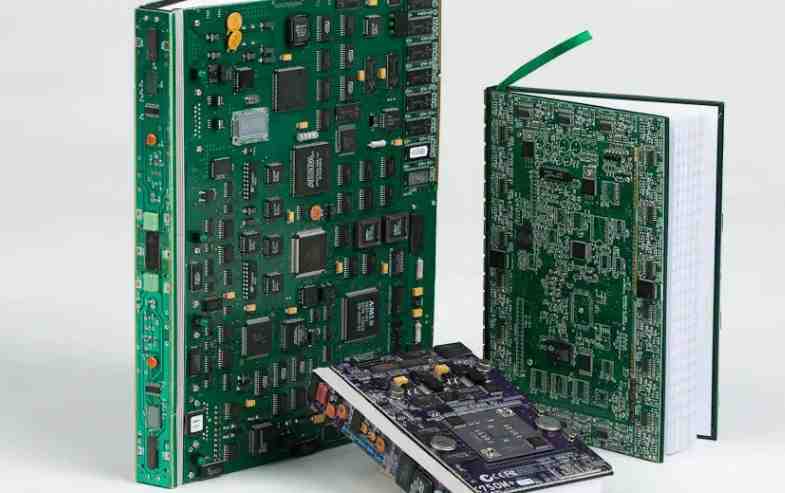
Usually, PCB made of soft insulating material is called soft PCB or flexible PCB, rigid flexible compound PCB is called rigid flexible PCB. It ADAPTS to today's electronic products to high density and high reliability, miniaturization, lightweight direction of development needs, but also meets the strict economic requirements and the needs of market and technical competition.
FPC flexible circuit board basic knowledge
Soft PCBS are usually classified according to the number of layers and structure of conductors as follows:
1.1 Single-side soft PCB
Single-sided soft PCB, with only one conductor, with or without a covering layer.
The insulating base material used varies with the application of the product.
Commonly used insulating materials are polyester, polyimide, polytetrafluoroethylene, soft epoxy-glass cloth
Single-sided soft PCB can be further divided into the following four categories:
1) Single-side connection without overlaying layer
The wire pattern of this kind of soft PCB is on the insulating substrate, and there is no covering layer on the surface of the wire.
Like the usual one sided rigid PCB.
These products are the cheapest and are usually used in non-critical and environmentally friendly applications.
The interconnection is realized by solder welding, fusion welding or pressure welding. It was commonly used in early telephone sets.
2) It is connected by a single covering layer
Compared with the previous class, this kind of wire is only covered with a layer on the surface according to customer requirements.
Cover the pad should be exposed, simple can not cover the end area.
Requirements of precision can be used in the form of clearance holes.
It is one of the most widely used single-sided soft PCB, and it is widely used in automobile instrument and electronic instrument.
3) Double-sided connection without covering layer
This type of connecting disk interface can be connected on the front and back of the conductor.
For this purpose, a path hole is cut in the insulating substrate at the pad. The path hole can be made by first punching, etching or other mechanical methods at the desired position of the insulating substrate.
It is used for double-sided mounting elements, devices, and where soldering is required. There is no insulating substrate in the pad area at the access point. Such pad area is usually removed by chemical methods.
4) Double-sided connection with covering layer
This class differs from its predecessors in that it has a covering layer on the surface. But the overlay has access holes that allow it
Both sides can be terminated and still maintain a covering layer.
This type of soft PCB is made of two layers of insulation and one layer of metal conductor.
It is used in the case that the covering layer is required to be insulated from the surrounding device, and itself is required to be insulated from each other, and the ends need to be connected on both sides.
1.2 Double-sided soft PCB
Double-sided soft PCB with two layers of conductors.
The applications and advantages of this type of double-sided soft PCB are the same as those of single-sided soft PCB, the main advantage of which is increased wiring density per unit area.
It can be divided into a, no metallized hole and no covering layer: a, no metallized hole, no covering layer; b without metallizing holes and with covering layer; c with metallized holes and no covering layer; d Having metallized holes or overlying layers. Double-sided soft PCBS without overlay are rarely used.
1.3 Multi-layer soft PCB
Soft multilayer PCB is like rigid multilayer PCB
Multilayer soft PCB can be made by using multilayer compaction technology.
The simplest multilayer soft PCB is a three-layer soft PCB formed by two layers of copper shielding on both sides of a single-sided PCB.
This three-layer soft PCB is electrically equivalent to a coaxial wire or a shielded wire.
The most commonly used multilayer soft PCB structure is a four-layer structure, with metallized holes to realize interconnect between layers, and the middle layer is generally the power layer and ground layer.
The advantages of multilayer soft PCBS are that the substrate film is light in weight and has excellent electrical characteristics, such as low dielectric constant. The multilayer soft PCB board made of polyimide film as the base material is about 1/3 lighter than the rigid epoxy glass cloth multilayer PCB board, but it loses the excellent flexibility of single-sided and double-sided soft PCB. Most of these products do not require flexibility.
1. Flexible circuit board FPC plating
(1) FPC electroplating flexible printed board FPC after coating layer process exposed copper conductor surface may have adhesive or ink pollution, but also due to high temperature process oxidation, discoloration, in order to obtain good adhesion tight coating must be the conductor surface pollution and oxide layer removal, so that the conductor surface clean. But some of these pollution and copper conductor combination is very firm, with weak cleaning agent can not be completely removed, so most often use a certain strength of alkaline abrasive and brush and treatment, covering adhesives are mostly epoxy resins and poor alkali resistance, which will lead to a decline in bonding strength, although not obviously visible, but in the FPC electroplating process, The bath is likely to penetrate from the edge of the covering layer, serious will make the covering layer peel. During the final welding, the solder drill went under the covering layer. It can be said that the pretreatment cleaning process will have a great impact on the basic characteristics of the flexible printed board F{C, so we must pay full attention to the treatment conditions.