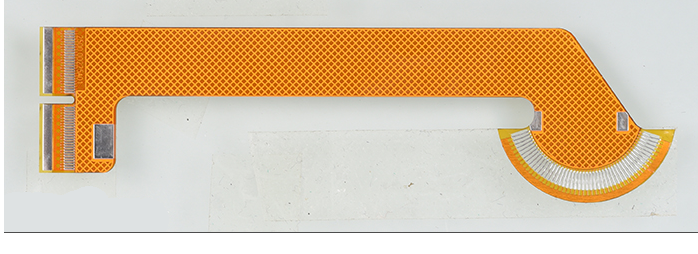
1. Flexibility and reliability of flexible PCB
Four types of flexible PCB are currently prevalent: single-sided, double-sided, multi-layer and rigid-flex combination. "Single-sided flex boards have the lowest cost. When electrical performance is not critical, and single-sided wiring is possible, single-sided flex boards should be used." This most common form has been used commercially, such as inkjet cartridges for printers and computer memory. The single-sided flexible board has a layer of chemically etched conductive patterns, and the conductive pattern layer on the surface of the flexible insulating substrate is rolled copper foil. Insulation substrates used for flexible assembly can be polyimide (Kapton), polyethylene terephthalate (PET), aramid fiber paper (Nomex) and polyvinyl chloride (PVC).
The double-sided flexible board is a conductive pattern formed by etching on both sides of the base film. The metallized holes connect the patterns on both sides of the insulating material to form a conductive path to meet the flexible design and use functions. The cover film protects single and double-sided conductors and indicates where the components are placed.
The multi-layer flexible board is to laminate three or more layers of single-sided flexible PCB or double-sided flexible PCB together, and form metallized holes through drilling and electroplating, forming conductive paths between different layers. In this way, no complicated welding process is required. Although the number of such flexible conductive layers can be unlimited, when designing the layout, in order to ensure the convenience of assembly, the interaction of assembly size, number of layers and flexibility should be considered.
2. The economy of flexible PCB
If the design of the circuit is relatively simple, the total volume is not large, and the space is suitable, most of the traditional interconnection methods are more cost-effective. If the circuit is complex, handles many signals, or has special electrical or mechanical performance requirements, a flexible circuit board is a better design choice. Another potential cost-saving reason for flexible materials over rigid materials is the elimination of connectors. The cost of raw materials is the main reason for the high price of flexible PCB. Although its raw materials are expensive and difficult to manufacture, the foldable, bendable and multi-layer paneling functions will reduce the size of the overall assembly, reduce the materials used, and reduce the total assembly cost.
3. The cost of flexible PCB is being further reduced
Despite the above-mentioned cost factors, the price of flexible assembly is falling, becoming close to that of traditional PCB. This is mainly due to the introduction of newer materials, improved production processes, and changes to the structure. As an example, on rigid-flex board assemblies with many layers, the use of acrylic adhesives has been eliminated. Some newer materials now allow finer lines due to thinner copper layers. Thinner copper layers have led to ever lighter components, and thinner and lighter assemblies have led to flexible components that fit better into smaller spaces. Today, copper foils can be produced directly on the media without the use of adhesives. The copper layers of several microns that can be obtained by these techniques enable the industry to obtain fine lines with a width of 3 mil or even narrower. "By removing the adhesive from the flexible circuit board, the flexible circuit board is made flame retardant. This can both speed up the UL certification process and further reduce costs. As flexible PCB continue to rapidly evolve from their initial military industrial applications to In residential and consumer applications, achieving UL certification is even more important. Solder masks and other surface coatings for flexible boards have further reduced the cost of flexible assembly. During the past decade, some of these new materials and new processes have greatly reduced costs. At the same time, it is precisely because such products have been widely recognized and demanded that the cost of flexible materials is also falling.