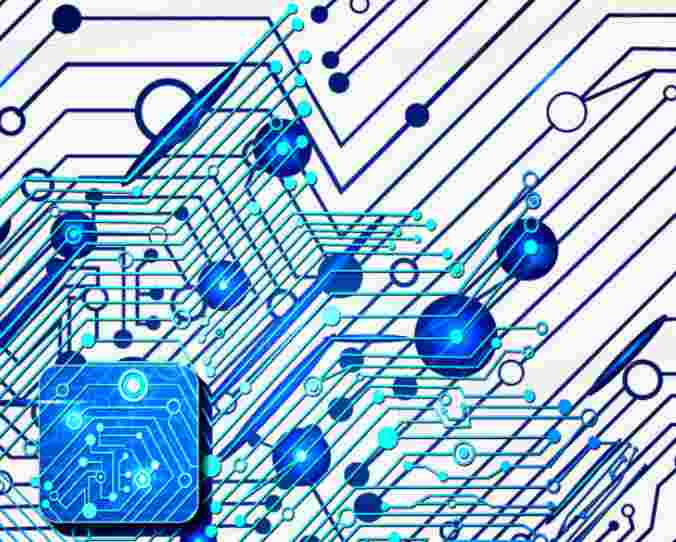
Maybe we will wonder, the substrate of the circuit board only has copper foil on both sides, and the insulation layer in the middle, so they do not need to conduct between the two sides of the circuit board or multiple lines? How can the two sides be joined together so that the current can flow smoothly?
Please see the circuit board manufacturer for you to analyze this magic process - copper (PTH).
Shortened from Eletcroless Plating Copper, also known as Plated Through hole or PTH, copper plating is a self-catalyzed REDOX reaction. The PTH process is performed after two or more layers are drilled.
The role of PTH: A thin layer of chemical copper is deposited chemically on the non-conductive hole wall substrate which has been drilled to serve as the base for copper plating later.
PTH process decomposition: basic oil removal → second or third countercurrent rinsing → coarsing (microetching)→ second countercurrent rinsing → preleaching → activation → second countercurrent rinsing → gelation → second countercurrent rinsing → copper sedimentation → second countercurrent rinsing → acid leaching
PTH detailed process explanation:
1. Alkaline oil removal: remove the surface oil, fingerprints, oxides, dust in the hole; The pore wall is adjusted from negative charge to positive charge so as to facilitate the adsorption of colloidal palladium in the latter process. Cleaning after oil removal shall be carried out in strict accordance with the requirements of the guidelines, and the copper backlight test shall be used for detection.
2. Micro corrosion: remove the oxide of the board surface, roughening the board surface, to ensure that there is a good bonding force between the subsequent copper deposition layer and the substrate bottom copper; The new copper surface has strong activity and can adsorb colloid palladium very well.
3. Prepreg: It is mainly used to protect palladium tank from contamination of pretreatment tank liquid and prolong the service life of palladium tank. The main components are consistent with palladium tank except palladium chloride, which can effectively wet the pore wall and facilitate subsequent activation liquid to enter the pore in time for sufficient and effective activation.
4. Activation: After adjusting the polarity of alkaline deoiling pretreatment, the positively charged pore wall can effectively adsorb enough colloid palladium particles with negative charge to ensure the evenness, continuity and density of subsequent copper deposition; Therefore, oil removal and activation are very important to the quality of subsequent copper deposition. Control points: set time; Standard stannous ion and chloride ion concentration; Specific gravity, acidity and temperature are also important and should be strictly controlled according to the working instructions.
5. Degumming: Removing stannous ions wrapped around colloidal palladium particles, exposing palladium nuclei in colloidal palladium particles, so as to directly and effectively catalyze the start of chemical copper precipitation reaction. Experience shows that fluoroborate as a degumming agent is a better choice.
6. Copper sedimentation: The self-catalytic reaction of chemical copper sedimentation is induced by the activation of palladium nuclei, and the newly formed chemical copper and reaction byproducts can be used as reaction catalysts to catalyze the reaction, so that the copper sedimentation reaction can continue. After this step, a layer of chemical copper can be deposited on the surface of the plate or the wall of the hole. During the process, the tank should keep the normal air stirring, in order to convert more soluble bivalent copper.
The quality of the copper sedimentation process is directly related to the quality of the production circuit board, which is the main source of the process of imperforation and bad opening and short circuit, and it is not convenient for visual inspection. The post-process can only be screened probabilistic through destructive experiments, and it is impossible to effectively analyze and monitor a single PCB board. Therefore, once the problem occurs, it must be a batch problem, even if the test cannot be finished. The final product causes great quality risks and can only be scrapped in batches. Therefore, the parameters in the working instructions should be strictly operated.
7. Comparison of electrical measurement:
The sunken gold plate can be measured directly before and after production and shipment, the operation technology is simple, not affected by other conditions; The surface layer of OSP plate is an organic weldable film, and the organic weldable film is a non-conductive film, so it is impossible to measure directly. It is necessary to measure before OSP, but after OSP, it is easy to cause excessive corrosion and worry, resulting in poor welding. The stability of the surface of the silver plate is general, and the requirements of the external environment are harsh.
8. Comparison of process difficulty and cost:
Gold sinking process card process is difficult, high equipment requirements, strict environmental requirements, and because of the use of a large number of gold element cost in the lead-free process card is the highest; The process of the silver board card is slightly less difficult, the water quality and environmental requirements are quite strict, the cost is slightly lower than the gold plate; OSP board is the most difficult process, so the cost is the lowest.
Keyou circuit specialized in the production of high precision double-sided/multilayer circuit board, thermoelectric separation single-sided/double-sided copper substrate, foldable metal substrate, copper substrate, industrial circuit board, medical circuit board, security PCB board, communication PCB board, automotive circuit board, instrument circuit board, military circuit board.