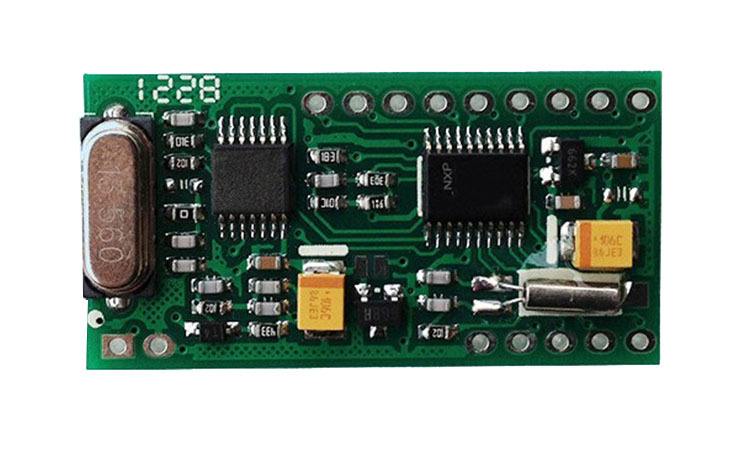
To solve these problems, we through a long time of research and discussion, finally research and manufacture a cheap, simple use of small scale quickly printed circuit board manufacturing system. The system consists of a rapid microcomputer digital control heat transfer platemaking machine and a rapid etching machine. The inspiration for the heat transfer plate making machine was in the research on laser printers, and our research positions found that the "toner" of laser printers, which we know well, is not the toner of inorganic substances, but the black molecular compound plastic microparticles containing magnetic substances. It is attracted by the laser printer drum static electricity, in the toner cartridge lists high precision graphics and documents, after eliminating static electricity, transfer to printing paper, and by high temperature melting hot pressing fixed, forming a laser printer work. Our research positions in this discovery revealed, research and manufacture of thermal transfer paper with high temperature resistance and non-adhesion special properties, rapid microcomputer digital control heat transfer platemaking machine and rapid corrosion machine. Using this system, printed circuit boards can be produced quickly and in small batches. Compared with the traditional photographic plate manufacturing process in the past, this system has the following significant advantages:
1. The version of high precision: can achieve the accuracy of laser printer accuracy, in addition to the manufacture of precise and detailed circuit graphics, but also can produce a high accuracy of the image. Using it can not only make a precise PCB circuit board, even can make a fine metal signs, metal painting and so on.
2. Low cost of plate making: the plate making cost of manufacturing a circuit board is only equivalent to the cost of a heat transfer paper.
3. Fast plate making speed: rapid heat transfer platemaking machine can be laser printer printed on the heat transfer paper printed circuit graphic quickly transferred to the circuit board, the formation of corrosion resistance layer, manufacturing a 200mm×300mm printed circuit board, only need 10 ~ 20 minutes. Very suitable for factories, research institutes, colleges, electronic stores to quickly manufacture circuit board template.
4. Multi-use: can be made at the same time a double panel, a single panel with characters, can also be made twice with characters double panel.
5 semi-automation, the operation is very simple: rapid heat transfer type platemaking machine, think appropriate and use 89c2051 as the main control chip. Plate-making machine to cots temperature survey and setting; Circuit boards in, out; When the power supply is turned on, and when the motor is turned off to prevent the cots from overtemperature, the motor delay stop function is fully semi-automatic choke with touch switch.
6. High cost performance of facilities: This kind of heat transfer rapid platemaking system replaces the traditional printed board manufacturing process. The facilities are cheap and cost-effective. The operation and office principle of the plate-making machine will be made of computer printed circuit board graphics, printed in the intense light printer through special disposal of special thermal transfer paper, and then transfer paper covered on the copper plate into the plate-making machine.
