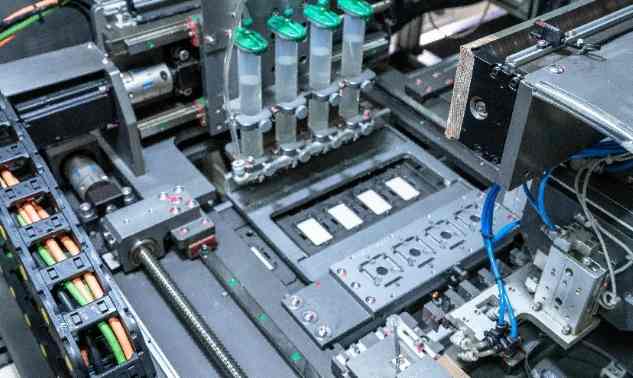
The plating tank also has internal or external causes to produce bubbles.
A. The internal causes of bubbles
Fortunately, acidic copper plating tanks have high cell efficiency, so there is little question of hydrogen production in the better tanks. Conditions that are likely to lead to hydrogen generation need to be avoided, such as high current density and rectifier fluctuations resulting in a short period of large current density drift. Some of the tin/lead tanks or the tin tanks are less efficient than the copper tanks and hydrogen production becomes an important problem. An interesting development in avoiding the generation of hydrogen separation is the addition of "antipititting additives". These organic compounds, such as derivatives of caprolactam, may participate in REDOX reactions, stripping away the atomic hydrogen before forming hydrogen molecules, preventing bubbles from forming. The reduced pitting additive is reoxidized at the anode and transferred to the cathode, starting the cycle all over again.
B. External causes of bubbles
The most obvious external cause of bubbles is the air bubbles that fill the holes before the board is immersed in the solution. In order to dislodge air from the hole before the board is immersed in the tank, some plating fixture designers have experimented with creating an Angle between the board and the fixture. Sufficient difference in pressure can be created to drive the bubbles out of the hole. Using compressed air to stir liquid through the board through a sprayer (air sparging) also helps drive away bubbles. Of course, spray mixing itself is also a kind of gas. When mixed into the tank, the air enters the circular filter pump to produce a susaturated liquid flow. Bubbles will be formed in the assembly position, and bubbles will also be formed in the hole wall defects. Some manufacturers are troubled by this problem and have turned to airless agitation (solution injection).
In addition to corrosion residuations and bubbles that hinder electroplating, other obvious problems that cause electroplating cavities are: poor penetration and foreign body blockage. A poorly penetrating tank will result in no copper in the middle, but this is a very extreme case. Usually the hole center copper thickness is not enough to meet the acceptable standard. In acidic copper plating tank, there are several reasons for poor penetration: improper copper/acid ratio, tank contamination, less or insufficient organic additives, poor current distribution, shielding effect or agitation, etc. If particle pollution is found, it is mostly caused by the failure of circulation or filter pump, the frequency of recirculation is too low, the damage of anode bag or the defect of cathode film.
7. Holes caused by copper etching
If there is any problem with the metal resist in the plating, the copper in the through hole will be exposed to the etching agent, resulting in cavitation. In this case, the cavity is caused by copper being etched away rather than not deposited. This is a little out of order, but it is still important to emphasize the reason why the copper is etched away, creating the void.
The first possible condition that may cause copper loss is if there is residual moisture in the hole during chemical deposition of copper, if it is left too long before the next operation, or if there is a corrosive atmosphere, the copper will be oxidized and dissolved in the pre-leaching step before acid copper plating. Another possibility is excessive microerosion before plating. Secondly, the copper of chemical precipitation may fall off. It can be seen in the samples made of metallography directly after chemical copper deposition or after thermal shock. The causes of this kind of cavity are: improper composition of chemical copper sink, entraining of treatment solution, poor adhesion of chemical copper due to decontamination, catalysis, or improper adjustment of accelerators.
When hole wall copper defects (cracks, shedding) occur during wave soldering, hot air leveling, or other high temperature reflow welding procedures or simulated thermal stress tests, the root causes of such problems are often traced to the hole wall pretreatment and initial metallization steps.
Pore wall cavities can have many causes. According to the manufacturing process, which can be traced back to previous steps such as drilling, it can also occur during lead/tin plating. But the shape and location of the void can often provide clues to the source of the problem. The cavity in the pore wall is often produced by the interaction of various technological conditions. They may act simultaneously or have a sequence. It is possible to find the root cause by carefully analyzing the defect characterization along the process steps.