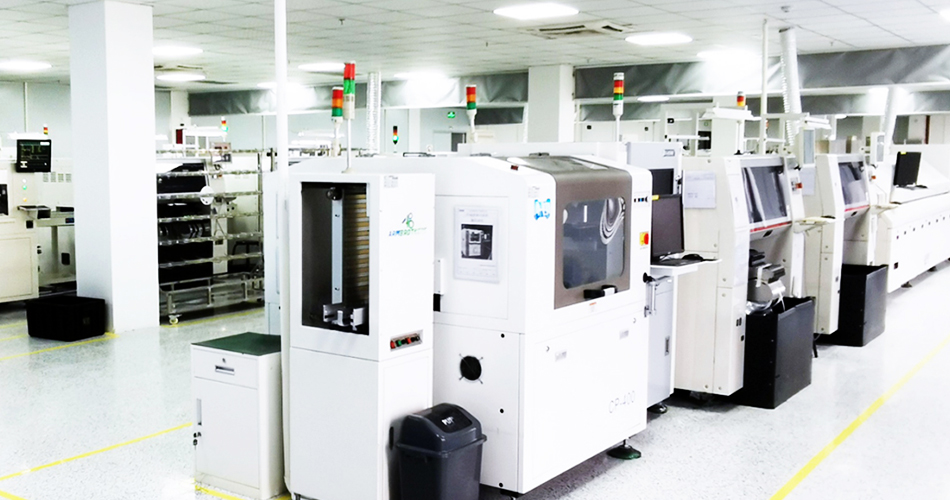
In the process of any PCB design and PCB manufacturer's production, design change, process change, process adjustment, unscheduLED line stop, production transfer, line transfer and other activities often occur.
Then, how to ensure that these activities will not affect the subsequent production quality? This requires the first artICle inspection in the stages of operation preparation verification and post production verification.
1. Definition of first article and first article inspection
Process change
During the production process, any one or more production factors in 5M1E (human, machine, material, method, environment, measurement) change, such as personnel change, equipment adjustment and maintenance, material change and fixture change, design change, line stop, etc.
What is the first piece?
The first or several products processed by the production line at the beginning of each shift/production line or after the process changes. For mass production, "first article" usually refers to a certain number of samples.
First article inspection
The inspection of the first or first products processed by the production line at the beginning of each shift or after the process changes. The inspection quantity can be determined according to the requirements of different enterprises or customers.
Generally speaking, at least 3-5 products produced continuously need to be inspected, and subsequent products can only be processed after they are qualified. In case of any change in equipment or manufacturing process, and before each work shift starts processing, the first article inspection shall be strictly carried out.
2. Purpose of first article inspection
The first article inspection in the production process is mainly to prevent the products from out of tolerance, repair and scrapping in batches. It is a means of pre controlling the production process of products, an important method of product process quality control, and an effective and indispensable method for enterprises to ensure product quality and improve economic benefits.
The first article inspection is to find out the factors that affect the product quality in the production process as early as possible, and prevent batch defects or scrap. The formal production can only be started after the first article passes the inspection, mainly to prevent the occurrence of batch nonconforming products.
Long term practical experience has proved that the first inspection system is an effective measure to find problems as early as possible and prevent products from being scrapped in batches.
Through the first article inspection, it can be found that there are systematic reasons, such as severe wear of fixtures or installation and positioning errors, poor accuracy of measuring instruments, wrong reading of drawings, feeding or formula errors, so as to take corrective or improvement measures to prevent the occurrence of batch nonconforming products.
3. Time/occasion of first article inspection
1. Start of each work shift;
2. Change the operator;
3. Replace or adjust equipment and process equipment (including tool replacement or grinding);
4. Change the technical conditions, process methods and process parameters (such as changes in roughness requirements, changes in reaming of internal holes to boring, changes in tool feed or speed in NC programs, etc.);
5. After using new materials or substituting materials (such as material changes during processing);
6. Replace or retest the bath solution (such as phOSPhating, nitriding, etc.).
Requirements for first article inspection
The first article inspection adopts the three inspection system: self inspection, mutual inspection and special inspection.
