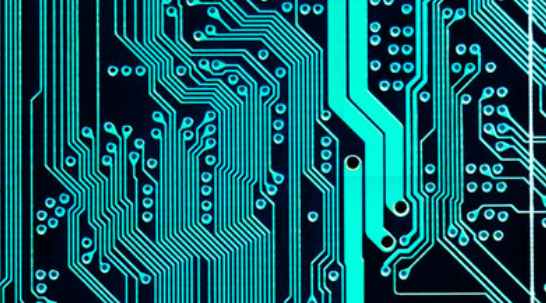
High speed products pay more attention to the dielectric loss (Df) of the plate. The grade of high speed materials commonly used in the market is also divided according to the size of the dielectric loss (Df). Different substrate materials can be divided into conventional loss, medium loss, low loss, very low loss and ultra-low loss according to the dielectric loss of substrate. Five levels of transmission loss.
High frequency material properties
Compared with high speed materials, high frequency materials pay more attention to the size and variation of material dielectric constant (Dk). High-frequency products are very sensitive to changes in the dielectric constant (Dk) of the material. Therefore, high frequency materials focus on the stability of dielectric constant (Dk), as well as the thickness of the material medium, the temperature drift coefficient of the material, and the ststrobe properties of the material. There is no clear classification standard for high-frequency materials in the industry, but many PCB manufacturers roughly classify high-frequency boards according to the dielectric constant (Dk) of the material. Materials with the same dielectric constant (Dk) are considered similar and can be substituted for each other.
In the field of high-frequency materials, there is also a conventional division of materials into PTFE and non-PTFE materials. This is closely related to the application field of high-frequency products. The current RF field can be divided into two parts. First, the frequencies below 6GHZ are commonly used in 3.5GHZ, 2.7GHZ and 1.8GHZ. The main products are power amplifier, antenna calibrator, and other products. The other part is over 20GHZ millimeter wave field commonly used frequencies are 24GHZ, 66GHZ, 77GHZ, the main products are radar products. This is mainly because with the increase of frequency, the stroboscopic effect and dielectric loss of non-PTFE products on signal transmission increase sharply, and PTFE materials have better performance characteristics.
Three, high frequency and high speed board development prospects
Traditional copper-clad materials have high transmission loss and can not meet the requirements of high frequency signal transmission quality. Therefore, the most important performance of PCB substrate materials used in 5G communication is to meet the requirements of high frequency and high speed, as well as integration, miniaturization, lightweight, multi-function and high reliability. In particular, resin materials require low dielectric constant (Dk), low dielectric loss (Df), low thermal expansion coefficient (CTE) and high thermal conductivity. At present, the hard copper clad plate represented by polytetrafluoroethylene (PTFE) thermoplastic materials and hydrocarbon resin (PCH) thermosetting materials, because of its incomparable low dielectric properties occupy the majority of the high frequency/high speed PCB substrate market. In recent years, polyphenyl ether (PPO or PPE), bismaleimide (BMI), cyanate (CE), triazine resin (BT), benzoxazine (BOZ) and benzocyclobutene (BCB) and other new resin materials of high frequency/high speed PCB substrate.
Polyphenyl ether (PPO or PPE), whose dielectric property is second only to PTFE, has attracted much attention in the industry in recent years
In addition, PPO material's workability is much better than PTFE material, so at present high speed plate in Very Low Loss (Very Low Loss) and Ultra low loss (Ultra Low Loss) more modified PPO resin, such as Panasonic M6, M7N, Bimau IT968, IT988GSE. The resin system of high frequency plate is mainly composed of polytetrafluoroethylene (PTFE) thermoplastic material and hydrocarbon resin (PCH). Although very low dielectric loss (Df) and stable dielectric constant (Dk) can be obtained, poor material machinability is not suitable for high multilayer plate, much less suitable for HDI plate processed products.
With the development of 5G communication, PCB complexity of high-frequency products is also becoming higher and higher (traditional high-frequency PCB is mainly single and double sided, and the development of multilayer board even has HDI design requirements) in recent years, material developers also use PPO resin to make high-frequency board. To ensure the board has very low dielectric loss (Df) and stable dielectric constant (Dk) at the same time, to obtain good PCB processability. For example, Lianmao launched IT-88GMW, IT-8300GA, IT-8350G, IT-8338G, IT-8615G and other high-frequency plate is the use of modified PPO resin and hydrocarbon resin mixed system. While meeting the high frequency signal transmission requirements, the machinability of the material is greatly enhanced.
On the one hand, the development of 5G communication towards higher speed and higher frequency will inevitably require the dielectric loss (Df) and dielectric constant (Dk) of materials to be smaller. On the other hand, 5G products require miniaturization and more unified PCB corresponding to the development of high multilayer or even HDI direction, which requires good machinability of materials. At present, the use of polyphenyl ether (PPO or PPE) resin is a good development direction, whether from high frequency materials or high speed materials.