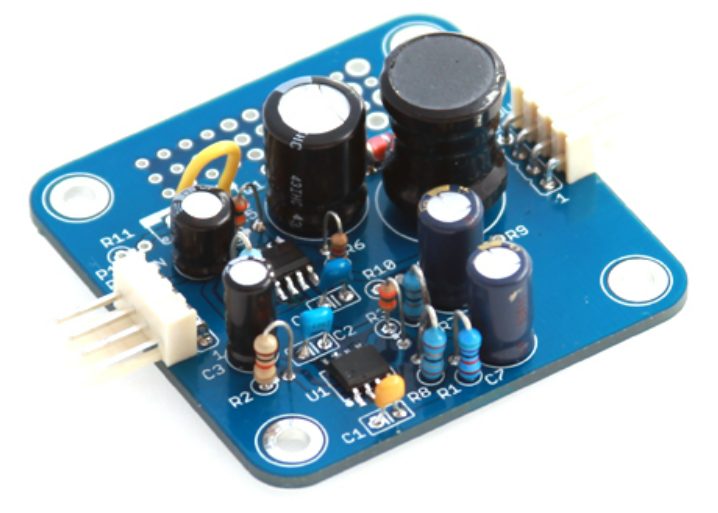
With the development of electronic information technology, more and more fields use multi-layer PCB board. Traditionally, we define PCB boards with more than 4 layers as "multilayer PCB boards", and more than 10 layers as "high multilayer PCB boards". The ability to produce high layer PCB board is an important index to measure the strength of a PCB board manufacturer. Can produce more than 20 layers of high multilayer board, is the technical strength of the top of the PCB enterprise. It is said that the production of multi-layer PCB board is expensive because it is difficult to make, but many customers have been confused about the problem of "why it is so difficult to make multi-layer PCB board", so that they think that the manufacturer is looking for a reason to charge arbitrarily. Today, let the experienced PCB engineer engineers for you to explain: why the production of multilayer PCB board is so difficult?
One, the main production difficulties
Compared with conventional circuit boards, high-rise circuit boards are thicker, more layers, more dense lines and holes, larger unit size, thinner medium layer, etc., and more stringent requirements for inner space, interlayer alignment, impedance control and reliability.
1. Difficulty in alignment degree between layers
Due to the number of high-rise board layers, the customer design end of PCB layer alignment requirements are more and more strict, usually the inter-layer alignment tolerance control ±75μm, considering the large size design of high-rise board units, graphic transfer workshop ambient temperature and humidity, as well as different core board layer growth and shrinkage inconsistency caused by dislocation superposition, inter-layer positioning mode and other factors. It makes it more difficult to control the alignment degree between the layers of the high floor.
2, the inner line production difficulties
The high floor board uses high TG, high speed, high frequency, thick copper, thin dielectric layer and other special materials, which puts forward high requirements for the inner line fabrication and graphic size control. Line width line distance is small, open short circuit increase, micro short increase, low qualified rate; There are more signal layers in the fine line, and the probability of missing AOI in the inner layer increases. Inner core plate thickness is thin, easy to fold resulting in poor exposure, etching machine is easy to roll plate; The cost of scrap in the finished product is relatively high.
3, pressing production difficulties
The superposition of multiple inner core plates and semi-cured sheets is easy to produce defects such as slide plate, delamination, resin cavity and bubble residue during pressing production. In the design of laminated structure, it is necessary to fully consider the heat resistance, voltage resistance, filling amount and medium thickness of the material, and set a reasonable high layer plate pressing program.
4, drilling production difficulties
Special plates of high TG, high speed, high frequency and thick copper are used to increase the roughness of drilling, burr of drilling and the difficulty of removing drilling dirt. The number of layers, the cumulative total copper thickness and plate thickness, drilling easy to break the knife; CAF failure caused by dense BGA and narrow pore wall spacing; The thickness of the plate is easy to lead to the problem of oblique drilling.
Tow. Control of key production processes
1. Material selection
It requires low dielectric constant and dielectric loss ratio of electronic circuit materials, as well as low CTE, low water absorption and better performance copper clad plate materials to meet the processing and reliability requirements of high-rise board.
