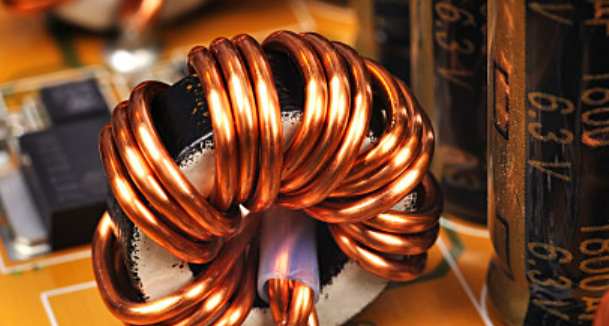
If the product use quality is poor, use time is short, it is easy to be eliminated by the market, only grasp the quality of the product, in order to play a greater market competitiveness, because almost all electronic products will use PCB board, so now more and more electronic product manufacturers on the three-proof paint demand is particularly important, The purpose is to protect the circuit board, components and printed wires from being infringed, so as to ensure the service life.
So what if PCB board is not coated with three anti - paint? Xiaobian and you talk about a few aspects, please understand.
First, the patina phenomenon
Patina is also called copper rust, then PCB board patina is how to come? First of all, we need to know the cause of the patina of PCB circuit boards. Moisture is the most common and destructive main factor to PCB circuit boards.
Therefore, if the PCB board is in a humid environment for a long time, coupled with the action of oxygen and carbon dioxide, the copper on the PCB board begins to produce chemical reactions, rust and produce patina, and eventually the board will not be able to work. Solution, use PCB three anti - paint, electric anti - adhesive.
Two, leakage or short circuit phenomenon
How does the phenomenon of electric leakage come about? Electrical circuit due to no protection, for a long time after the accumulation of dust, because the dust is easy to absorb moisture, moisture dust resistance will be reduced, making the local leakage wire, easy to cause the control circuit work is not normal or even heat fire.
For example, we often use the computer, for a long time, the boot is not normal, clean up the circuit board, and can start normally, because the circuit board is covered with too much dust and no three anti-paint protection caused by the circuit board, in serious cases, cleaning is useless, only directly replace the main engine. So to prevent the product leakage or short circuit phenomenon solution, the use of PCB three anti-paint, electric anti-adhesive.
3. Influence of finger marks or sweat
Almost every link of PCB board manufacturing runs through manual operation, and the risk of contamination is greater, especially sweaty hands. We can understand what components sweat finger prints have, which generally include moisture, inorganic salts, fats and oils, some people like makeup and cosmetics, skin care products and so on. They are left in components, component pins, welding lines and other places, coupled with the effect of the external environment. In short, after 2 or 3 months, the surface of the circuit board will appear moldy components, component pins will be corroded and broken, and so on. Therefore, after the PCB board is manufactured, the board surface is cleaned and the three-proof paint is sprayed, which can ensure that all aspects of the PCB board used on the product work normally after the assembly process. Therefore, to solve the harm caused by finger printing, or the use of PCB three-proof paint and electric proof glue.
So if PCB board is not coated with three anti paint, electric anti adhesive, wait until the market returns, slight repair and rework, serious scrap, the cost of loss is much higher than the cost of using three anti paint, because of environmental changes and product use of different areas, do not use three anti paint can not avoid PCB board and environmental hazards contact, such as heavy humidity in the south, especially in the return of moisture, Seaside salt fog heavy, chemical heavy local chemical damage heavy and so on.
PCB board does not use three anti-paint harm, the above is only a small part, more detailed understanding, please consult the manufacturer.
These are pcb board color pay attention to
The color of PCB board, as the name implies, after getting the PCB board, the most intuitive to see the oil color on the board, is the color of PCB board we often say, common colors are green, blue, red, black and so on. The following Xiaobian to share their understanding of different colors.
Green ink is by far the most widely used, the oldest, and the cheapest on the market today, so it is used by a large number of manufacturers as the main color of their products.
In general, the whole PCB product must go through the process of board making and SMT in the production process. In the process of board making, several processes must go through the yellow light room, because the effect of green in the yellow light room is better than that of other colors, but this is not the main reason. When SMT is used to solder components, the PCB goes through processes such as solder paste, patch, and final AOI verification. These processes require optical alignment and have a green background color for instrument identification. Common PCB color for red, yellow, green, blue and black three. However, due to the production process and other problems, the quality inspection process of many lines still relies on workers to observe and identify with the naked eye (of course, most of the current use of flying needle detection technology). Eyes keep staring at the board under strong light, which is a very hard work process, relatively speaking, green is the least harmful to eyes, so most manufacturers on the market are using green PCB.
The principle of blue and black is that they are mixed with cobalt and carbon respectively, which have certain conductivity and are prone to short-circuit problems when powered on. Compared with green PCB, green PCB is more environmentally friendly and will not release toxic gases when used in high temperature environment. And there are a few manufacturers on the market will use black PCB board, which is mainly because the small editor believes that there are two reasons: one is because the PCB board looks more high-grade; Second, the black plate is not easy to see the wiring, so it is more difficult to copy the board. The author learned that the Android embedded board mostly uses black PCB.
About from the middle and late last century, the color of the circuit board has attracted the attention of the industry, mainly because the color design of many high-end circuit boards are made of green, so people slowly believe that the color of the circuit board is green must be high-end.