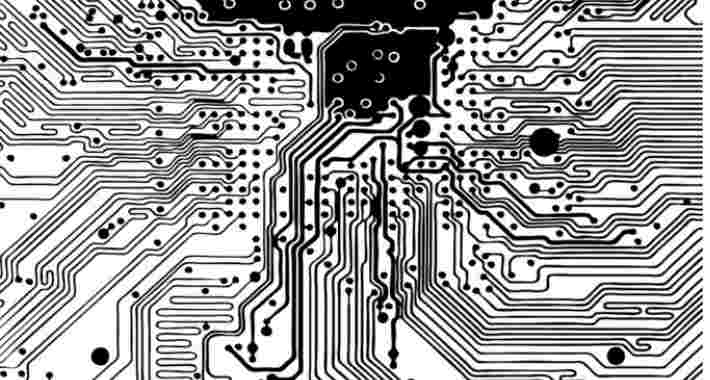
By having your printed circuit board components handled by an experienced PCB component manufacturer, it can help your company save a lot of time and resources that could have been spent creating this technology on its own. Plus, since these outstanding PCB assembly companies will know how to optimize the performance of these components, it can help you get a higher quality PCB.
One way they can help achieve this is by increasing the production of printed circuit board components. This is how they completed the process of increasing PCB production.
Use solder paste wedges
As anyone even vaguely familiar with PCB assembly will probably know, one of the most common ways to apply solder paste to a PCB is to paint it as a rectangle. This is because the pad will likely be rectangular, which means that the average PCB assembler will consider applying the paste in this shape as optimal.
However, this is not the case, and using a rectangular solder paste may actually limit the performance of the PCB, as may applying too much or too little solder paste.
Why do solder wedges increase yield
For paste shapes used on PCBS, you need to use a shape that allows you to use as little paste as possible without getting to the point where it starts to negatively affect PCB performance.
By using a rectangular paste shape, the possibility of bridging is greatly increased due to excessive paste on the pad. However, when someone decides to switch to a wedge-shaped solder paste, the amount of solder paste decreases, meaning that the PCB bridge wire is very unlikely.
The use of wedge paste shapes also has the benefit of increasing the amount of distance between shapes, which contributes greatly to the production of PCBS. Together, these reasons make solder paste wedges the most effective tool for improving the yield of PCB components.
Common core and copper thickness
The core thicknesses most commonly used to construct layers 0.062 inches thick are 0.005 inches, 0.008 inches, 0.014 inches, 0.021 inches, 0.028 inches, and 0.039 inches. An inventory of 0.047 "is also common, as it is sometimes used to build 2 layers of board. The other core that is always going to be stored is 0.059 inches, because it is used to produce 2 layers 0.062 inches thick, but only for thicker layers, such as 0.093 inches. For this position, we limit the scope to apply to core designs with final nominal thickness of 0.062 inches.
Copper thickness ranges from half an ounce to 3 to 4 ounces, depending on the particular manufacturer's product mix, but most stocks are likely to be 2 ounces or less. Keep this in mind and remember that almost all stock will use the same weight of copper on both sides of the core. Try to avoid design requirements that require different copper on each side of the PCB, as often this requires special purchase, may require expedited fees (expedited delivery), and sometimes does not even meet the minimum order quantity of the distributor.
For example, if you want to use 1oz of copper on an aircraft and plan to use an H oz signal, consider making the aircraft at H oz or increasing the signal to 1oz so that the magnetic core is used like copper with weight on both sides. Of course, you can only do this if you can still meet the electrical requirements of the design and have enough XY areas to accommodate widened trace/space design rules to meet the 1oz minimum at the signal layer. If you can meet these conditions, it is best to use them like copper weights. Otherwise, you may need to consider a few extra days of delivery time.
Assuming you have selected the appropriate core thickness and available copper weight, use various combinations of prepregs to establish the remaining dielectric locations until the desired total thickness requirements are met. For designs that do not require impedance control, you can leave the choice of prepreg to the manufacturer. They will use their preferred "standard" version. On the other hand, if you do have impedance requirements, state them in your documentation so that the manufacturer can adjust the amount of prepreg between cores to meet specified values.
Whether impedance control is required or not, it is not recommended that you attempt to mark the type and thickness of prepreg at each location in the documentation unless you are proficient in doing so. Often, such detailed stacks end up needing adjustments, so they can cause delays. Instead, your stack diagram shows the core thickness of the inner layer pair and notes "prepreg billet location required based on impedance and overall thickness requirements." This allows the manufacturer to create the ideal layering to match your design.