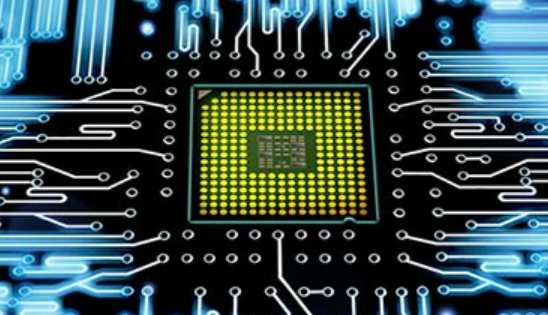
Circuit boarddeformation hazard.
In the automatic surface mounting line, if the circuit board is not smooth, it will lead to inaccurate positioning, components can not be inserted or affixed to the orifice and surface mounting pad of the board, and even crash the automatic mounting machine.
After the circuit board is connected with the components, it will be bent, and the feet of the components are not easy to be cut flat. Panels can't fit into the case or socket, so assembly plants are equally bothered by the warped panels.
The current surface assembly technology is developing towards the direction of high precision, high speed and intelligence, which requires higher flatness of PCB board, which can be used as the main component of various components.
In particular, the IPC standard states that the allowable deformation of PCB board with surface mount device is 0.75%, while the allowable deformation of PCB board without surface mount device is 1.5%.
In practical application, in order to meet the requirements of high precision and high speed mounting, some electronic assembly manufacturers have stricter requirements on the amount of deformation, such as the required deformation allowance of 0.5%, or even individual requirements of 0.3%.
Printed circuit board is composed of copper foil, resin, glass cloth and other materials, their physical and chemical properties are different, pressing together will inevitably produce thermal stress, resulting in deformation.
At the same time, PCB board in the process of processing, will experience high temperature, mechanical cutting, wet process and other processes, will also have an important impact on the deformation of the board, PCB board deformation causes are complex and changeable, how to reduce or eliminate the deformation caused by different material characteristics or different processing technology, has become one of the difficult problems for PCB manufacturers.
Cause analysis of circuit board deformation.
The deformation of printed circuit board needs to be studied from the material, structure, graphic distribution, processing technology and other aspects. This paper will analyze and elaborate various causes of deformation and improvement methods.
The copper area of the plate is uneven, so that the bending and warping of the plate are worse.
Usually a large number of copper foil will be designed on the circuit board as grounding, sometimes Vcc layer will also design a large number of copper foil, when these large numbers of copper foil can not be evenly distributed on the same circuit board, it will produce the problem of heat absorption and heat dissipation is not uniform.
Of course, the circuit board is also thermshrinkable. If the thermal shrinkage cannot cause deformation under different stresses at the same time, then the temperature of the board reaches the upper limit of Tg value, the board will begin to soften and cause deformation.
The joint points (vias, through holes) of the layers on the circuit board will limit the lift of the board.
Modern circuit board is mostly multi-layer board, there will be the same joint point between the plate and the rivets, the joint point is divided into through holes, blind holes and buried holes, where the joint point will limit the effect of the board cooling contraction, will also indirectly lead to the bending and warping of the board.
Causes of circuit board deformation:
The weight of the board itself dents and deforms the board.
Usually the backweld furnace is a chain structure, which can push the circuit board forward, that is, to support the entire board on both sides of the board as a fulcrum.
If there are too heavy parts on the board, or the size of the board is too large, it will be due to its own number and the phenomenon of the middle depression, causing the bending of the board.
The depth of V-Cut and the connection strip will affect the deformation of the plate.
Fundamentally speaking, V-Cut is the culprit of damaging the structure of the board, because the V-Cut is slotted on the original large board, so it is easy to produce deformation at the V-Cut.
Influence degree of crimping material, structure and figure on plate deformation:
The circuit board is made of core board, semi-cured sheet and outer copper foil pressed together. The core board and copper foil are deformed by heat in the pressing process. The amount of deformation depends on the coefficient of thermal expansion (CTE) of the two materials.
The thermal expansion coefficient (CTE) of copper is about 17X10-6. The thermal expansion coefficient (CTE) of FR-4 substrate is about (50~70)X10-6. The thermal expansion coefficient (250~350) and x-direction CTE of ordinary FR-4 substrates are generally similar to copper foil due to the presence of glass cloth.
Distortion of the circuit board during processing.
The causes of deformation in circuit board machining are very complex, which can be divided into thermal stress and mechanical stress.
Among these stresses, the thermal stress is produced when pressing, and the mechanical stress is produced when the plate is stacked, transported and baked. A brief discussion follows the process sequence.
I. Copper coated raw materials:
Copper clad plates are double-layer panels, symmetrical structure, no pattern, copper foil and glass cloth CTE is far from each other, so there is little deformation caused by different CTE when pressing.
However, due to the large size of the copper clad plate press and the temperature difference between different areas of the hot plate, the curing speed and degree of the resin in different areas are slightly different in the pressing process. Meanwhile, the dynamic viscosity varies greatly under different heating rates, so local stress in the curing process will also be generated.
In general, the stress remains in equilibrium after pressing, but gradually releases during the later machining process, forming deformation.
Two, pressing:
The pressing process of printed circuit board is the main process of generating thermal stress. Similar to the pressing process of copper clad plate, it will also produce local stress caused by inconsistency in the curing process. The printed circuit board is more difficult to eliminate thermal stress than copper clad plate due to its thicker thickness, more patterns and more semi-cured sheets.
In addition, the stress on the PCB board will be released in the subsequent drilling, forming or baking process, resulting in the deformation of the board.