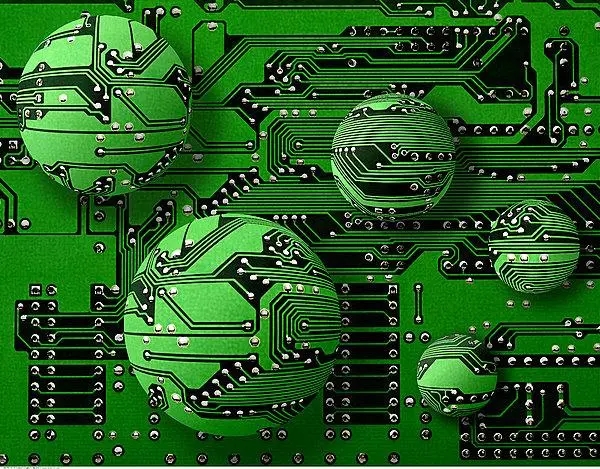
Liquid solder wetting in PCBA welding
In the process of PCBA welding, only when the molten liquid filler metal spreads on the metal surface, can metal atoms freely approach. Therefore, wetting the surface of the weldment with molten filler metal is the primary condition for diffusion, dissolution and formation of the bonding layer. This is also the most easily overlooked link in daily SMT processing detail control.
In the process of PCBA welding, only when the molten liquid filler metal spreads on the metal surface, can metal atoms freely approach. Therefore, wetting the surface of the weldment with molten filler metal is the primary condition for diffusion, dissolution and formation of the bonding layer. This is also the most easily overlooked link in daily SMT processing detail control.
Achieving Conditions and Influencing Factors of Liquid Solder Wetting in PCBA Welding
(1) Wetting conditions
① Liquid solder and base metal have good affinity and can dissolve each other. The mutual solubility between liquid solder and base metal depends on the lattICe type and atomic radius, so wetting is an inherent property of the material
② The surface of liquid solder and base metal is clean, free of oxide layer and pollutants. The clean surface makes the solder close to the parent metal atoms,
Generate gravity (wetting power). When there are oxide layers and other contaminants between the solder and the metal to be welded, they will prevent the free access of metal atoms and cannot produce wetting effect. This is one of the reasons for the formation of false soldering during chip processing.
(2) Factors affecting wetting power
① Surface tension: in the system where different phases exist together, the phenomenon that the phase interface always tends to be the minimum due to the different forces between the molecules at the phase interface and those in the bulk phase is calLED surface tension.
Since the force exerted on the internal molecules of the liquid by the surrounding molecules is symmetrical, the effect is offset by this, and the resultant force is zero. However, the liquid surface molecules are attracted more by the molecules in the liquid than by the atmOSPheric molecules, so the liquid surface tends to shrink to the minimum automatically.
Wetting is the force of liquid flowing across the solid surface. Surface tension is the force of liquid shrinking on the solid surface. The direction of surface tension is opposite to that of wetting force, so surface tension is not conducive to wetting. The molten solder also automatically shrinks to the minimum surface tension on the metal surface. Therefore, the wetness of molten solder on the metal surface is related to the surface tension of liquid solder.
② Viscosity: The viscosity is proportional to the surface tension. The greater the viscosity, the worse the fluidity of solder, which is not conducive to wetting.
③ Alloy composition: The viscosity and surface tension are different for different alloys and different alloy composition ratios. The viscosity and surface tension of Sn Pb alloy are closely related to the composition of the alloy.
④ Temperature: Increasing temperature can reduce viscosity and surface tension. Therefore, through the above analysis, we can learn that liquid solder wetting plays a very important role in PCBA welding, so SMT processing plants need to focus on this detail.