The products submitted for inspection must first be "self inspected" by the operator, then "mutual inspected" by the team leader or colleagues, and finally "special inspected" by the inspector. The subsequent products can only be processed after they are confirmed to be qualified.
Whether the first article is qualified after inspection shall be approved by the full-time inspector. The inspector shall MARK the first article that is qualified after inspection and keep it until the shift or a batch of products are processed.
All first product samples must be reserved for comparison of subsequent products to see if the process has changed, and marked with "√" with a marking pen to indicate that the first product inspection has been passed.
If the first article fails to pass the inspection, it is necessary to find out the cause and take measures. After troubleshooting, it is necessary to re process and conduct three inspections. It can be regarded as the first article until it is qualified.
4. Main items of first article inspection
1. Whether the drawing number is consistent with the work order;
2. Whether the materials, blanks or sEMI-finished products are consistent with the work order;
3. Whether the surface treatment, installation and positioning of materials and blanks are consistent;
4. Whether the formula ingredients meet the specified requirements;
5. Whether the actual quality characteristics of the first product after processing meet the requirements specified in the drawings or technical documents.
5. First article inspection specification process
The production department is responsible for organizing and arranging the first article inspection. The directly responsible person shall be responsible for the quality accident caused by the unauthorized production of products without first article inspection of new products, first article inspection of a batch or first article inspection of unqualified products.
The inspector and the person in charge of the production line are responsible for the correctness of the first article inspection. If the first article confirmation is not completed, the inspector starts to issue the quality certificate, and the inspector is responsible for the quality accident caused.
Control requirements
The first finished semi-finished products and finished products produced continuously for the first time by the production department must be inspected and confirmed by the first article.
For routine production products, the first article inspection shall be carried out by batch.
For the shutdown caused by equipment, process and other reasons, the first article inspection and confirmation shall be conducted when the shutdown is restarted.
The first article inspection and confirmation shall be carried out when the product materials and specifications are changed and put into production.
During the first article inspection of new products, the production unit shall be responsible for notifying the relevant inspection personnel to carry out the inspection according to the current effective drawings, lists (or samples provided by customers) and process documents. The inspector shall fill in the inspection records, sign on the first article card after passing the inspection, and hang the card on the first article to mark the first article.
If the first article fails to pass the inspection, it shall be returned immediately, and the first article shall be redone and recorded. Products that have not passed the first article inspection shall not be accepted.
The first piece, as a sample for mass production, shall be retained by the production department until the completion of full batch production. During the first article inspection, all raw and auxiliary materials used in the production process of the product shall be inspected and must conform to the regulations.
Working procedures
During the first article production process, the person in charge of the production line and the inspector shall go to the production site to supervise and inspect the actual producer to complete the first article according to the production process flow, according to the current effective production process documents, supervise and inspect each production process, and timely correct and solve the problems found.
All production processes must be completed for the first article of products produced in regular production and those produced after shutdown and restart. After the manufacturer has inspected and passed the inspection, the first article shall be signed on the first article board and then submitted to the inspector for the first article inspection.
During the first article inspection, the inspector shall, together with the person in charge of the production line, carry out the inspection according to the current effective drawings, lists (or samples provided by customers), process documents, and product requirements. After passing the inspection, the first article shall be marked (such as "qualified first article"), and the first article card shall be countersigned by the manufacturer (or representative) and the inspector.
The first article inspection required due to major product changes can be signed and approved by relevant personnel and inspectors; If the first article fails to pass the inspection, it shall be returned immediately and the first article shall be redone.
The first batch production of new products and the semi-finished products and finished products generated after the change of materials and specifications require the first article inspection and confirmation.
During the first article inspection, the first article record shall be made in time and the first article confirmation shall be filled in.
When quality problems are found in the first article production, they should be reflected and handled in a timely manner, and the nonconforming items should be reconfirmed. Production can be organized only after the first article is inspected as qualified, the results are recorded on the first article card, and the quality is approved by the inspector.
The inspector can start the normal delivery inspection only after the pcb manufacturer has confirmed the first article.