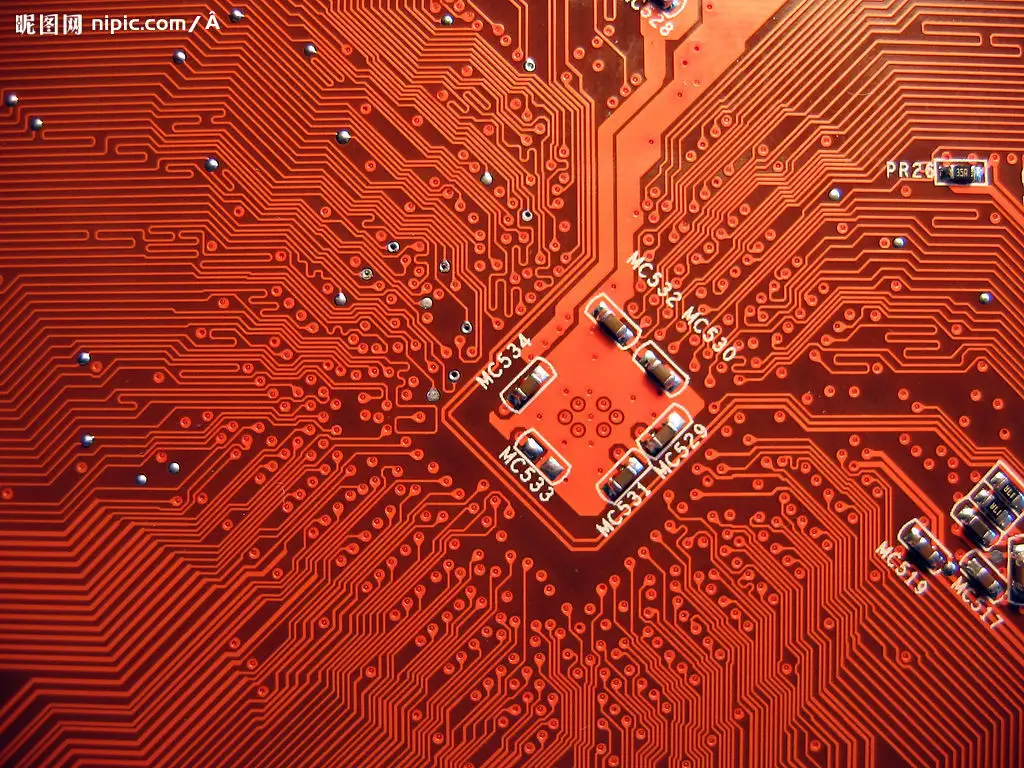
Nordson ASYMTEK has been the innovation and leader in the advancement of dispensing technology for Printed Circuit Board Assembly (also known as surface mount, SMT) -- from the early days of time-pressure pumps to SPIral valve systems to today's injection technology and closed-loop process control -- providing more options for balanced speed, volume control, precision and prICe.
Use bottom filler glue to reduce failure protection
Many large components on a mobile device board, such as a layered package (PoP), a ball grid array (BGA), and a Chip level package (CSP), require bottom-filling technology to avoid failure due to falling off. These components are very tightly distributed. Non-dispensing area (KOZ) is an important parameter to identify good bottom filling dispensing: the small bottom filling edging on the edge of the component must be densely distributed. A small drop of bottom filler glue must be applied close to the assembly, which requires a dispensing system to deliver a small amount of glue to the exact location. In addition, productivity is critical, so injection speed determines productivity.
Use a metal cap attachment for RF shielding
Mobile devices include many wireless components that need to be covered with RF shielding technology to protect them from interference. A metal cap is a more common material for RF shielding, where the cap can cover the components separately. But attaching the cap to the plate requires selective welding using a cryogenic solder paste: secondary welding. The key to high yield cap seal is to form a unique cap seal shape using fast and accurate solder paste dispensing technology.
Heat dissipation of hot end components
Many high-speed processors, amplifiers, and converters/inverters require efficient heat dissipation. Thermal interface materials (TIM) play an important role in transferring heat from the components to the heat sink or housing. Although there are many types of thermal interface materials, such as grease, gel, paste, liners, metal preforging, and phase transitions, many components that require high thermal capabilities use fluids such as grease, gel, and paste because they conduct heat better. The main performance characteristics of TIM glue are accurate, ultra-thin, wear resistance (TIM is rough) and high productivity. CPJ/MFC, Z-axis dispensing gap control, appropriate consumables combination and speed are suitable for this application.
Use accurate surface coating for moisture protection
Today, the use of mobile Electronic devices is everywhere, such as texting in the bathroom. Electronics must be protected from moisture by an ultra-thin, uniform polymer coating calLED surface coating. But electronics have a lot of interconnections and functional components beyond the device. Surface coating needs to avoid some areas, into some difficult to reach areas; This process is called selective coating. One of the key properties of surface coating equipment is selectivity and flow control for improved applications. Thin film coating, atomization coating, dispensing machine, valve rotation, tilt and other features solve these difficulties of surface coating.
Another problem is that the target assembly is too small to be solved by traditional spray coatings. There are many flexible circuits and micro components in mobile devices, such as 01005 capacitors, that need to be sprayed separately. Jet technology solves this problem and precision coating is applied.
circuit production can be manual, but the factory has basically realized mechanization, except for some large, heavy, abnormal body components, other direct plug-in components can be completed by automatic plug-in machine, plug-in speed is very fast, usually up to thousands to tens of thousands per hour. After the component is inserted, wave soldering is carried out, and the solder is welded up.
Now there are more dedicated to the patch components of the patch machine. First of all, brush a layer of solder paste on the solder plate of the circuit board, and then a little bit of red glue in the component, and then stick the component with the patch machine, the component will be stuck with red glue, will not fall off. After all pasting, reflow welding is performed, and the components are welded. The speed of the patch machine is also very high, generally can reach 40,000 to 160,000 per hour (resistance class), integrated circuit mount is slower.
If you want to know more specific, you can go to the Internet to find Wang Weiping teacher "electronic products manufacturing technology" book, Higher Education Press, there is a CD behind the book, a look will know.
Surface Mount Adhesive (SMA) for Assembly Reflux
features for this application.
During reflux, Surface Mount Technology (SMT) assumes that the component is in the correct position, even though the component may be on the back. Surface mount adhesive (SMA) plays an important role by holding the components in place on the printed circuit board. These components are often sparsely distributed on a large board. To increase productivity, the dispensing tip needs to move quickly between these scattered points without wasting time moving up and down due to sudden disconnection of the SMA fluid. Spraying technology and fast dispensing platform are the main features of this application.
The main dispensing applications to solve the printed circuit board assembly problems:
Solder paste seal for RF shielding
Bottom Fill Injection technique for BGA, CSP and PoP (Level 2)
Heat dissipation with TIM dispensing glue
Surface coating for moisture protection
Component reflux using SMA injection technology