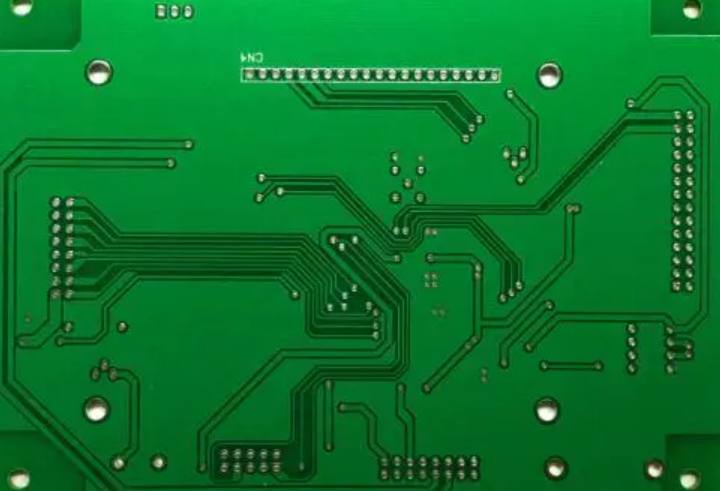
How can we prevent the bending and warping of the plate after the back welding furnace?
1.The effect of reducing temperature on the stress of plate
Since "temperature" is the main source of plate stress, as long as reducing the temperature of the backwelding furnace or slow down the heating and cooling speed of the plate in the backwelding furnace, the bending and warping of the plate can be greatly reduced. But there may be other side effects.
2.High Tg plate is used
Tg is the glass conversion temperature, that is, the temperature at which the material changes from glass state to rubber state. The lower the Tg value is, the faster the board will become soft after entering the backwelding furnace, and the longer it will take to become soft rubber state, the more serious the deformation of the board will be. The plate with higher Tg can increase its ability to withstand stress and deformation, but the price of the material is relatively high.
3.Increase the thickness of the circuit board
Many electronic products in order to achieve the purpose of thinner, the thickness of the board has been left 1.0mm, 0.8mm, and even 0.6mm thickness, such a thickness to keep the board in the welding furnace without deformation, really a bit of a force, it is suggested that if there is no light and thin requirements, the board can use the best thickness of 1.6mm, Can greatly reduce the risk of bending and deformation of the plate.
4.Reduce the size of the circuit board and reduce the number of pieces
Since most backwelding furnaces use chains to drive the circuit board forward, the larger the size of the circuit board will sag and deform in the backwelding furnace because of its own weight, so try to put the long side of the circuit board as the board side on the chain of the backwelding furnace, you can reduce the weight of the circuit board caused by the sag deformation, reduce the number of plates is also based on this reason, That is to say, when the furnace, as far as possible to use the narrow side of the vertical direction of the furnace, can achieve the lowest depression deformation.
5.Used stove tray fixtures
If the above methods are difficult to achieve, reflow carrier/template is used to reduce the deformation. The reason why the plate bending and warped can be reduced by the reflow carrier/template is that the tray is expected to hold the circuit board no matter it is hot expansion or cold contraction. After the temperature of the circuit board is lower than Tg value and begins to harden again, It can also maintain the size of the garden.
If a single layer of tray can not reduce the deformation of the circuit board, it is necessary to add a layer of cover, the circuit board with two layers of tray clip up, so that you can greatly reduce the circuit board over the welding furnace deformation problem. But the trays are expensive, and you have to add labor to place and retrieve them.
6.Use real connection and stamp hole instead of V-Cut sub-board
Since V-cuts can damage the structural strength of the board, try not to use V-Cut subboards, or reduce the depth of the V-Cut.
Optimization in PCB production engineering
Influence of different materials on plate deformation
The excessive deformation and defect rates of plates of different materials were counted, and the results were shown in Table 1.
As can be seen from the table, the deformation defect rate of low-TG materials is higher than that of high-TG materials. The high-TG materials listed in the table above are all package-shaped materials, and the CTE is smaller than that of low-TG materials. Meanwhile, in the processing process after pressing, the baking temperature is up to 150℃, so the influence on low-TG materials is definitely greater than that of medium-high Tg materials.
1.Engineering design research
Engineering design should avoid structural asymmetry, material asymmetry and graphic asymmetry as far as possible to reduce deformation. Meanwhile, during the research process, it is also found that the core plate directly pressed structure is easier to deform than the copper foil pressed structure. Table 2 shows the test results of the two kinds of structural plates.
It can be seen from Table 2 that there are obvious differences in the defect rates of unqualified deformation of the two structures. It can be understood that the core plate pressing structure is composed of three core plates, and the expansion and contraction and stress changes between different core plates are more complicated and difficult to eliminate.
In engineering design, the form of panel frame also has a great influence on the deformation. Generally, PCB factories will have continuous large copper frame and non-continuous copper point or copper block frame, which are also different.
Table 3 shows the comparative test results of the two frame design panels. The reason why the deformation of the two forms of the frame is different is that the continuous copper frame has high strength, and the rigidity is relatively large in the process of pressing and assembling the plate, so that the residual stress in the plate is not easy to release, which is concentrated in the release after the shape processing, resulting in more serious deformation. While the non-continuous copper point frame gradually releases the stress in the process of pressing and subsequent processing, and the veneer deformation is small after the shape.
The above are some possible influencing factors involved in engineering design, such as flexible use in design. It can reduce the deformation effect brought by the design.