2, laminated structure design
The main factors considered in the design of laminated structure are the heat resistance, voltage resistance, filling amount and dielectric layer thickness of the material, which should follow the following main principles:
(1) Semi-cured sheet and core plate manufacturers must be consistent. In order to ensure PCB reliability, 1080 or 106 semi-cured sheets shall be avoided for all layers (except for special requirements of the customer). If the customer has no requirement of medium thickness, the thickness of medium between each layer shall be guaranteed to be ≥0.09mm according to IPC-A-600G.
(2) When the customer requires high TG plate, the core plate and semi-cured plate shall use the corresponding high TG material.
(3) Inner substrate 3OZ or above, use high resin content of the semi-cured sheet, but try to avoid the use of all 106 high-glue semi-cured sheet structure design.
(4) If the customer does not have special requirements, the dielectric layer thickness tolerance between layers is generally controlled by +/-10%. For impedance plates, the dielectric thickness tolerance is controlled by IPC-4101 C/M class tolerance. If the impedance influence factor is related to the substrate thickness, the plate tolerance must also be controlled by IPC-4101 C/M class tolerance.
3, interlayer alignment degree control
The precision of inner core board size compensation and the control of production size requires accurate compensation of each layer graphic size of high-rise board through the data and historical data experience collected during production for a certain period of time, so as to ensure the consistency of each layer core board growth and shrinkage.
4. Inner line process
Since the resolution capacity of the traditional exposure machine is about 50μm, the laser direct imaging machine (LDI) can be introduced for the production of high-rise plate to improve the graphic resolution capacity to about 20μm. The alignment accuracy of conventional exposure machine is ±25μm, and the alignment accuracy of interlayer is greater than 50μm. Using high precision alignment exposure machine, the alignment accuracy of graphics can be improved to about 15μm, and the interlayer alignment accuracy can be controlled within 30μm.
5. Pressing process
At present, interlayer positioning methods before pressing mainly include: four-slot positioning (Pin LAM), hot melt, rivet, hot melt and rivet combination. Different product structures adopt different positioning methods. For the high level plate using four groove positioning mode, or the use of fusion + riveting production, OPE punching machine out of the positioning hole, punching accuracy control in ±25μm.
According to the laminated structure of the high-rise board and the materials used, study the appropriate pressing procedure, set the optimal heating rate and curve, properly reduce the heating rate of the laminated board, prolong the high temperature curing time, so that the resin fully flow and cure, avoid the problems of sliding plate and dislocation between layers during the pressing process.
6. Drilling process
Due to the superposition of each layer, the plate and copper layer are too thick, which causes serious wear to the drill bit and is easy to break the drill tool. The number of holes, falling speed and rotating speed should be adjusted appropriately. Accurately measure the expansion and contraction of the plate to provide accurate coefficient; The number of layers is more than 14 layers, the aperture is less than 0.2mm or the distance from the hole to the line is less than 0.175mm, and the drilling machine with the accuracy of the hole position is less than 0.025mm is used for production. The diameter above φ4.0mm is drilled by steps, the thickness to diameter ratio is 12:1 is drilled by steps, positive and negative drilling method; Control the drilling edge and hole thickness. Adopt new drilling tool or grind 1 drilling tool to drill the upper board as far as possible, and control the hole diameter within 25um.
Iii. Reliability test
The high-rise board is thicker, heavier and larger than the conventional multilayer board. The corresponding heat capacity is also larger. When welding, more heat is needed and the welding high temperature time is longer. At 217℃(solder melting point), 50 seconds to 90 seconds, and the high floor cooling rate is relatively slow, so the over-reflow test time is extended.
The above is the answer of "Why is it so difficult to make multi-layer PCB board" detailed by the experienced PCB engineer for you. Through the above sharing, I believe you must have a more profound understanding of the production of multi-layer PCB board. At the same time, you also understand why the production price of multi-layer PCB board is so expensive! Indeed, the production process of PCB board is complicated, and the production of multi-layer PCB board is even more difficult. "You get what you pay for" is the truth. I hope the above sharing can help you.