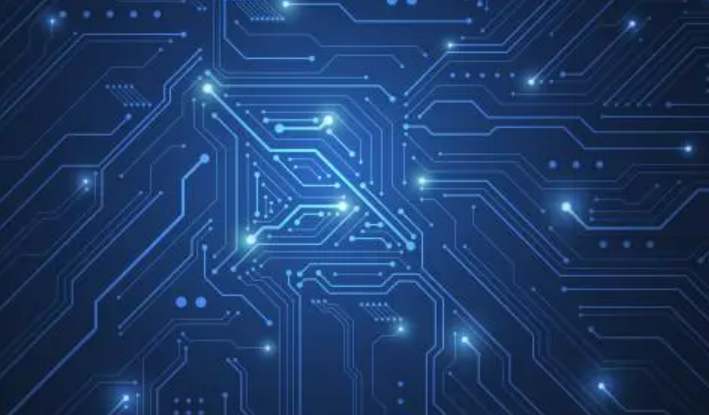
In the quality management work, a lot of managers and the so-called quality experts will fall into such a mistake: a bunch of people sitting in the conference room, together looking at the computer, with such and such quality tools, in the face of a string of numbers to analyze the bad, develop improvement measures, also openly called "brainstorming"; On the other hand, the site is completely liberal, the process is not implemented, the equipment is operated with disease, and defective products can be seen everywhere. People always think that the term quality is how esoteric, is six Sig code, TPM and other high-end knowledge, but ignore the field management, ignore the most basic production activities of the people and equipment.
I have seen such a story, a top pharmaceutical company is often troubled by a simple but difficult problem. They often make mistakes in the canning of pills, mixing empty bottles with full ones and making it impossible to distinguish them from each other, and having to unpack boxes in order to find an empty bottle. After years of research and a lot of investment, they finally installed an X-ray emitter on the assembly line and fed the signal back to the computer, which used a series of advanced principles to detect empty bottles without medicine. They even celebrate solving a world problem. And a county-level pharmaceutical enterprise, not like large enterprises as capital investment, but by the on-site staff thought of a good way, put an electric fan next to the assembly line, no medicine bottles will naturally be blown down, so that can solve the same problem.
Most of the time, on-site problems are not so complicated, and the operators at the front line are the most familiar with the production status and equipment status every day, so the managers can communicate with them more on site to understand the situation, which may solve the production problems more effectively and directly. Every operating staff is willing to work honestly, but faced with a lot of they can not solve, and no one to help them solve, will let operators to the scene of the abnormal indifference. The most important thing for managers is to go to the site to understand the current situation, understand our equipment, process state, to solve the problems of our operators. Never imagine the situation or previous situations, blindly trust your own experience and judgment.
Improper grasp of the current situation will only affect our management direction. A lot of people may find that the problem on the scene only comes from a small screw or switch after discussing and analyzing the anomaly. Blind complaints about the staff do not implement the process and equipment management is not in place, it is better to go to the site to correct training staff, it is better to help maintenance personnel tightly loose screws. The deterioration of quality is not terrible, terrible is the manager's armchair and indifferent. 80% of the problems come from the field, and 80% of the results come from the status quo.
What are we going to do about the current quality situation?
We have to be the leader of the scene, we have to break the functional boundaries, we have to grasp the status quo to develop the most effective countermeasures. The weakness of the process control force in the second factory leads to the uncontrolled process of our company, and the personnel and equipment are not in normal working condition.
Therefore, our managers and engineers are required to go to the site together to help the process control personnel to check the process execution, solve the practical problems faced by the operators, and help the equipment personnel to find the reasons for the equipment failure. To pay attention to the process and details of how we make our products. Perhaps the over-rot defects that have plagued us for many years come from small dry film scratches during the exposure process, and these causes are not something that we can analyze through slice analysis, EDX, or microscopy. The problems of the site come from the site, and the improvement of the site also comes from the site. Only by putting ourselves into the work of the site, as an ordinary operating staff, and feeling the state of the site, can we find the root cause of the quality problems.
Quality improvement is not nothing, it is a "do it now, grasp the situation, improve the scene" attitude and way of working, there is no secret, it just needs us to practice.