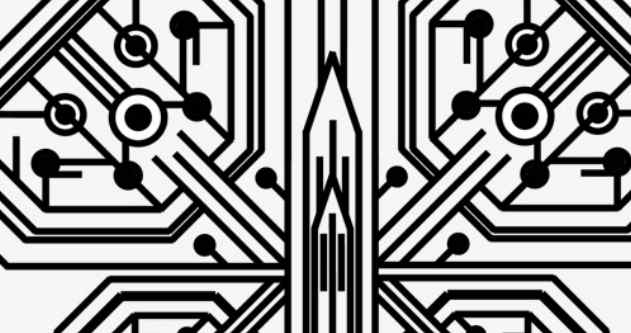
In the production process of the whole machine, it can not be continuously found that the boot phenomenon, after maintenance, the cause of the fault has a certain common, basically is the bottom of the power board between the solder joint sticky dirt, resulting in circuit leakage caused by fault. According to the preliminary analysis, it is caused by the sticking of tin furnace slag to the printed board during the over-wave soldering of the component board. However, because of the irregular occurrence of the problem, there are sometimes 3 ~ 5 cases a month. Sometimes half a year goes by without a problem; Moreover, when the bottom surface of the component board was found to be dirty, the component board basically had been all through wave soldering, and the production process could not be reproduced. Because of the uncertainty and contingency of the problem, the analysis of the cause of the problem caused a great deal of trouble, had to take the component plate after wave soldering, temporarily increase the washing process (the company uses no cleaning flux, the normal production of component plate without washing plate), in order to avoid quality hazards.
1. Harm of dirty component plate and solution
There are foreign bodies stuck on the bottom surface of the component plate. During the use of the product, due to the influence of environmental factors, electricity leakage will be formed between the solder joints through "foreign bodies". Slight leakage may cause the product to not work properly; Serious leakage will cause serious accidents such as equipment damage or even fire due to ignition between welding spots. On the other hand, because of the fast production line operation speed, the "dirty" problem of the board is contingent, and the production process cannot be completely controlled. If the cause of the dirty parts of the board cannot be found, the hidden danger of quality cannot be eliminated.
After more than a year of tracking and analysis, the "real culprit" that led to the dirty component board was finally identified, which was mainly caused by some aspects of equipment failure or design defects. The following will give a detailed description one by one for the reference of all practitioners when they encounter similar problems.
2 Trace and analyze the dirty causes of the component plate
2.1 Peak nozzle turbulence wave and small distance between waves At the beginning of lead-free process, in order to ensure the reliability of solder joints, the excessive pursuit of the time difference between the two peaks welding, as far as possible to reduce the distance between the two peaks, but this has led to a problem. Because of the small distance between the two wave peaking nozzle, the tin flowing down during welding and the tin slag on the surface of the tin collided at the bottom of the wave peaking nozzle, causing the tin slag to flow upstream along the tin flow and flow to the welding surface of the component plate, thus sticking to the component plate surface, resulting in failure.
In order to solve this problem, in addition to the comprehensive upgrade and replacement of the crest solder furnace, the simple way is to transform the crest nozzle, after discussion with the equipment manufacturer, under the premise of not affecting the quality of welding, the peak nozzle and the distance between the spoiling nozzle and the wave nozzle is increased by 10 mm, to completely solve the problem.
2.2 The tin furnace motor is not firmly fastened
In a tin furnace maintenance process, it was found that when the tin furnace motor was rotating, the coupling connecting the motor and the tin wave generator was shaking and unstable. After the coupling was removed, it was found that the bolt and fixed screws were loose and slipping, resulting in the lower coupling floating up and down. Further analysis, because the motor coupling pin of the tin furnace is short, it is easy to slip and loosen due to operation problems when fixed. After the lower coupling floats up and down, it is easy to cause the tin slag to be sucked into the wave source generator from the surface of the tin liquid, and transported together with the tin liquid to the welding surface of the component plate, resulting in the dirty problem of the plate. Solution: Make a long bolt, replace all the wave soldering furnace, avoid the quality hidden trouble caused by the operation problem.
2.3 Tin furnace inner deformation crest soldering furnace is divided into inner and outer gallbladder, the outer gallbladder mainly plays the role of tin loading and heat conduction, the inner gallbladder mainly plays the role of fixing the crest nozzle and guiding the flow, in the process of tracking the parts of the plate dirty, it is found that the tin furnace inner deformation has a great impact on the plate dirty.
(1) When the plate dirty problem is found in the first production, it is found in the analysis process that the flat wave peak nozzle of the tin furnace has signs of loosening, causing the tin liquid to shake occasionally. At the shaking moment, more tin liquid rushes to the tin slag, causing the tin slag to splash on the component surface. After line stop maintenance, it is confirmed that because the bottom of the inner liner of the fixed crest nozzle is cracked, the width of the inner liner is enlarged, and the fixing nut of the crest nozzle is sliding. Remove the liner and weld to solve the problem.
(2) Because more tin liquid scour the tin slag caused the splash on the tin slag caused by dirty plate, a comprehensive overhaul of each wave soldering equipment tin furnace, found that some of the inner liner deformation phenomenon, so that the flow of tin liquid from the flat wave is easy to wash to the tin slag, the tin furnace liner replacement and transformation, thoroughly solve the problem of plate dirty caused by the fault.