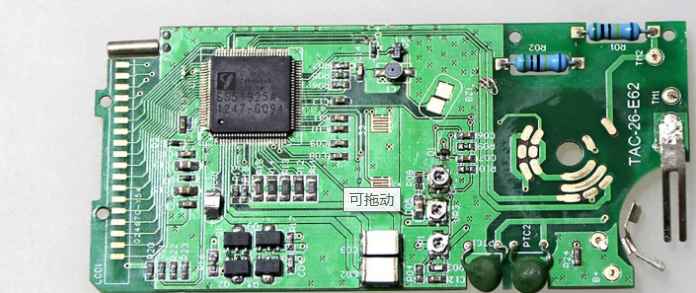
kingford specializes in providing overall PCBA electronic manufacturing services, including upstream electronic component procurement to PCB production and processing, SMT patches, DIP plug-ins, PCBA testing, finished product assembly and other one-stop services. Next, we introduce how to do solder paste printing in PCBA processing. Solder paste printing is very important for PCBA, which directly determines the overall welding effect of PCBA. In the process of PCBA machining, how to print solder paste correctly has become a problem that must be considered by PCBA machining engineers. The printing effect of solder paste includes steel mesh, solder paste, printing process, detection method, etc.
One, the steel mesh must be according to the layout of the electronic components on the PCBA board to expand or reduce the circulation of the steel mesh, in order to determine the content of tin on the solder plate, in order to achieve the best welding effect, to avoid the occurrence of tin connection, tin and so on less, which requires a strict evaluation of the process engineer. In addition, the material of the steel mesh is also very critical, which will affect the tension and reuse life of the steel mesh. In addition, the cleaning and storage environment before feeding the wire mesh is particularly critical. Strict cleaning must be carried out before each production line, and holes must be checked for blockage, the presence of tin residues, etc. Some PCBA manufacturers recommend purchasing a wire mesh tension meter and testing the wire mesh tension before each feed.
Solder paste should be selected from high-end brands, such as Qianju, Vitex, etc., which contains active ingredients such as gold or silver. The solder paste must be strictly kept in the refrigerator at 2 to 10 degrees, and the solder paste must be counted each time. The recovery of solder paste must be strictly controlled within the IPC standards, and the solder paste stirring procedure must be strictly implemented before it can be put online.
At present, manufacturers are using automatic solder paste printing presses, whose equipment can well control the printing force and speed parameters, and has a certain automatic cleaning function. The operator only needs to set parameters strictly according to the regulations. During mass production, it is particularly important to detect blocking and deviation of the steel mesh, especially when certain defects detected by SPI increase after printing, and the machine must be shut down to check the working condition of the steel and the mesh itself.
After the solder paste printing press, it is particularly important to install SPI solder paste detector, which can effectively detect many defects in the solder paste printing process, such as tin deficiency, tin connection, notch, wire drawing, deviation, etc. To maximize the overall welding PPM. It is no secret to manage the printing effect of solder paste. It requires managers to carefully implement each management method in the PCBA process. The closed-loop mechanism is designed to detect and detect defects.
How to do electrostatic protection in PCBA processing
In the process of PCBA, electrostatic protection is very important. Static electricity can damage electronic components invisibly, thus affecting the quality of products. In the eyes of PCBA processing manufacturers, the quality of products largely depends on the electrostatic protection of the production site. Next, it is necessary to do a good job of electrostatic protection in PCBA processing, as well as the precautions and key points of electrostatic protection. Why should we do electrostatic protection in PCBA processing? PCBA board has many precision electronic components, many components are more sensitive to voltage. A shock above the rated voltage will damage these components. However, it is difficult to gradually troubleshoot PCBA boards damaged by static electricity during functional detection. What is more fatal is that some PCBA boards function normally during the test, but when the finished products are used in the hands of customers, there will be occasional defects, which brings great hidden trouble to the after-sales service and affects the company's brand and goodwill. Therefore, great attention must be paid to ESD protection during PCBA processing.
Electrostatic hazard faced by PCBA processing
1. According to timeliness, damage is divided into two types, one is sudden damage. This kind of damage can usually be detected during quality inspection in the production process. Usually the only loss to the business is the cost of rework and repair. 2. Potential damage generally refers to the basic use function of components still exists, but the service life is sharply reduced. It is usually discovered only by later users. This kind of damage can cause a lot of unexpected damage.
Esd precautions for PCBA processing
1. Operators must wear electrostatic work clothes, do not attach or wear any metal products on the work clothes, do not take off the work clothes in the operation of electrostatic sensitive products, work clothes buttons must be all buttoned, try not to make it in the state of stripping. 2. Wear an ESD wrist strap that is in good contact with your skin and grounded properly. Plastic boxes, erasers, cardboard, and glass are not allowed to be stacked on the ESD workbench. 3. All components must be operated on the ESD workbench. Components entering the ESD work area must be treated according to the ESD requirements. 4. Esd sensors that fall on the floor during operation must be tested and reconfirmed before they can be used. Items that cannot be directly tested must be confirmed to be qualified before being released. 5. When handling the sensitive element, avoid touching its lead and wiring piece. Avoid electrostatic sensitive components when holding the mainboard. Some components to clean, should use anti-static brush, do not use plastic brush. 6. When entering the workshop, you must wear anti-static caps to prevent your hair from inadvertently contacting electrostatic sensitive components. 7. During manual welding, anti-static low-voltage constant temperature electric soldering iron should be used. It is forbidden to reuse device packaging pipe to pack components.
Key points of electrostatic protection in PCBA processing
1. To ensure that the temperature and humidity of the workshop within the standard range, 22-28 degrees Celsius, humidity 40%-70%; 2. All employees must release static electricity when entering and leaving the workshop; 3. Dress as required, wear electrostatic caps, electrostatic clothes and electrostatic shoes; 4. At all stations where you need to touch the PCBA board, you must wear a rope electrostatic ring and connect the rope electrostatic ring to the electrostatic alarm. 5. The static wire is separated from the ground wire of the equipment to prevent the leakage of electricity of the equipment, resulting in damage to the PCBA board; 6. All static frames and shelves of turnover cars must be connected to electrostatic ground wires; 7. Perform ESD spot check in strict accordance with ISO quality management requirements. Static electricity can not be seen and touched in the production process, often inadvertently produce fatal hidden dangers to the PCBA circuit board, PCBA troubleshooting cost is very high. Therefore, each factory manager must pay strict attention to ESD static management, so that the PCBA processing process is complete quality control.