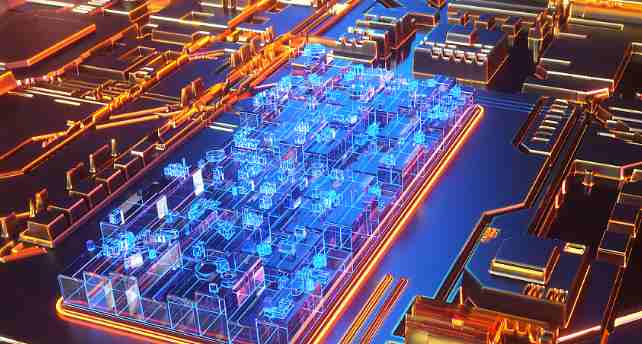
1 -- tin-dipping action
When hot liquid solder dissolves and penetrates the surface of the metal being welded, it is said to be tin-dipping or tin-dipping of metal. The molecules of the mixture of solder and copper form a new alloy that is partly copper and partly solder. This solvent action is called tin-dipping, which forms intermolecular bonds between the various parts to form a metal alloy copide. The formation of good intermolecular bond is the core of welding process, which determines the strength and quality of welding points. Only the surface of copper is not contaminated, no oxide film formed by exposure to the air can be stained with tin, and the solder and working surface need to reach the appropriate temperature.
2 -- surface tension
Everyone is familiar with the surface tension of water, the force that keeps cold water droplets spherical on a greased sheet of metal because, in this case, the adhesion force that causes the liquid to tend to diffuse on a solid surface is less than its cohesion. The surface tension is reduced by cleaning with warm water and detergent. The water will saturate the greased metal and flow outward to form a thin layer. This happens if the adhesion is greater than the cohesion.
The cohesion of tin-lead solder is even greater than that of water, forming the solder into a sphere to minimize its surface area (the sphere has the smallest surface area compared to other geometries for the same volume to meet the requirements of the lowest energy state). The action of the flux is similar to that of the cleaner on the greased metal plate. In addition, the surface tension is also highly dependent on the cleanliness of the surface and temperature. Only when the adhesion energy is much greater than the surface energy (cohesion), can the ideal tin-sticking occur.
3 - The generation of metal alloy commides
The intermetallic bonds between copper and tin form grains whose shape and size depend on the duration and strength of the temperature at the time of welding. Less heat during welding can form fine crystalline structure, forming excellent welding points with optimal strength. Too long a reaction time, whether due to too long welding time or too high temperature or both, will result in a coarse crystalline structure that is gritty and brittle with low shear strength.
With copper as the metal base material and tin - lead as the solder alloy, lead and copper will not form any metal alloy copulates, however, tin can penetrate into copper, and the molecular bond between tin and copper forms metal alloy copulates Cu3Sn and Cu6Sn5 at the joint surface of solder and metal, as shown in the figure.
The metal alloy layer (n phase +ε phase) must be very thin. In laser welding, the thickness of the metal alloy layer is of the order of magnitude of 0.1mm. In wave soldering and manual soldering iron welding, the thickness of the metal bond between the excellent welding points is more than 0.5μm. Since the shear strength of the welding point decreases with the increase of the thickness of the metal alloy layer, it is often tried to keep the thickness of the metal alloy layer below 1μm, which can be achieved by making the welding time as short as possible.
The thickness of the common layer of the metal alloy depends on the temperature and time at which the welding point is formed. Ideally, the welding should be completed in about 2s of 220't. Under these conditions, the chemical diffusion reaction of copper and tin will produce appropriate metal alloy bonding materials Cu3Sn and Cu6Sn5 with the thickness of about 0.5μm. Inadequate intermetallic bonding is common in cold welding contacts or welding points that are not raised to the proper temperature during welding. It can lead to cutting of the welded surface. Conversely, too thick a layer of metal alloy, which is commonly seen in the welding points of excessive heating or welding for too long, will result in very weak tensile strength of the welding points, as shown in the figure.
4 -- tin Angle
At temperatures approximately 35 ° C above the eutectic point of solder, a meniscus is formed when a drop of solder is placed on a hot flux-coated surface. To some extent, the ability of a metal surface to stick tin to the meniscus can be assessed by its shape. The metal is not weldable if the solder mensurus has a distinct bottom cut, like a bead of water on a greased metal plate, or even tends to be spherical. Only the meniscus stretches to a surface less than 30. The small Angle has good weldability.