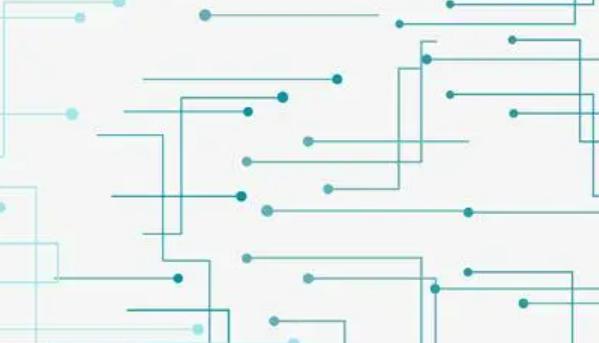
1. Short circuitof clip film:
1, anti-coating layer is too thin, electroplating because the coating exceeds the film thickness, the formation of clip film, especially the smaller the line spacing, the easier to cause short circuit clip film.
2, the plate graphic distribution is not uniform, isolated several lines in the process of graphic plating, because of high potential, the coating exceeds the thickness of the film, the formation of clip film resulting in short circuit. Improvement methods: (1) Increase the thickness of the anti-coating: choose the appropriate thickness of the dry film, if it is wet film can be printed with low mesh screen, or by printing wet film twice to increase the thickness of the film.
(2) The pattern distribution of the plate is not uniform, which can properly reduce the current density (1.0~1.5A) electroplating. In daily production, we usually control plating time as short as possible in order to ensure the output. Therefore, the current density used is generally between 1.7 and 2.4A, and the current density obtained in the isolated area will be 1.5 to 3.0 times of that in the normal area. Often cause the isolated area on the small distance of the local coating height exceeds the film thickness a lot, after the film is removed, the film is not clean, serious will appear the line edge clamping anti-coating phenomenon, resulting in short circuit film, at the same time will make the line on the welding resistance thickness thin.
Ii. Invisible micro short circuit: Invisible micro short circuit is the most troubled problem for our company and was once the most difficult problem to solve. Among the finished plates with problems in the test, about 50% belong to this kind of micro short circuit, which is mainly caused by the existence of invisible metal wires or metal particles in the line spacing. Improvement method:
1, because of welding resistance before grinding board is using physical coarsening, grinding brush mark depth is generally between 0.3~1.5μm, grinding board process due to the board edge along a large number of metal debris attached to the surface, pressure washing part of the water is not washed clean, attached to the surface of the sponge absorbent roller behind the water, when the back of the board, then metal debris may be attached to the surface, As a result, the finished board has many invisible short circuit phenomenon, so in order to avoid this phenomenon, we must regularly clean the sponge suction roller, which is very important, but also very easy to be neglected!
2, the washing water behind the grinding plate should be replaced regularly to ensure that the water in the washing cylinder is clean.
3. Clean and maintain the grinding machine regularly (with 3~5% NaOH solution and 3~5% H2SO4 solution respectively), clean the accumulation of copper powder in the sink and the microorganisms in the water, clean the inside of the air drying section and the filter of the fan regularly and keep clean.
Three, fixed short circuit: the main reason is that the film line is scratched or coated screen there is garbage blocking, coated anti-coating fixed bit exposed copper short circuit. Improvement method:
The film negative shall not have trachoma, scratches and other problems. The film surface shall be upward when placed and shall not be rubbed with other objects.
2, when the film is facing the board, take the film with both hands to pick up diagonally, do not encounter other objects, avoid the film surface scratches, each filin board to a certain number of people must stop to check or replace the position, after use into the appropriate film film bag for preservation.
3. Operators shall not wear any decorations such as rings and bracelets on their hands. Nails shall be trimmed and kept smooth.
4, before the production of the screen version must be strictly checked to ensure that the screen version without obstruction phenomenon, coated wet film often spot check, check whether there is garbage plugging screen version. When there is no printing at an interval of time, the empty screen should be printed several times before printing, so that the diluent in the ink is fully dissolved and solidified ink, to ensure the smooth oil leakage of the screen version.
Four, scratch short circuit:
1. Scratches after coating wet film, and scratches on film surface caused by improper operation during alignment.
2. The developer outlet plate is not busy enough to cause collision and scratch between the plate and the plate.
3. Improper plate taking during electroplating, improper operation on the splint, improper operation during manual pretreatment of the plate, etc., resulting in scratches.
2, improvement method: (1) Because of the wet film coating in the board easy to cause scratches, so the board and the board had better be far apart, to ensure that the surface of the board without scratches. Counterpoint when hands take, put the board, strictly avoid board and board superimposed together, or board and counterpoint table friction, avoid scratching the board surface
(2) When developing, adjust the spacing distance of placing the board according to the size of the board and the operation ability of the person receiving the board. When no one is connecting the board at the exit of the board, the machine cannot place the board at the place where the board is placed. When connecting the board, the board is stuck with both hands to avoid the collision between the board and the board resulting in scratches on the board surface.
(3) When electroplating, hands take and put the plate, avoid two or more plates stacked together for splinting, manual line plate to avoid friction between the plate and the table, manual line before processing of the plate can not be too much, a clip a clip over the plate to avoid collision.