The office principle of the plate-making machine is mainly considered appropriate and the principle of heat transfer is used. Its structure is similar to that of the laser printer. There are two groups of four specially made high temperature resistant silicone cylindrical rollers to form the transmission structure. Two infrared quartz heating tubes are used to heat a group of two silicone cylindrical rollers to 180.5℃ on average. At the same time, each group of two silicone cylindrical rollers is two pressure rollers, whose appearance can reach 300℃. The two groups of rubber rollers are driven by synchronous motor through the transmission system and rotate at a constant speed of two revolutions per minute.
When the heat transfer paper and the copper coated plate pass through the crack between the silicone cylinder roller with high temperature and high pressure, the absorbed toner on the heat transfer paper will melt. Because the heat transfer paper is specially disposed of, several layers of special material coating are covered on its surface by polymer technology, so that the heat transfer paper has the special property of high temperature resistance and non-adhesion. When the temperature reaches 180.5℃, the adsorption capacity of the ablation toner of the thermal transfer paper decreases rapidly. Under the effect of pressure, the ablation toner is absolutely adsorbed on the copper coating. After the copper coating is cooled, the tight printed graph is formed, and the whole heat transfer process is completed. The same principle, if you need to transfer the component layout on the other side of the printed circuit board, it can also be implemented at the same time, so that the printed board can reach a more professional level.
Here the requirements are explained clearly: the whole heat transfer process is particularly high temperature requirements, temperature control appears to be very tight. For example, the optimal point of toner ablation temperature is generally 180.5℃. When the temperature is too high, the excessive ablation toner will stretch around the original lines, resulting in blurred graphics and poor precision. In serious cases, the paper will be scorched. When the temperature is too low or the temperature is even, the transfer effect will be shown to be poor, or even can not be transferred. In practice, because of the temperature, humidity, the thickness of paper and circuit board and other factors on the transfer effect has a certain impact, because the temperature of the transfer effect is very close. Therefore, the temperature control sensor of the heat transfer platemaking machine is considered appropriate and the imported pt-1000 thin film platinum resistance is used, so that the temperature control precision can reach 0.1℃, satisfying the higher requirements of platemaking temperature.
When the graphic is transferred to the copper coating, that is to say, the printer's toner forms a graphical care layer on the copper coating surface. Because the toner of laser printer is made of polymer material including natural resin, which has satisfactory corrosion resistance to corrosion solution (fecl3 solution), it can form a fine printed circuit board after corrosion by fecl3 solution. In order to make the corrosion circuit board more agile and convenient, but also need a corrosion machine to implement rapid corrosion on the circuit board, in order to save time, reduce the cost of fecl3 solution, growth rate. Rapid corrosion machine will quickly heat fecl3 solution to more than 60℃, and then anti-corrosion small-scale circulating submerged pump fecl3 solution through the special showerhead spray evenly scattered to the printed board.
Generally, under the condition of heating to 80℃, corrosion with fecl3 solution with higher liquid concentration can be finished in 5 ~ 6 minutes. Due to the rapid corrosion process, side erosion can be reduced, so that the PCB precision is more perfect and reliable. After heating, the oxygenation recovery response of fecl3 solution is accelerated, so the copper on the surface of the copper plate is accelerated into cu2+ oxygen; At the same time, the impact of the water takes away the cu2+ deposited on the surface of the copper plate and nearby, so that the chemical reaction is faster and more fully implemented. This machine is especially suitable for the use of the flat surface or the surface of the object of the larger size of the printing plate manufacturing.
The whole corrosion process is carried out under the condition of semi-closed affairs, which has the advantages of cleanliness and hygiene and loss of corrosion liquid evaporation, because it is very suitable for the small batch manufacturing of printed circuit boards in laboratories, research institutes and factories. Once the printed circuit board is etched, the board is drilled with a special drill bit. This drill bit has a cylinder attached to it, which simultaneously grinds away the toner near the hole at high speed, creating a very neat pad. The other toner covering the copper foil forms a satisfactory solder resistance layer.