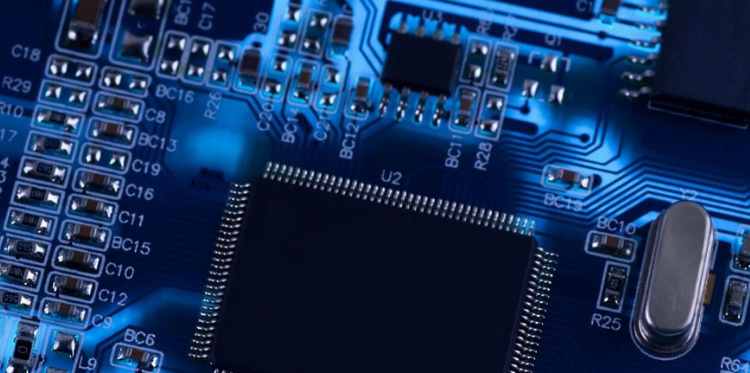
The performance of PCBS can be affected by many external or environmental factors, such as moisture, extreme temperatures, salt spray and chemicals. A protective coating is a polymer film applied to the PCB surface to protect the PCB board and its components from corrosion and environmental contamination.
Protective coatings prevent corrosion of conductors, solder joints and wiring by protecting against contaminants and environmental factors. In addition, it provides insulation, thus reducing the impact of thermal and mechanical stress on the components.
Protective coatings are an important component of printed circuit boards, typically ranging in thickness from 3 to 8 mils (0.075 to 0.2 mm), and are widely used in industries such as aerospace, automotive, military, Marine, lighting, consumer electronics and industrial.
Type of PCB protective coating
Protective coatings can be classified into five types based on their chemical composition: acrylic, epoxy, polyurethane, silicone and p-xylene. The choice of specific coatings is based on the application and electronic requirements of the PCB. Select appropriate materials to effectively protect PCB.
Acrylic protective coating:
Acrylic resin (AR) is a preformed acrylic polymer that dissolves in a solvent and is used to coat PCB surfaces. Acrylic protective coatings can be hand-brushed, sprayed or dipped into acrylic paint. This is the most common protective coating for PCBS.
What types of protective coatings do PCB boards have?
Polyurethane protective coating:
Polyurethane (UR) coatings provide excellent protection against the effects of chemicals, moisture and wear. Polyurethane (UR) protective coatings are easy to apply but difficult to remove. It is not recommended to repair directly by means of heat or soldering iron, as it can release the toxic gas isocyanate.
Epoxy resin (ER type) :
Epoxy resins have excellent conformal properties in harsh environments. It is easy to use, but can damage the circuit when removed. Epoxy resins are usually a two-component thermosetting mixture. Single-part compounds are cured by heat or ultraviolet irradiation.
Silicone (SR type) :
Silicone (SR type) protective coatings are used in high temperature environments. The paint is easy to apply, has low toxicity, and is resistant to wear and moisture. Silicone coatings are one-component compounds.
Paraxylene:
The p-xylene coating was applied to the PCB by chemical vapor deposition process. When heated, p-xylene turns into a gas. After the cooling process, it is placed in a chamber, where it is polymerized and turned into a film. The film is then applied to the surface of the PCB.
Guide for selection of PCB protective coatings
The type of conformal coating depends on the thickness of the desired coating, the area to be covered, and the degree of adhesion of the coating to the board and its components.
How to apply conformal coating to PCB?
● Paint by hand with a brush
● Use aerosol for hand application
● Manual spraying with atomizing spray gun
Keep hot forming and can be used for smaller and smaller PCBS
When you think printed circuit boards (PCBS) can't shrink, they continue to shrink, especially in today's era of mushrooming Internet of Things devices. See Figure 1 for an example of denser and smaller PCBS. The smaller the PCB, the greater the challenge of creating the correct thermal curve.
Having a similar temperature curve is particularly critical for smaller boards, which can only withstand a lower duration peak temperature cycle than PCBS with higher reflux.
Develop a heat dissipation curve based on the size of the PCB and the number of key components to be installed on the board, as well as other factors to be considered, such as the number of layers and thickness of the board. Both tin lead and unlead profiles are different because unlead profiles require a higher peak temperature than tin-lead profiles.
For more details, check out our article on heat dissipation curves for small PCBS.
In the meantime, here are some tips and tips to help you better understand the heat dissipation map of small PCBS.
● The most important rule is that the heat distribution is not equal, and each plate side needs a unique distribution.
● The thermocouple needs to be placed on the board in a number of different and correct ways. Contact the process engineer.
● When the board is in array or panel form, the thermocouple is placed in the area where the key components are located.
● Thermocouples provide actual temperature readings from specific areas placed on the PCB.
● Thermocouples collect data to determine if certain areas are overheating and/or certain areas are not getting enough heat.
● Other factors to be aware of are the packaging material of the component as well as the material of the PCB, such as polyimide, FR4 or Rogers, as they have different Tg or glass transition temperatures.
It should be noted that some sensitive components cannot withstand high temperatures and may fail during testing. They are considered sensitive based on their sensitivity to heat. For example, certain devices (such as micro BGA) cannot be exposed to temperatures above 230°C. Oems often provide instructions on component reflow soldering guidelines to help process engineers set up their reflow profile.