components with very small surface area to dissipate heat. At the same time, due to the large number of surface mounted components such as QFP, BGA, the heat generated by components to PCB board, therefore, the best way to solve the heat dissipation is to improve the heat dissipation capacity of PCB aluminum substrate in direct contact with the heating element, through the PCB board to conduct out or send out.
2. For equipment with free convection air cooling, it is best to arrange integrated circuits (or other devices) by length or by transverse length.
3. Use reasonable wire design to achieve heat dissipation: because the resin in the plate has poor thermal conductivity, and the copper foil line and hole are good conductors of heat, so improving the copper foil residual rate and increasing the heat conduction hole is the main means of heat dissipation.
4. High heating device with radiator, heat conduction plate: when the heat of a few components in PCB is larger (less than 3), can be added on the heating device radiator or heat conduction tube, when the temperature can not fall, can be used with a fan radiator, in order to enhance the heat dissipation effect. When the amount of heating devices is large (more than 3), you can use a large heat sink (plate), which is customized according to the position and height of the heating devices on the PCB board, or in a large flat radiator cut out different positions of the components. The radiator cover is fastened on the component surface as a whole, and contact with each component to dissipate heat. However, due to the low consistency of components during welding, the heat dissipation effect is not good. Soft thermal phase change pads are usually added on the surface of components to improve the heat dissipation effect.
What is the difference between aluminum substrate and FR4 plate?
Aluminum substrate and FR-4 plate main characteristics comparison: aluminum substrate and FR-4 plate heat dissipation (expressed by saturated thermal resistance) contrast: the substrate is aluminum substrate and FR-4 plate equipped with transistor PCB, due to the heat dissipation of the substrate is different, resulting in the working temperature rise of different test data.
1. Performance:
The comparison of conductive lines (copper lines) and fusing currents on different substrate materials is shown in Figure 1. From the comparison of aluminum substrate and FR-4 plate, because of the high heat dissipation of metal substrate, the wire fuse current has been significantly improved, which indicates the high heat dissipation characteristics of aluminum substrate from another Angle. The heat dissipation of aluminum substrate is related to its insulating layer thickness and thermal conductivity. The thinner the insulation, the higher the thermal conductivity (but the lower the voltage resistance) of the aluminum substrate.
2. Machinability:
Aluminum substrate has high mechanical strength and toughness, which is superior to FR-4 plate. For this purpose, large area printed boards can be manufactured on aluminum substrates, and heavy components can be installed on such substrates.
3. Electromagnetic shielding:
In order to ensure the performance of electronic circuits, some components of electronic products need to prevent the radiation and interference of electromagnetic waves. Aluminum substrate can act as a shield plate, play the role of shielding electromagnetic wave.
4. Thermal expansion coefficient:
Due to the general FR-4 there is a problem of thermal expansion, especially the thickness of the plate in the direction of thermal expansion, so that the quality of the metallization hole, the line is affected. The main reason is that there is a difference in the thermal expansion coefficient of the raw material thickness of the plate: the thermal expansion coefficient of copper is 17×106cm/cm•℃, and the FR-4 plate substrate is 110×106cm/cm•℃. The difference between the two is large, which is easy to produce: the difference in the expansion change of the heated substrate, which causes the rupture between the copper line and the metallization hole, and affects the reliability of the product. The thermal expansion coefficient of aluminum substrate is 50×106cm/cm•℃, smaller than the general FR-4 plate, more close to the thermal expansion coefficient of copper foil. This is conducive to ensure the quality of the printed circuit board, reliability.